Плавка металлов и сплавов характеризуется сложными физикохимическими процессами, протекающими при высоких температурах. Процесс плавки состоит из физических преобразований исходных материалов и химических реакций, в которых участвуют составляющие сплава и флюсы, а также печные газы и футеровка печей. Сущность этих процессов подробно изложена в работах, посвященных теории металлургических процессов и производству сплавов. Здесь приведены только важнейшие сведения об особенностях технологии плавки сплавов, широко применяемых при литье по выплавляемым моделям.
В зависимости от рода футеровки сталеплавильных печей плавку стали ведут основным или кислым процессом. Основная футеровка печей позволяет выплавлять сталь с пониженным содержанием фос-.
фора й Сёры, что достигают применением активных шлаков с высоким содержанием извести.
Фосфор — вредный элемент в стали. Он образует фосфиды железа, вытесняет углерод из карбидов железа, придает стали свойства хладноломкости. Реакции окисления фосфора и дефосфорации идут в расплавленном металле (гомогенная реакция) и на поверхности раздела металл—шлак (гетерогенная реакция).
В печи с основной футеровкой окись кальция связывает пятиокись фосфора в химически устойчивое соединение — тетрафосфат кальция (СаО)
-я Р]> переходящее в шлак.
Сера — также вредный элемент в стали. Сульфиды железа, не растворяясь в твердом растворе, образуют хрупкую эвтектику по границам зерен и вызывают красноломкость стали в интервале температур 800—1200 °С. Процесс удаления серы (десульфурация стали) происходит в присутствии высокоосновного активного известкового шлака при высокой температуре.
Кислая футеровка печей разрушается основным известковым шлаком, поэтому известь при кислой футеровке применяют в ограниченном количестве. Кислые шлаки тугоплавки, малоподвижны. Удалить фосфор и серу в печах с кислой футеровкой практически невозможно. Однако сталеплавильные печи с кислой футеровкой имеют преимущества перед печами с основной футеровкой в долговечности и меньшей стоимости.
Подбирая шихту с малым содержанием серы и фосфора, можно успешно вести плавку в печах с кислой футеровкой. При плавке специальных сталей с высоким содержанием марганца, никеля, титана, алюминия и со строго ограниченным содержанием кремния происходит насыщение сплава кремнием, восстанавливающимся из кислой футеровки, что недопустимо.
".
Пр-и выплавке марганцовистых сплавов кислая футеровка быстро разрушается, так как закись марганца, реагируя с кремнеземом футеровки, образует легкоплавкий силикат марганца. Алюминий и титан восстанавливают кремний из футеровки. Никелевохромовые сплавы, выплавляемые в кислой печи, загрязняются мелкодисперсными включениями кремнезема («кремнистая муть»), которые иногда неразличимы под микроскопом, но, располагаясь между первичными кристаллами, сильно снижают ударную вязкость сплава и ухудшают его пластические свойства. Поэтому такие стали и сплавы плавят в печах с основной футеровкой.
В производстве литья по выплавляемым моделям сталь плавят без окисления, чаще всего методом переплава в электрических индукционных печах.
Для плавки без окисления тщательно рассчитывают шихту и составляют ее из свежего сплава и возврата или при необходимости снижения содержания углерода в стали — из 70—80 % возврата и 20—30 % низкоуглеродистой стали (0,1 —0,15 % С; % Р).
Шихту расплавляют при максимальном нагреве металла. К раскислению приступают после расплавления шихты и доводки стали по химическому составу. При раскислении происходит восстановление
рис. 7.1. Схема индукционной плавильной печи повышенной частоты с машинным преобразователем.
.
закиси железа, растворенной как в металле, так и в шлаке. Кроме того, раскислители, частично восстанавливающие легирующие элементы, находятся в шлаке в виде окислов. Восстановленные легирующие элементы вновь переходят в металл.
Устройство и работа индукционных печей повышенной частоты. Индукционные плавильные печи повышенной частоты (1000—2500 Гц) широко применяют в цехах литья по выплавляемым моделям. С такой частотой и работают современные установки с машинными и тиристорными преобразователями. На рис. 7.1 приведена схема печи с машинным преобразователем. К трубчатому индуктору, охлаждаемому протекающей внутри него водой, подводят переменный электрический ток, который, проходя по индуктору, создает переменный магнитный поток, пролизывающий футеровку печи и загруженные в тигель куски металлической шихты. Возникающие в металле вихревые токи нагревают шихту до расплавления.
Печи с машинным вращающимся преобразователем состоят из следующих основных узлов: печи 1 с индуктором, конденсаторных батарей 2, возбудителя 3 к преобразователю повышенной частоты 4 электродвигателя 8, вращающего преобразователь, электромонтаж* ной, измерительной, блокировочной и пусковой аппаратуры (на схеме не показаны).
Собственно печь представляет собой каркас с изолирующими про* кладками, внутри которого укреплен индуктор. Изолирующие прокладки необходимы для того, чтобы вокруг ийдуктора каркас печи не образовывал замкнутых контуров, что предотвращает утечку энергии в каркас. Тигель, расположенный внутри инДуктора, набивают футе-ровочной массой по конусному металлическому шаблону. Шаблоны делают из листового желаза (сварные). Небольшие шаблоны вынимают из печи после набивки. Шаблоны в печах большой вместимости расплавляются при первой плавке. Каркас печи укреплен на станине и вращается на дапфах, вокруг сливного носка печи. Поворот печи осуществляется электротельфером, гидроприводом или червячным поворотным механизмом с помощью штурвала.
Индуктор печи представляет собой медную трубку в виде катушки с расчетным (по мощности установки) числом витков. По индуктору пропускается переменный электрический ток повышенной.
частоты. Внутри индуктор охлаждается проточной холодной водой, что предохраняет его от перегрева и оплавления. Электрический ток и воду подводят к индуктору по гибким кабелям и шлангам, позволяющим осуществлять поворот печи. Со стороны футеровки индуктор защищают, дополнительно используя огнеупорную обмазку и изоляционные листы миканита и асбеста.
Конденсаторы монтируют в батарею. Они позволяют значительно сокращать потребную мощность преобразователя и регулировать работу печи на экономичных режимах (регулировать cos .
На схеме (см. рис. 7.1) приведен вращающийся преобразователь с горизонтальной осью. В последние годы получили распространение преобразователи с вертикальной осью, а также статические (тиристорные) преобразователи с высоким КПД, отсутствием изнашиваемых деталей и т. п. В табл. 7.2 приведены технические характеристики выпускаемых промышленностью индукционных плавильных печей для плавки стали.
Футеровка индукционных печей. Углеродистые стали выплавляют, как правило, в печах с кислой футеровкой. Исходными материалами для кислой футеровки служит кварцит или кварцевый песок и борная кислота.
Большую часть легированных, коррозионно-стойких, специальных сталей и сплавов выплавляют в печах с основной футеровкой. Ниже приведена, как пример, футеровка печи основными материалами. Кислая футеровка выполняется таким же способом. Исходными материалами для основной футеровки служат хромомагнезитовый кирпич (бой), магнезитовый кирпич (бой), заменяющий их металлургический магнезит {порошок), огнеупорная глина, жидкое стекло, борная кислота.
Магнезитовый и хромомагнезитовый кирпич или бой кирпича дробят на щековой камнедробилке, измельчают в бегунах или в шаровой мельнице до величины зерен
< 4 мм, затем просеивают через сито № 04. Полученный материал хранят в закрытых ларях; в сухом помещении и по мере надобности используют для приготовления футеровочной массы. Огнеупорную глину просушивают при температуре 150—200 °С, измельчают в бегунах и просеивают также через сито № 04. Молотую глину хранят в закрытых ларях.
Применяют футеровочную массу следующего состава; до 95 % магнезита или хромомагнезита; 2—6 % огнеупорной глины и 1,5—.
2 % борной кислоты или буры. Сначала тщательно перемешивают магнезит, затем добавляют борную кислоту, вновь тщательно перемешивают всю смесь в сухом виде и, добавляя воды (до влажности.
3—4 %), опять тщательно перемешивают всю массу. Мешалки могут быть лопастными или шнековыми.
Перед набивкой тигля обязательно проверяют исправность механизма подъема печи, системы водяного охлаждения, изоляции и крепления индуктора. Затем рчцщают и обдувают индуктор сжатым.
Таблица 7.2.
Технические характеристики индукционных плавильных печей для плавки стали
t> * | сх. ж | к . к S. о. с | сть. пере- | Расход воды на охлаждение, м 8 /ч | а. V | S. О. * | ||||
Тип печи (вместимость тигля по стали, кг) | Тип преобразователя частоты | Выходная мощн < преобр азовател я, | Частота тока кс иой депи, Гд | Номинальное нап ние питающей де | Производительно по переплаву и греву, т/.ч | индуктора | конденсаторной. батареи | преобразовате. ля | Масса электропе | Число печей в плексе |
ИСТ-0,06 | ВПЧ — 100—2,4 | 100 | 2400 | 380 | 0,13 | 1,2 | 0,6 | 2,5 | i,6 | 2 |
(60) | ТПЧ — 100—2,4 | 100 | 2400 | 380 | 0,13 | 1,2 | 0,6 | 2,0 | i,6 | 2 |
ТПЧ — 100—2,4 | 100 | 2400 | 380 | 0,24 | 1,8 | 1,0 | 2,0 | 1,6 | 2 | |
ИСТ-0,16 | ТПЧ — 160—2,4 | 160 | 2400 | 380 | 0,265 | 1,8 | 2,8 | 4,0 | 2,0 | 2 |
(160) | ОПЧ — 250—2,4 | 250 | 2400 | 380,. 600,. 3000. или. 6000 | 0,41 | 2,5 | 3,8 | 4,0 | 2,0 | 1 |
ТПЧ — 320—1 | 320 | 1000 | 380 | 0,50 | 3,1 | 5,5 | 4,0 | 2,0 | 1 | |
ИСТ-0,25 (250) 4 | ; ОПЧ — 250—2,4 | 250 | 2400 | 380,. 600,. 3000. или. 6000 | 0,38 | 2,25 | 3,3 | 4,0 | 2,4 | 1 |
ТПЧ — 320—1 | 320 | 1000 | 380 | 0,47 | 2,5 | 4,8 | 5,5 | 2,4 | 1 | |
ОПЧ — 500—1 | 500 | 1000 | 3000. или. 6000 | 0,81 | 3,7 | 7,5 | 4,0 | 3,0 | 1 | |
ИСТ-0,4 | ТПЧ — 320—1 | 320 | 1000 | 380 | 0,44 | 2,9 | 6,3 | 4,0 | 3,0 | ) 1 |
(400) | ОПЧ — 500—1 | 500 | 1000 | 3000. или. 6000 | 0,78 | 4,0 | 8,2 | 5,5 | 3,0 | 1 |
Примечания. 1, ОПЧ — однофазный преобразователь частоты. ВПЧ — вращающийся преобразователь частоты, ТПЧ — тиристорный (статический) преобразователь частоты.
2. Напряжение контурной цепи в печах всех типов 800 — 1000 В.
воздухом. Для изоляции индуктора можно применять специальную обмазку, состоящую из 80 % шамотного порошка, 20 % глиноземистого цемента и воды (сверх 100 %) до кашеобразного состояния. Слой обмазки продавливают сквозь витки индуктора и заглаживают с внутренней стороны, затем сушат. По внутреннему диаметру индуктор изолируют двумя слоями листового асбеста, который закрепляют пружинными разъемными кольцами. На подину печи укладывают два-три слоя листового асбеста общей толщиной 6—10 мм .(рис, 7.2),
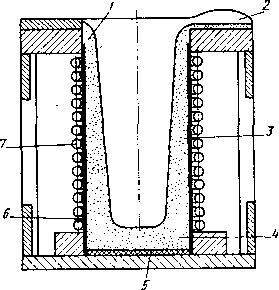
Рис. 7.2. Футеровка индукционной печн повышенной частоты:.
1 — верхнее кольцо (воротник); 2 — носок; 3 — стенка тигля; 4 — подииа; 5 — асбест; 6 — асбестовая ткаиь; 7 — индуктор.
.
На листовой асбест, уложенный на подину печи, засыпают футеровочную массу (слой толщиной 100—130 мм) и уплотняют ее трамбовкой равномерно и плотно до такой степени, чтобы трамбовка отскакивала. На этот слой устанавливают металлический шаблон. Поверхность утрамбованного слоя вокруг основания шаблона взрыхляют и засыпают футеровочную массу в кольцевое пространство между индуктором и шаблоном слоем высотой 20—40 мм. Каждый слой плотно утрамбовывают и затем для связи с последующим слоем взрыхляют поверхность. Стенки тигля набивают футеровочной массой до верхнего витка индуктора, предварительно вынимая поочередно разжимные кольца. После этого вынимают шаблон или расплавляют его при первой плавке. Иногда стенки тигля смачивают 50 %-ным раствором жидкого стекла в воде. Верхнее кольцо футеровки и носок тигля выполняют из той же футеровочной массы с добавкой 5—10 % жидкого стекла.
В тигель вставляют графитовый стержень, близкий по размеру тиглю, или металлические болванки, и включают печь на мощность 10—40 кВт. Таким образом, в течение 1,5—2 ч происходят сушка и спекание тигля. По окончании этого процесса печь выключают, вынимают графитовый стержень (болванки), продувают тигель сжатым воздухом и проверяют состояние футеровки. При отсутствии трещин в футеровке печь пригодна к плавке. Если в процессе работы печи на футеровке появятся незначительные трещины или размывы, то допускается подмазать их футеровочной массой с жидким стеклом, применяемой для набивки верхнего кольца (воротника).
Перед загрузкой шихты печь очищают от посторонних предметов, проверяют состояние футеровки печи (на отсутствие трещин, размывов и других дефектов) и состояние индуктора (исправность изоляции и водяного охлаждения).
Футеровку тиглей вакуумных печей осуществляют набивкой смесью плавленных магнезита и электрокорунда в соотношении 2:1.
Футеровочную смесь составляют из порошков трех фракций, в том числе 10 % размером зерна 4—2 мм, 20 % размером зерна 2—.
1 мм, остальные размером зерна .
Смесь готовят в лопастных мешалках или в смешивающих бегунах. Сначала смешивают тонкозернистую фракцию (размер зерна.
.
Стойкость футеровки вакуумных печей с массой плавки 10— 20 кг, наиболее часто применяемых в производстве отливок из жаропрочных сплавов, достигает 500—600 плавок. Однако в процессе эксплуатации наблюдаются мелкие растрескивания и разрушения футеровки, частицы которой попадают в жидкий металл и приводят к браку отливок по засорам. Для снижения брака по засорам вместо набивных тиглей целесообразно применять готовые спеченные огнеупорные тигли с ежесуточной их заменой.
Плавка стали в индукционных печах. Плавка в индукционной печи идет быстро, поэтому нет возможности ждать полного экспресс-анализа и по полученным данным корректировать химический состав расплава. Плавку приходится вести, основываясь на расчете шихты. Шлаки имеют низкую температуру и недостаточно активны. По этой причине плавку ведут без окисления, методом переплава, используя чистый металлический скрап, чистый литейный возврат и ферросплавы. Процессы дефосфорации, десульфурации и диффузионного раскисления в таком случае затруднены, поэтому шихтовые материалы необходимо подбирать с малым содержанием серы и фосфора.
Размеры шихтовых материалов подбирают из условий наиболее полного заполнения тигля. Тугоплавкие ферросплавы зафужают в более горячую часть печи — в нижнюю часть тигля. Для"более плотной укл,адки промежутки между крупными кусками шкхты засыпают мелкими. Плотная укладка шихты способствует ускорению ее расплавления и снижению расхода электроэнергии. В этих же целях печь накрывают крышкой-сводом. Шихтовые материалы не следует загружать выше витков индуктора, так как в этом случае, не пересекаясь силовыми линиями магнитного поля, шихта плавится только за счет теплопередачи; кроме того, высоко загруженная шихта препятствует плотному закрытию печи сводом.
Куски шихты по мере оплавления и опускания вниз могут свариваться между собой, образуя «мост», под который расплав перегревается, что может привести к разрушению футеровки. Заклинйв-шиеся куски шихты следует освобождать, поднимая их клещами вверх, осаживая в то же время освобожденные куски шихты вниз, в расплав. Нельзя загружать холодную шихту, а тем более влажную в расплавленный металл, так как это сопровождается выплеском последнего из печи. Выплески, попадая на куски твердой шихты, также способствуют образованию «мостов».
По мере плавЛенйй й оседания Шихты в печь добавляют подогре тые куски шихты, не поместившиеся при завалке.
Соблюдают следующий порядок введения в сплав легирующих элементов. Никель в процессе плавки не окисляется, поэтому era вводят непосредственно в шихту при загрузке печи. Раняя загрузка* никеля способствует выделению из металла водорода, газов, содер- жащихся в электролитическом никеле, и воды — в гранулированном никеле. Ферромолибден также дают в завалку.
Вольфрам — тугоплавкий элемент с температурой плавления. ~3400 °С. Для его растворения в расплаве требуется длительное время, сократить которое можно предварительным подогревом вольфрама или ферровольфрама до 900—950 °С. Вольфрам — тяжелый; металл. Для его растворения необходимо перемешивать нижние слои ванны.
Металлический хром вводят в состав шихты при выплавке сталей с особыми свойствами (жаропрочные, жаростойкие) главным образом в случаях, когда требуется низкое содержание углерода. При выплавке других легированных сталей обычно используют феррохром разных марок. Феррохром вводят в завалку или после расплавления основы сплава. После присадки феррохрома шлак приобретает зеленый цвет благодаря окислам хрома. Раскислители восстанавливают хром из окислов, и шлак после раскисления приобретает светлую окраску.
При выплавке высокохромистых сталей феррохром предварительно подогревают в нагревательной печи, что сокращает продолжительность плавки. Феррохром имеет меньшую объемную массу, чем сталь, поэтому куски его всплывают на поверхность металла. Их периодически осаживают в глубину ванны.
Ванадий легко окисляется, поэтому его вводят в ванну за 5— 10 мин до выпуска стали в хорошо раскисленный металл.
Титан окисляется еще более интенсивно, чем ванадий. Его вводят в ванну перед выпуском стали из печи (за 2—3 мин). Так как титан значительно легче стали, то его для лучшего усвоения следует погружать в расплав с помощью специального «колокольчика» или шомпола. Если ферротитан предварительно подогреть и непрерывно погружать при расплавлении в стальную ванну с малым количеством Шлака, то можно растворить в стали до 70 % вводимого титана. Если этих мер не принять, усвоение титана составит всего 50—40 %, а иногда и менее.
После расплавления всей шихты наводят шлак. В индукционных печах благодаря выпуклому мениску расплава, пронизываемого магнитными силовыми линиями, шлак стекает к стенкам тигля; его время от времени добавляют, не допуская появления незащищенной Шлаком поверхности металла. Шлаковый покров в индукционных печах защищает сплав от насыщения газами, снижает угар элементов и уменьшает тепловые потери. При выплавке стали в печах с кислой футеровкой чаще всего в качестве шлаковой смеси используют бой стекла.
При основной футеровке шлак состоит из 60—80 % свежеобож-женной извести, 15—20 % магнезитового порошка и 5—20 % плавикового шпата. Для высокожаропрочных никелевых сплавов применяют также шлак следующего состава: 50 % СаО, 25 % А1
0
; 18 % MgO и 7 % CaF
Во время доводки стали в последний период плавки в состав шлака добавляют молотый кокс или электродный бой, ферросилиций или комплексные раскислители—силикокальций, боркальк. От состава шлака зависит стойкость тигля. Высокоосновной шлак проникает в стенки футеровки и реагирует со связующим, вымывая стенки тигля. Кроме того, если шлак имеет такой состав, что при охлаждении он рассыпается на воздухе, ошлакованные стенки тигля при охлаждении печи также могут осыпаться. Поэтому часто доводку сплава ведут со шлаком меньшей основности, например: 50 % SiO„.
25 % СаО, 25 % А1
0
Общее количество шлака при плавке в индукционных печах составляет ~3 % массы металлической шихты. Плавку следует вести на максимальной мощности генератора и настраивать электрический режим на резонанс (cos .
При выплавке стали в печах вместимостью 150—250 кг после полного расплавления металла берут пробу для экспресс-анализа на углерод и марганец в основной печи и на углерод и кремний в кислой печи. В ожидании анализа снимают шлак, образовавшийся при плавлении, и наводят новый шлак того же состава.
При плавке в печах вместимостью 10—50 кг экспресс-анализ обычно не делают вследствие быстрого протекания процесса плавки. В этом случае состав шихты не корректируют, а ведут плавку точно по расчету, строго выдерживая время и электрическщцэежим плавки. В печах малой емкости ввиду трудности наведения шлака при очень выпуклом мениске расплава покровным шлаком обычно не пользуются. Плавку ведут без шлака.
После получения анализа, если сплав надо науглеродить, снимают шлак и на зеркало расплава засыпают мелко дробленый электродный бой или древесный уголь, после чего наводят новый шлак. В этом случае коэффициент усвоения углерода составляет 70—80 %. Науглероживание стали лучше вести, применяя углеродистый феррохром или чугун, а не древесный уголь или электродный бой, так как в последнем случае время плавки увеличивается.
Марганец вводят в расплав, исходя из среднего содержания его (по заданному химическому составу сплава). При хорошо отлаженной технологии плавки для экономичной работы легирующие элементы вводят в расплав с учетом усвоения на нижнем пределе химического состава.
Во всех случаях доводку стали по составу следует проводить в печи, а не в ковше, как это иногда пытаются делать.
- Перед взятием пробы на химический анализ следует тщательно перемешивать ванну на всю глубину,.
В качестве раскислителей применяют углерод, кремний, марганец, титан (или их ферросплавы), алюминий, карбид кальция, а также комплексные раскислители: силикокальций, силикомарга-нец, алюмобарийкальций и др. При диффузионном раскислении раскислители вводят в шлак в молотом виде или в порошке (алюминий).
Раскисление углеродом идет по реакции
Побочным веществом при раскислении углеродом является газ, а эго значит, что металл не загрязняется неметаллическими соединениями. Раскисление углеродом связано и с некоторыми недостатками: возможно науглероживание сплава, диффузионный процесс раскисления углеродом длителен.
Раскисление кремнием, марганцем и алюминием идет по реакциям
Кремний — сильный раскислитель, но с повышением температуры его раскисляющая способность снижается.
Марганец значительно слабее раскисляет сталь, чем кремний. Одним марганцем полностью раскислить сталь нельзя. Закись марганца нерастворима в стали и переходит в шлак. С серой марганец образует более тугоплавкое соединение, чем железо. Сернистый марганец полностью переходит в шлак и металл освобождается от сернистых соединений.
Для окончательного раскисления используют силикокальций (до 0,1 %), который изменяет характер включений встали (строчечные включения он превращает в глобулярные).
Раскисление металла для больших плавок (>100 кг) можно проводить диффузионным методом, вводя в шлак молотый кокс, ферросилиций или комплексные раскислители (силикокальций, бор-кальк). Шлак при этом быстро получает светную окраску. Раскислению способствует интенсивное движение металла при индукционной плавке, но используя хорошую циркуляцию металла, можно раскислять сталь и кусковыми раскислителями, что чаще делают при работе на печах малой емкости. Циркулирующие потоки металла выносят продукты раскисления на поверхность, где окислы переходят е шлак.
При диффузионном раскислении применяют различные шлаки в зависимости от химического состава стали и устройства печи. Конструкционные углеродистые стали с содержанием менее 0,3 % С.
раскисляют под белым шлаком, среднеуглеродистые и высокоуглеродистые под карбидным шлаком, коррозионно-стойкие — под магнезиально-глиноземистым шлаком.
Перед наведением белого шлака скачивают окислительный шлак, в ванну присаживают ферромарганец из расчета на верхний предел содержания в сплаве, затем наводят высокоосновной шлак, состоящий из 80 % извести и 20 % плавикового шпата. Количество шлака зависит от вместимости печей и составляет 2—3 % массы завалки для печей большой вместимости и 3—7 % — малой.
Для раскисления в шлаковую смесь вводят молотый кокс или древесный уголь, обладающий меньшей массой и меньше науглероживающий сталь.
Углерод в шлаке раскисляет закись железа и марганца по реакциям
Перед раскислением шлак темного цвета (присутствуют окислы железа и марганца), в процессе раскисления он светлеет. Для окончательного раскисления вводят дробленый 75 %-ный ферросилиций так, чтобы его частицы оставались взвешенными в шлаке и не переходили в металл. Количество ферросилиция должно быть равно количеству вводимого в шлак углерода. После окончательного раскисления шлак становится белым пенящимся. Хороший шлак при остывании рассыпается на воздухе в порошок.
Раскисление металла в печах малой вместимости (до 50 кг) ведут твердым раскислителем (предпочтительно силикокальцием из рас* чета 0,2—0,3 % массы шихты). В этом случае шлак не наводят. В процессе раскисления тигель закрывают железным листом из-за большого пироэффекта.
Повышение качества сталей и сплавов в процессе их плавки и заливки. Большую часть сталей длялитья по выплавляемым моделям в металлургической промышленности выплавляют в печах с кварцевой (кислой) футеровкой. Содержание серы и фосфора в этих сталях более высокое, чем в сталях, выплавленных в печах с основной футеровкой. Эти стали загрязнены также неметаллическими включениями (сульфиды, фосфиды и др.), снижающими их механические свойства, особенно пластичность. Для обеспечения высокой ударной вязкости высококачественных отливок содержание серы и фосфора в них должно быть не более 0,01 %. Между тем в выпускаемых металлургической промышленностью сталях, используемых в качестве шихтовых материалор при литье по выплавляемым моделям, содержание серы и фосфора допускается до 0,025 и даже 0,05 %. Для подавления влияния вредных примесей, при плавке следует применять модификаторы, которые видоизменяют особенно неблагоприятную остроугольную форму фосфидов, оксидов и сульфидов, очищают границы зерен и упрочняют сталь.
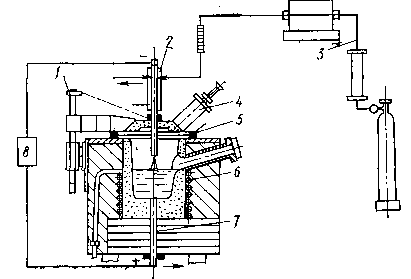
Рис. 7.3. Схема плазменно-индукционной плавильной установки:.
I — механизм перемещения плазмотрона; 2 — плазмотрон; 3 — пода« ча аргона; 4 — герметизированный люк; 5 — крышка (свод); 6 — индуктор печи; 7 — водоохлаждаемый анод; 8 — источник питания.
.
Хорошим модификатором является силикокальций в сочетании с РМЗ, при введении которых в 2 раза повышается ударная вязкость стали [111, 1121.
Значительное повышение качества сталей и сплавов достигают также применением плазменно-индукционной плавки при которой благодаря дополнительному нагреву верхней части ванны сокращается время плавки. Одновременно повышается чистота металла, производительность печей и снижается удельный расход электроэнергии [91.
В ИПЛ АН УССР разработана и испытана на ряде заводов плазменно-индукционная установка [9], изготовленная на базе печи ИСТ-0,16, к которой сделана плазменная приставка, представляющая собой водоохлаждаемую футерованную крышку (свод), установленную в верхней части печи на уплотнительном кольце (рис. 7.3). На крышке смонтирован плазматрон с механизмом его перемещения. Для загрузки шихты в процессе плавки, ввода легирующих добавок и наблюдения за ходом плавки в крышке предусмотрен герметизированный люк со стеклом. В дно тигля вмонтирован водоохлаждаемый анод. К плазматрону подведены системы охлаждения и газоочистки. Питание плазматрона осуществляется от управляемого источника постоянного тока типа ВПР-602. В качестве плазмообразующего газа используют технически чистый аргон (ГОСТ 10157—79), предварительно очищенный от влаги, кислорода и азота.
Известно, что свойства отливок в большой степени зависят от ориентации и величины зерей в литой структуре. Качество отливок можно повысить, осуществляя регулирование структуры металла в процессе заливки формы и ее охлаждения, так называемую, контролируемую кристаллизацию [90, 18]. Для этих целей в плавильнозаливочных вакуумных установках, дополнительно к плавильным печам помещают индукционные нагревательные печи для форм. Прокаленные формы устанавливают в печь нагрева формы и, в процессе плавки металла и заливки его форма не остывает, а нагревается до заданной температуры и даже до температуры заливаемого расплава. Контролируемую (направленную) кристаллизацию отливок можно вести по нескольким вариантам технологического процесса, рассмотренным ниже.
1.
Применяют тонкостенную прочную оболочку форму без опорного наполнителя, которую нагревают до 1000—1050 °С, заливают расплавом при температуре 1480—1500 °С и выдерживают в нагревательной печи до 800—850 °С. При достижении этой температуры отливку переносят в термостат с температурой 600—650 °С, где выдерживают до 300 °С с последующим охлаждением на воздухе. При таком режиме получают поликристаллическую структуру отливки с минимальными остаточными напряжениями, но со сравнительно крупной макроструктурой.
2.
При изготовлении оболочковой формы в поверхностный слой формы вносят мелкодисперсные окислы, являющиеся модификаторами — центрами кристаллизации, и затем эту форму нагревают, заливают расплавом и охлаждают по варианту 1. В этом случае получают более мелкую макроструктуру в поверхностном слое отливки. Ее можно регулировать количеством; модификатора и его дисперсностью.
3.
Оболочковую форму нагревают до температуры заливки расплава. После заливки нижнюю часть формы (отливки) искусственно охлаждаюр-и постепенно с заданной скоростью форму с отливкой выводят вниз из зоны нагревательной печи. Происходит направленная снизу вверх кристаллизация отливки, которая приобретает поликристаллическую или монокристаллическую структуру, ориентированную вертикально по всей высоте. При этом резко возрастают пластические свойства металла, надежность и длительность эксплуатации отливок.
В табл. 7.3 приведены свойства сплава ММ 200, отлитого по различным вариантам технологии.
Таблица 7.3.
Свойства различных модификаций сплава ММ 200 _ _.
Сплав | ММ 200 | |||
Свойства | обычный | ММ 246 (модификация) | направленной кристал-лиаацин | в вида монокристалла |
при г и = 760 °с. сг в . МПа | 949 | 1055 | 1055 | 1055 |
6, % | 3 | 4 | 6 | 12 |
Жаропрочность т, ч (при 700 МПа) | . 5 | 30 | . 380 | 250 |
Ползучесть о^о/юо ( П Р И ^00 МПа) | — | 30 | 3 | 5 ■ |
При t B = 982 °С Жаропрочность х, ч (при 210 МПа) | 40 | 36 | 105 | 105 |
Ползучесть о^о/юо ( П Р И 210 МПа) | 30 | 10 | 45 | 45 : |
Термическая усталость | Хорошая | Очень | Отлич | |
Стоимость | Обычная | хорошая. Высокая | им. Очень | |
высокая |
Рис. 7.4. Макроструктура отливок с регулируемой кристаллизацией;.
.
/ — поликристаллнческая структура; II — направленная (про-дольио-ориеитнрованная) структура; III — монокрнсталлическая структура.
По пластичности и термической усталости сплавы с направленной кристаллизацией по сравнению с поликристаллическими сплавами имеют очень большие преимущества, что объясняется отсутствием поперечных границ зерен. Но медленная кристаллизация способствует образованию рыхлот в отливках. Нет преимуществ в ползучести. Получение отливок с контролируемой кристаллизацией трудоемко и сложно, поэтому отливки пока очень дороги.
4. Оболочковую форму устанавливают в графитовую опоку с д ом и засыпают графитовой крошкой. Опоку помещают в печь и нагревают до температуры заливки металла. После заливки форму выдерживают в печи до полного заполнения расплавом междендритных пустот. Затем форму с заданной скоростью опускают из нагревательной печи и она остывает на воздухе, либо в термостате по заданному режиму. В результате получают тонкостенную плотную фасонную отливку с однонаправленным затвердеванием металла во всех стенках. При этом наблюдается некоторое повышение прочности и резкое повышение пластичности.
На рис. 7.4 приведена макроструктура отливок с регулируемой кристаллизацией.
Плавка специальных сплавов в иидукциоииых вакуумных печах. Наиболее высокими жаропрочными свойствами, необходимыми для производства литых турбинных лопаток, обладают литые сплавы на никелевой основе типа ЖС. Основным методом получения лопаток из этих сплавов является литье по выплавляемым моделям. Однако указанные сплавы из-за большого содержания алюминия и титана легко окисляются и образуют в процессе плавки и разливки плотные окисные плены, которые, попадая в отливки, нарушают сплошность
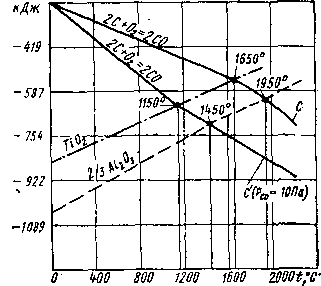
Рис. 7.5. Свободные энергии образования окислов металлов для реакций, выраженных на 1 г• моль кислорода.
.
материала и снижают прочность лопаток. Величина окисных плен и их расположение в отливках самые разнообразные. Наличие окисных плен на поверхности пера лопаток, а также на их кромках, как правило, является признаком брака.
Окисные плены образуются при температуре до 1700 °С как во время приготовления исходного сплава иразливки его в изложницы, так и во время приготовления рабочего сплава и разливки его в формы при отливке лопаток. Избежать образования окисных плен можно обработкой жидкого расплава раскислителями, плавкой и разливкой в вакууме или в нейтральной среде.
Плавка жаропрочных литейных сплавов, содержащих алюминий и титан, в вакуумных индукционных печах повышенной частоты находит все большее применение. По своему сродству к кислороду алюминий уступает лишь магнию и кальцию. Вакуум благоприятствует любой химической реакции, в ходе которой из нелетучих веществ образуются газы или летучие вещества, в результате чего понижается температура и становится возможным протекание данной реакции.
На рис. 7.5 приведены изменения свободных энергий образования окислов титана и алюминия в зависимости от температуры.
В атмосферных условиях углерод может начать раскисление окислов титана при температуре 1650 °С, а окислов алюминия при 1950 °С. С понижением давления раскислительная способность углерода повышается и при разрежении 10 Па температура начала раскисления снижается примерно на 500 °С, т. е. окислы титана раскисляются углеродом при температуре 1150 °С, а окислы алюминия при 1450 °С. Опыт плавки жаропрочных сплавов в вакуумных печах при разрежении 1—4 Па подтверждает раскисляемость окислов алюминия (плены) при температуре 1550—1650 °С по реакции
при этом окись углерода улетучивается. Технические характеристики вакуумных индукционных печей приведены в табл. 7.4.
При использовании печей периодического действия (см. табл. 7.4) после каждой плавки и заливки вакуумная камера сообщается с атмосферой и откатывается. Залитую форму снимают с печи, очищают тигель, вновь загружают шихту, устанавливают новую форму, камеру накатывают и начинают вакуумирование тигля, шихты и формы.
Технические характеристики индукционных вакуумных печей для плавки н заливки форм
Тип | печи | |
Параметр | ИСВ-0,04 ПФ-И2 * | ИСВ-0,16 НФ-И1 * |
Номинальная емкость тигля (по стали), т | 0,04 | 0,16 |
Установленная мощность, кВ-А | 250 | 525 |
Мощность питающего преобразователя, кВт Частота, Гц: | 120 | 250 |
контура | 2400 | 2400 |
питающей сети Напряжение, В: | 50 | 50 |
контура | 500 | 300 |
питающей сети | 380 | 380 |
цепей управления | 220 | 220 |
силовых цепей | 220/380 | 220/380 |
Максимальная температура расплава в тнгле, °С Среда в рабочем пространстве (плавильная камера) | 1650 | 1700 |
Вакуум или нейтральный газ | ||
Предельное разрежение в холодной печи, Па | 5-0,133 | 5-0,133 |
Максимально допустимое избыточное давление нейтрального газа, кПа. Производительность по расплавлению и перегреву, т/ч | 10 | 10 |
0,12 | 0,21 | |
Удельный расход электроэнергии на расплавление и перегрев, кВт-ч/т Габаритные размеры форм, м: | 1100 | 2000 |
ширина X длина | 0,5X0,6 | 0,7X1,6 |
высота | 1,0 | 1,0 |
Масса электропечи, т | 10 | 30 |
Вместимость (по стали) сменных индукторов, которыми дополнительно комплектуются печи, т | 0,01 и 0,025 | 0,06 и 0,1 |
* П — периодического действия; Н — непрерывного действия.
.
Таким образом, вакуумная система работает нерационально на восстановление утерянного вакуума. Кроме того, происходит потеря теплоты и резкое изменение температуры тигля, снижающее стойкость футеровки, а также окисление остатков расплава на стенках тигля. Образуются так называемые настыли, что загрязняет жидкий металл последующих плавок и снижает качество отливок.
Для устранения отмеченных недостатков выпускают вакуумные установки полупрерывного действия на различную вместимость тиглей (см. табл. 7.4). В этих установках кроме индукционной печи для плавки металла имеется печь сопротивления для подогрева формы до 900 °С.
Особенности плавки сплавов для постоянных магнитов. Содержание примесей, особенно углерода, в шихтовых материалах должно быть минимальным. В магнитных сплавах должно быть не более0,03 % С;Ч),35 % Мп, 0,15 % Si, 0,025 % S и 0,025 % Р. В сплаве ЮНДК18 содержание 0,1 % С снижает остаточную индукцию на.
20 %, коэрцитивную силу на 40 % и максимальную магнитную энергию на 50 %.
•.
Для получения высококачественных магнитов необходимо применять следующие шихтовые материалы: низкоуглеродистую электротехническую сталь (железо армко) марок ЭА и Э в виде прутков или листов; никель марок Н-0 и Н-1 в виде катодных листов или слитков по ГОСТ 849—70; кобальт марок КО и К.1А в чушках шг ГОСТ 123—78; алюминий первичный марок А95, А7, А6, А5 в чушках по ГОСТ 11069—74; медь марок МО и Ml в виде катодных листов по ГОСТ 546—79; возврат и отходы магнитного сплава (литники, брак магнитов по внешним дефектам и др.).
Количество отходов, вводимых в плавку, должно быть не более 40 % массы шихты.
Исходные шихтовые материалы подлежат разделке только в холодном состоянии. Газовая резка шихтовых материалов не допускается. Возврат и отходы, поступающие на плавку, должны быть очищены от формовочных материалов, а также от окислов, масляных, пятен и других загрязнений. Кроме основных шихтовых материалов в сплав часто добавляют сернистое железо с целью измельчения структуры и упрочнения сплава. При плавке сплава ЮНДК18 сернистого железа обычно добавляют 0,3 % массы шихты.
Магнитные сплавы выплавляют в высокочастотных индукционных печах с кислой или основной футеровкой. Для получения магнитов со стабильными свойствами плавку следует вести форсированно; скорость расплавления всей шихты данной плавки 0,7—1,2 кг/мин. Чтобы сократить продолжительность плавки, шихтовые материалы подбирают оптимальных размеров в зависимости от емкости плавильного тигля (табл. 7.5).
.
Таблица 7.5.
Размеры шихтовых материалов в зависимости от вместимости тигля
Вместимость плавильного тигля, кг | Размеры прутков железа, мм | Масса. чушек. кобальта,. кг | Размер заготовки, мм | Масса. чушкн. алюминия,. кг | ||
диаметр | длина | иикеля | меди | |||
10—20. 20—30. 30—50 | 15—20. 20—35. 20—50 | 110—130. 150—200. 200—230 | 0,9-1,5. 1.5-2,5. 2.5-4,0 | ЗОХ100 60Х160 80X 250 | ЗОХ 100 60X150 80X250 | 0,8-1,1 1,1-2,4 2,5-4,0 |
Рекомендуется также подогревать до температуры 300—400 °С никель, медь и алюминий перед загрузкой в плавильный тигель. Загрузку и плавку шихтовых материалов необходимо вести в определенной последовательности: при плавке в кислом тигле загружают битое стекло (2 % массы шихты), затем железо, кобальт. Включают ток и ведут плавку на максимально возможной мощности печи. После расшгавления большей части железа и кобальта в тигель загружают никель, медь и сернистое железо, а потом возврат (литники и другие отходы). Во время расплавления шихты ванна должна быть все время покрыта шлаком, . ...
Основные характеристики поворотных тигельных печей сопротивления CAT
Тип печи | Вместимость тигля, кг | Мощность трансформатора, кВт | Масса металлической конструкция печн, кг | Габаритные размеры (длниа, ширина, высота), м |
САТ-0Д5А | 150 | 40 | 960 | 1,75X1,34X2,30 |
САТ-0.25А | 250 | 60 | 1170 | 1,87X1,44X 2,38 |
САТ-0,50А | 500 | 80 | 1570 | 2,0X1,59X2,62 |
После расплавления всей загруженной шихты и некоторого перегрева расплава снимают шлак и быстро загружают крупные куски алюминия. Затем ванну тщательно перемешивают (штангой из электротехнической стали) и, выдержав 2—3 мин, снимают вновь образовавшийся шлак и готовый расплав сливают в ковш, предварительно подогретый до 700—850 °С. Перед выпуском расплава температура его должна быть 1550—1600 °С. Температуру измеряют.
термопарой погружения. Сильный перегрев расплава приводит к получению хрупких магнитов, выкрашивающихся при шлифовании. Плавка алюминиевых сплавов. В производстве литья по выплавляемым моделям из алюминиевых сплавов обычно применяют плавильные печи вместимостью 0,15— 0,50 т, к ним относятся и электропечи сопротивления типа CAT (тигельные) (табл. 7.6, рис. 7.6). Для плавки алюминиевых сплавов применяют также более экономичные индукционные печи промышленной частоты с железным сердечником, которые работают по принципу своеобразного короткозамкнутого трансформатора: первичная обмотка — мно-говитковая катушка (индуктор), а вторичная — расплавленный металл в каналах. Работу на этих печах следует вести непрерывно. В перерывах между плавками в печи должен обязательно оставаться расплав («болото») в таком количестве, чтобы плавильные каналы замыкались. В это время печь работает на мощности холостого хода, которая в 5—6 раз меньше номинальной мощности.
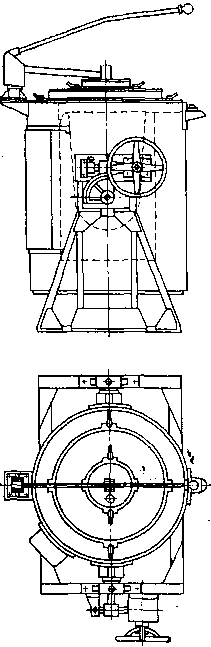
Рис. 7.6. Поворотная тигельная печь типа CAT.
.
.
.
Для алюминиевых СПЛаВОй Минимальной, по полезной вместимости является индукционная канальная печь ИА-0,5 (рис. 7.7).
Печи ИА-05, снабжены гидравлическим механизмом с плунжерами для поворота. Расплав сливают при наклоне печи через слив* ной носок.
Индукционные электропечи ИА-0,5 применяют для непрерывной работы. Пусковой период включая время на футеровку печи длится.
1 —1,5 мес, поэтому в эксплуатации должно быть не менее двух печей. Стойкость футеровки канальной части печей ИА-0,5 выполненной из шамотно-кварцитовой массы, 2000—3000 плавок. В процессе работы каналы печи зарастают окисью алюминия, их приходится система-тичзски прочищать 1—2 раза в смену специальным инструментом (трубы, ерши и г. д.). Полная вместимость каналов 0,3 т и рабочей ванны 0,5 т. Номинальная мощность печи 125 кВт, мощность трансформатора 180 кВт. Удельный расход электроэнергии 450— 445 кВт-ч/т. Продолжительность плавки 2 ч. Мощность холостого хода 22 кВА. Выдача расплава может производиться в заданном темпе до 250 кг/ч.
Целесообразно применять индукционные тигельные печи (ИПА-250 и И ПА-500) промышленной частоты вместимостью 250 и 500 кг, которые хорошо себя зарекомендовали в эксплуатации (табл. 7.7).
Таблица 7.7.
Технические характеристики индукционных тигельных печей ИПА-250 н И ПА-500 для плавки алюминиевых сплавов и печи ИПМ-350 для плавки магниевых сплавов
Параметр | ИПА-250 | ИПА-500 | ИПМ-350 |
Средняя мощность печн, кВт | 70 | 120 | 100 |
Мощность конденсаторных батарей, кВ-А | 190 | 320 | 420 |
Средняя снла тока сетн, А | 270 | 400 | 260 |
Емкость тнгля, кг | 250 | 500 | 350 |
Время плавки в горячем тигле, мнн Производительность печн, кг/ч | 110 | 110 | 100 |
136 | 273 | 210 | |
КПД, % | 70 | 75 | 83 |
Удельный расход электроэнергии, кВт-ч/т Габаритные размеры печн (длина, ши | 450 | 400 | 450 |
1,5X2,0Х | 1,5X2,0Х | 1,25Х 1,25Х | |
рина, высота), м | Х1,6 | Х2,0 | XI,5 |
Примечание. Частота питающего тока 50 Гц; напряжение на индукторе печя питающей сети и конденсаторной батареи 380 В.
На рис. 7.8 показана тигельная индукционная печь промышленной частоты. Печь состоит из толстостенного тигля с крышкой, индуктора, теплоизоляции и магнитопровода. Тигель установлен в каркас печи, который поворачивается гидравлическим подъемником. Нагрев и плавка шихты происходят за счет теплоты, индуктированной в материале шихты, и теплоизлучения тигля, нагреваемого индуктивными токами. Благодаря этому, удельный расход электро-
РИС. 7.7. Печь ИА-0,5:.
а — общий вид; б — футеровка.
Рис. 7.8. Индукционная тигельная электропечь промышленной частоты для плавки легких сплавов:.
1 — тигель; 2 — тепловая изоляция; 3 — индуктор; 4 — гидравлический подъемник; 5 — узел присоединения печи; 6 — щит управления; 7 — помещение для конденсаторов
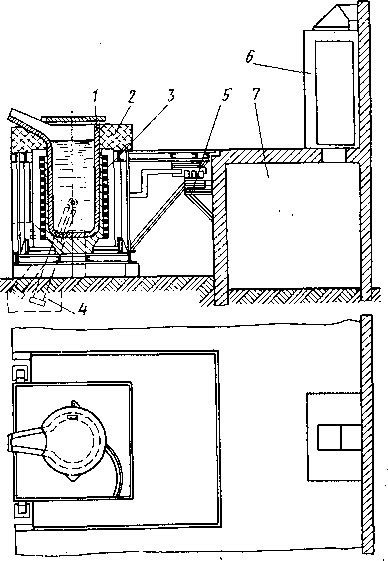
энергии значительно со-кращается. КПД таких печей очень высок и достигает 0,85.
При плавке алюминиевых сплавов применяют чугунные тигли. В печах типа ИПА можно также плавить медные сплавы, но в графитовых тиглях.
Использование чугунных тиглей при плавке приводит к насыщению алюминиевых сплавов железом вследствие растворения стенок тигля. Во избежание этого чугунные тигли в подогревом до 150 °С состоянии покрывают защитными красками, которые снижают степень насыщения железом алюминиевых сплавов. Чтобы полностью исключить насыщение алюминиевых сплавов железом и снизить эксплуатационные расходы, связанные с заменой чугунных тиглей, на ряде промышленных предприятий для индукционных печей типа ИПА внедрены тигли из жаростойкого бетона.
Бетон состоит из шамотно-магнезитовой крошки, скрепленной жидким стеклом и кремнефтористым натрием. Твердение этого бес-цементного бетона происходит в результате физико-химических процессов, протекающих при взаимодействии составляющих смеси. При этом образуются форстерит и кордиерит, связывающие все компоненты в однородную прочную массу.
Приготовление алюминиевых сплавов заключается в сплавлении алюминия с другими металлами. В разогретую печь загружают шихтовые материалы по расчету, в следующем порядке: возврат сплава (литники, бракованные детали и сплески), исходные металлы (алюминий, силумин, магний) и лигатуры (промежуточный сплав). Сильно угорающие элементы (магний, цинк) вводят в сплав в последнюю очередь. Такой порядок загрузки позволяет вести плавку форсированно, не перегревая сплав; тем самым снижается угар компонентов и повышается качество сплава.
Алюминиевые сплавы легко окисляют. В процессе плавки на поверхности расплава образуется прочная окисная пленка, защищающая сплав от дальнейшего окисления. Во время плавки перемешивать расплав не следует, чтобы не разрушать окисной пленки. Добавки вводят осторожно, сдвинув пленку с части поверхности металла. Алюминиевые сплавы интенсивно поглощают и растворяют газы, особенно водород, что приводит к газовой пористости в отливках. Поэтому все шихтовые материалы хранят в сухом помещении и вводят в печь в сухом виде и даже слегка подогретыми. Индукционные печи с железным сердечником футеруют смесями, в которые входят молотый фарфор или шамот (50—55 %), глина огнеупорная (30—40 %) и барит в порошке или плавиковый штап (9—12 %).
Для уменьшения зарастания окисью алюминия каналы выполняют из графитовых электродов или путем обклейки шаблона при футеровке специальными графитовыми пластинами. Для предупреждения образования пористости и исключения неметаллических включений алюминиевые сплавы подвергают дегазации и рафинированию в жидком состоянии. Для этих целей применяют продувку расплава хлором, обрабатывают гексахлорэтаном или хлористыми солями (хлористый цинк, хлористый марганец и хлористый алюминий). Предварительно соли обезвоживают переплавкой и до использования хранят в электрошкафу при температуре 120—150 °С.
Для повышения механических свойств, особенно пластичности, алюминиевые сплавы, содержащие *>5 % Si с грубой структурой подвергают модифицированию (искусственное измельчение структуры).
При литье по выплавляемым моделям, когда процесс кристаллизации замедлен из-за повышенной температуры формы (100—300 °С), получаются отливки с крупнокристаллической структурой и относительно низкими механическими свойствами. В таких случаях рекомендуется модифицирование расплава введением в него небольшого количества натрия. Для этого используют хлористые и фтористые соли натрия. Сначала расплав рафинируют, а затем модифицируют. Опыт показал, что во время модифицирования двойным (34 % NaCl + 66 % NaF) или тройным (62,5 % NaCl + 25 % NaF -f-+ 12,5 % КСЛ) модификатором расплав вновь насыщается газами и неметаллическими включениями. Во избежание этого, а также для ускорения и удешевления процесса плавки применяют так называемый универсальный флюс, который одновременно рафинирует и модифицирует расплав. Универсальный флюс растворяет, переводит в прозрачный расплав 1,2—1,6 % (по массе) А1
0
, адсорбирует б—12 % А1
0
и дегазирует расплав активнее хлористого цинка. Так как заливку разных отливок производят при различных температурах, применяют три состава универсального флюса, приведенные в табл. 7.8.
Рафинируют и модифицируют расплавы универсальным порошковым флюсом следующим образом. Соли, входящие в состав флюса, предварительно сушат при 200—250 "С в течение 3 ч. Высушенные соли смешивают в бегунах или в шаровой мельнице до получения
}. Номер. флюса | Содержание, % | Температура, °С | ||||
фтори. стый. натрий | хлористый. натрий | хлористый. калий | криолит | плавле. ния | минимальная. модифициро. вания | |
1 | 60 | 25 | 15 | 850 | 750 | |
2 | 40 | 45 | — | 15 | 780 | 730 |
3 | 30 | 50 | 10 | 10 | 730 | 710 |
однородной смеси. Готовый флюс, предварительно нагретый до 250— 300 °С, вводят в количестве 0,75—1,0 % на струю расплава, подаваемого в разливочный ковш (при заполнении его). По истечении 2—4 мин после заполнения ковша расплав тщательно очищают и затем заливают в формы. Еще более эффективно действие универсального флюса в жидком состоянии. Для расплавления флюса применяют трехфазную дуговую печь с центральным нагревом солей (рис. 7.9).
Рафинируют и модифицируют расплав жидким универсальным флюсом следующим образом. В нагретый разливочный тигель на небольшой слой расплава мерной ложкой заливают жидкий флюс в количестве 0,3—0,5 % массы расплава и заполняют тигель расплавом. При этом флюс всплывает. Проходя через весь расплав флюс взаимодействует с ним, дегазируя, рафинируя и модифицируя расплав. С момента заполнения тигля расплав выдерживают в течение.
3 мин, после чего флюс снимают с зеркала расплава и последний разливают в формы.
Плавка магниевых сплавов. Магний и его сплавы при нагреве на воздухе окисляются и загораются, поскольку окисная пленка магния рыхлая и не защищает его от дальнейшего окисления. Поэтому плавку магниевых сплавов надо вести под защитой флюсов или с добавкой 0,01—0,02 % Be. В цехах литья по выплавляемым моделям для плавки магниевых сплавов рекомендуется применять индукционные тигельные печи промышленной частоты ИПМ (рис. 7.10) с вставным стальным тиглем (см. табл. 7.7). Магниевые сплавы готовят в два приема: сначала предварительный сплав, в затем рабочий сплав.
В раскаленном тигле расплавляют флюс ВИ-2 в количестве 1—2 % массы шихты, затем в него загружают чушковый магний, алюминий, лигатуру и расплавляют шихту. Расплав нагревают до 680—700 °С и вводят в него легирующие низкоплавкие элементы (в зависимости от состава сплава). Затем расплав доводят до температуры 700—720 °С и рафинируют его флюсами с перемешиванием в течение 5—6 мин. С поверхности расплава снимают шлак и загрязненный флюс, наносят свежий флюс, повышают температуру расплава до 750—780 °С и выдерживают при этой температуре 12— 15 мин, чтобы расплав отстоялся. После этого берут пробы на анализ
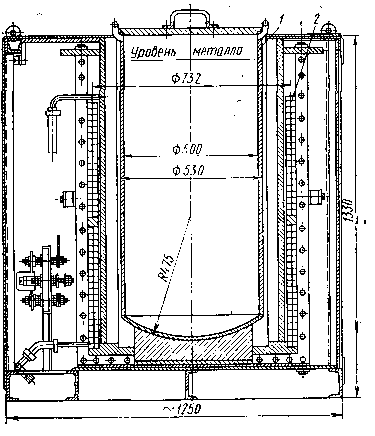
Рис. 7.10. Схема индукционной тигельной печи промышленной частоты для плавки магниевых сплавов:
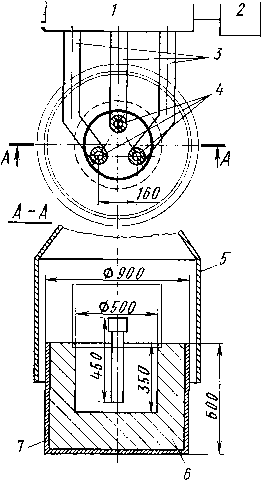
Рис. 7.9. Схема дуговой электропечи для плавки универсального флюса:.
1 — трехфазиый трансформатор 380/24;.
2 — щит управления; 3 —* шины: 4 —* графитовые электроды; 5 — вытяжной зоит; 6 — футеровка из шамотиого кирпича; 7 — каркас печи
1 — стальной тигель; 2 —• индуктор
химического состава, охлаждают расплав до 700—680 °С и разливают в изложницы. Тигель очищают от остатков флюса, шлака и других загрязнений и подготовляют к следующей плавке.
Рабочий сплав в тигельной печи готовят так же, как предварительный сплав, только в шихту для рабочего сплава кроме чушковых свежих металлов и лигатур загружают отходы данного сплава. После нагрева расплав модифицируют углеродсодержащими материалами (мел, мрамор, магнезия) и рафинируют флюсом ВИ-2, затем охлаждают до температуры заливки и разливают в формы. При этом сливают не весь расплав, 10—15 % остается в тигле и его сливают в изложницы. Тигель очищают и готовят к следующей плавке.
Плавка титановых сплавов. Вследствие большого сродства титана к кислороду и образования нитридов титана при нагреве его в воздушной среде плавка титана и его сплавов возможна только в вакууме или в среде нейтральных газов.
Для литья по выплавляемым моделям наибольшее распространение находят дуговые гарииссажные электропечи с расходуемым электродом (рис. 7.11). Графитовый тигель 2, в котором происходит плавка, охлаждается водой, протекающей в медной обойме 5. Температуру внутренней поверхности тигля регулируют с таким расчетом,
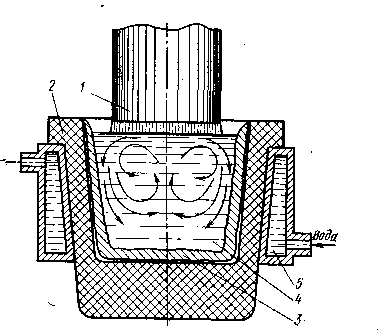
Рис. 7*11. Схема плавни в дуговой гарнис-саж ой электропечи с расходуемым электродом.
.
чтобы на стенках тигля в течение всего процесса плавки оставался нерасплавленным слой титанового сплава толщиной 10—15 мм, так называемый гарниссаж 3. Гарниссаж препятствует непосредственному контакту тигля с ванной расплава 4,полученной от расплавления расходуемого электрода /, и, таким образом, предохраняет сплав от насыщения углеродом.
В табл. 7.9 приведены технические характеристики электропечей для плавки титановых сплавов. Одна из печей (ОКБ-956) с поворотным тиглем для заливки расплава в форму представлена на рис. 7.12.
Для заливки тонкостенных отливок в плавильно-заливочных камерах устанавливают центробежные установки.
.
Таблица 7.9.
Техническая характеристика дуговых вакуумных гарниссажных электропечей
Параметр | ОКБ-956 | ОКБ-Ю72 | ОКБ-1007 |
Емкость плавильной ванны, кг | 25; 60 | 100 | 250 |
Постоянный ток, А | 14 000 | 14 000 | 25 000 |
Напряжение, В | 28—32 | 34 | 38—40 |
Остаточное давление, Па | 0,13 | 0,13 | 0,65 |
Максимальные размеры электрода, мм: | |||
длина | 500 | 650 | 485 |
диаметр | 200 | 300 | 460 |
Число устанавливаемых электродов | 1 | 1 | 4 |
Максимальные размеры формы, мм: | |||
длина (диаметр) | 800 | 600 | 800 |
ширина | — | 600 | 800 |
высота | 500 | 600 | 1200 |
Число установленных форм | 1 | 1 | 4 |
Скорость плавки, кг/мин | 5—8 | 3—6 | 10—15 |
Удельный расход электроэнергии, | 7,4 | 2,3 | 2,5 |
кВт-ч/кг | |||
Длительность цикла, ч | 2; 2,5 | 0,2 | 6,5 |
Расход охлаждающей воды, м 8 /ч | 25 | 40 | 45 |
Габаритные размеры печи, мм: | |||
длина | 7400 | 12 000 | 11 350 |
ширина | 2 800 | 7 560 | 6 750 |
высота | 5 275 | 6 800 | 5175 |
Масса печи, т | 176 | 50 | 42 |
Рис. 7,12* Дуговая гарииссажиая электропечь ОКБ-960.
.
Плавка в электродуговых гарниссажных печах с расходуемым электродом имеет и недостатки—затруднен перегрев расплава и переплав отходов, невозможно выдерживать расплав в печи и др, В связи с этим ведутся работы по применению других источников теплоты для вакуумных гарниссажных печей. Для этих целей исполь-
Рис. 7.13. Электронно-лучевая четырехпушечная гарннссажиая установка
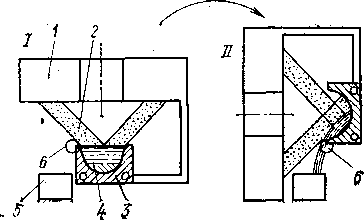
Рис. 7.14. Схема гарннссажной электропечи с поворотной радиальной пушкой;.
/ — положение при плавке; II — положение при заливке; 1 — электроиио-лу-чевая пушка; 2 — электронный луч; 3 — медный тигель; 4 — расплав; 5 — форма; 6 — ось поворота.
.
зуют аксиальные и радиаль-ные электронные пушки. На их базе созданы гарниссажные установки для плавки титана и других тугоплавких ме таллов.
На рис. 7.13 показана электронно-лучевая гарниссажная промышленная установка для литья тугоплавких металлов, в которой находятся четыре аксиальные пушки мощностью 120 кВт каждая. Емкость тигля для плавки титана 6 л. Печь снабжена системой дистанционного наблюдения и управления процессом.
В отличие от дуговой плавки с расходуемым электродом электронно-лучевой нагрев позволяет расплавлять кусковой шихтовый материал, в том числе и отходы применяемых сплавов, легировать сплав введением легирующих компонентов в твердую шихту или в расплав в хбде плавки. При этом представляется возможным выдерживать расплав в течение любого времени и перегревать его до необходимой температуры. Кроме того, электронный нагрев позволяет создавать глубокий вакуум непосредственно над зеркалом ванны расплава для максимальной очистки его от вредных примесей.
На рис. 7.14 показана схема гарниссажной электропечи с поворотной радиальной пушкой, что позволяет эффективно обогревать ванну в процессе поворота тигля для слива расплава в форму.
Наряду с дальнейшими работами по внедрению электр онно-лу-чевой плавки ведутся работы по плазменному нагреву. Для получения плазмы используют электрический разряд в среде газа. Обычно плазму получают с помощью дугового разряда в плазменной горелке. Проходя в плазменной горелке через дуговой разряд, газ ионизируется и выходит из сопла с температурой в несколько тысяч градусов. Полученную таким образом плазму применяют для гарниссажной плавки титана и других тугоплавких металлов.