Формовка холодных оболочек сыпучим наполнителем. На дно.
опоки, представляющей собой коробку, насыпают небольшой слой наполнителя, чтобы верхний уровень торца литниковой вороньи оболочки был примерно на уровне верха опоки; ставят оболочки, воронки закрывают крышками и насыпают наполнитель. В него могут быть введены связующие, например борная кислота (табл. 6.23). Опоку ставят на вибростол с амплитудой колебаний 0,5—0,6 мм и частотой колебаний около 1400 в минуту. После уплотнения наполнителя снимают крышки и формы направляют для прокаливания в печь.
Оболочки прокаливают 7—10 ч и заливают их горячими, при литье стали они имеют температуру 800—900 °С; с момента извлечения форм из печи и до их заливки упакованные оболочки не успевают охлаждаться. При использовании опорного наполнителя оболочки нагревают постепенно и заливают горячими. Однако процесс прокаливания заформованных оболочек длителен, требует значительных затрат энергии и большого расхода жаростойких опок. При этом к оболочке, пропитанной модельным составом, затруднен доступ кислорода воздуха, необходимый для выжигания остатков модельного состава. В качестве наполнителя чаще всего применяют обычный кварцевый песок (кристаллический кварц) как один из доступных материалов. Однако это нередко приводит к искажению размеров оболочек и, следовательно, отливок, так как примыкающие к опоке наружные слои песка нагреваются до температуры полиморфного превращенЙя (573 °С) и расширяются раньше, чем прилегающие к оболочке слои песка и сама оболочка. Расширяющийся песок, ограниченный стенками опоки, расширение которой невелико, давит на оболочку, что может вызвать ее деформацию или разрушение. При дальнейшем нагреве оболочки до температуры полиморфного превращения кварца, ее расширению в этот период препятствует наполнитель, оказывая на оболочку значительное давление. В результате наполните^ сжимает оболочку, в ней образуются трещины. Давление может вызвать даже деформацию (выпучивание) опоки, либо образование в ней трещин.
Следовательно, лучшим вариантом является прокаливание оболочек и заливка их без опорного наполнителя. Если это невозможно, то рационально прокаливать оболочку без наполнителя, а затем заливать в обогреваемых контейнерах (также без опорного наполнителя), либо упаковывать перед заливкой в горячий опорный наполнитель. При этом следует применять оболочковые и наполнительные материалы, не имеющие полиморфных превращений, например НК.С, шамот, электрокорунд.
Формовка прокаленных горячих оболочек. В серийном производстве целесообразно использовать установки с псевдоожиженным слоем и располагать их возле печи прокаливания. Отличаются они.
Таблица 6.24.
Твердеющие опорные наполнители
Составляющие | Количество, % по массе | Составляющие | Количество, % по массе |
1. Цемент глиноземистый | 12—15 | . 2. Пульвербакелит (смо | 1,0—1,5 |
марки 500 | ла № 104) | ||
Песок кварцевый 1К020 | 88—85 | Песок 1К020 | 99—98,5 |
Вода | 30—40 | Смачиватель песка | 0,5—0,6 |
(сверх 100) | (сверх 100) |
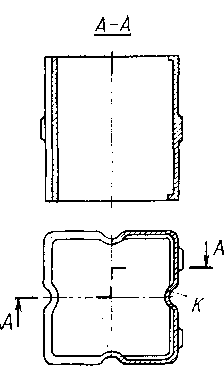
Рис. 6.27. Неразъемная опока из жаростойкой стали с компенсатором теплового расширения К.
.
тем, что песок приводят в псевдоожи-женное состояние, включая подачу горячего воздуха с помощью ножной педали только в момент погружения в него оболочки, а после оседания песка в оболочку заливают расплав и далее в этой же установке отливки остывают до следующей плавки.
Формовка твердеющим опорным наполнителем. Примерные составы смесей приведены в табл. 6.24. Смесь 1 готовят в лопастном смесителе, наливают воду, насыпают цемент и перемешивают 2— Змин; не прекращая перемешивания, насыпают песок и перемешивают еще 6—7 мин. На стол вибратора ставят строганую подопочную плиту, на которую устанавливают блок модели с оболочкой, приклеивают его модельным составом и устанавливают опоку без дна из жаростойкой стали.
^.
Внутреннюю поверхность опоки обкладывают картоном для обра-зовани зазора между опокой и наполнителем (рис. 6.27). Наливают наполнитель, включают вибромашину с амплитудой 0,3—0,4 мм при частоте вибрации 1600—1500 колебаний в минуту и по мере оседания смеси ее добавляют совком. Стол вибромашины имеет приемник для стекания воды. Продолжительность вибрирования 10— 15 мин, после чего формы снимают со стола и устанавливают на стеллажи для медленной сушки.
В способе, предложенном М. Г. Глазом и Н. Г. Черняком, используют преимущества сухого сыпучего наполнителя, при этом применяют смесь 2 (см. табл. 6.24). Вследствие перехода пульвер-бакелита из состояния А в состояние С при нагреве форм для выплавления моделей смесь приобретает высокую прочность, а в процессе покаливания она, вследствие деструкции связующего, становится непрочной и не препятствует- усадке отливок. Формовать блоки можно только в опоках с дном.
6.8. ПРОКАЛИВАНИЕ ОБОЛОЧКОВЫХ ФОРМ.
При прокаливании решаются три задачи: удаление газотворных составляющих, повышение прочности, нагрев оболочки для лучшего заполнения полостей металлическим расплавом. Прокаливают оболочки в окислительной среде нагревом до 800—1100 °С с последующей выдержкой. При этом протекают процессы: нагрев оболочки; удаление из нее газотворных составляющих, источником которых является влага; удаление остатков модельного состава и продуктов.
деструкции сЁЯзующегб; гидролитическая поликоНденсация связующего; образование кристаллических структур связующего; термическое расширение оболочки и полиморфные превращения; образование капиллярных каналов.
Передача теплоты оболочке и перемещение теплоты в толще последней — главные процессы; все другие — следствие их. Отметим, что оболочковая форма обладает низкой эффективной теплопроводностью и она увеличивается с увеличением температуры. Например, теплопроводность кварцевой оболочки 0,29 Вт/(м-°С) при 600 °С,.
0,35 Вт/(м • °С) при 1100°С, 0,56 Вт/(м-°С) при 1500 °С.
Оболочковые формы, как правило, заливают горячими и поэтому нельзя отрывать прокаливание их от заливки. Температура формы должна быть при заливке сплавов: на основе железа 800—900 °С, на основе никеля 900—1100 °С, на основе меди 600—700 °С, на основе алюминия и магния 200—250 °С. При заливке сплавов на основе меди, алюминия и магния оболочки после прокаливания охлаждают.
Главные источники газов: модельный состав (табл. 6.25), впитавшийся в оболочку, и продукты деструкции связующего [85, 86]. Процесс их удаления состоит из двух стадий: газификации и сжигания продуктов деструкции; выжигания углерода, отложившегося в капиллярах оболочки. Цвет излома полностью прокаленной оболочки белый или. розовый. Цвет излома от черного до серого — признак того, что в капиллярах есть углерод и оболочковая форма недостаточно газопроницаема; полученные отливки поражены газовыми раковинами и имеют повышенное содержание углерода в поверхностном слое стальных отливок.
.
Таблица 6.25.
Содержание модельного состава н углерода в образцах оболочек после выплавления
N. Теплоноситель | Количество модельного состава | Содержание углерода, % к массе оболочки | |
г/кг оболочки | % к массе оболочки | ||
Вода, 97—99 °С | 38 | 3,8 | 3,0—3,2 |
Модельный состав, 125—130 °С | 70 | 7,0 | 5,8-6,0 |
Воздух (поток), 170—180 °С | 51 | 5,1 | 4,2—4,4 |
Отметим, что чрезмерная прочность оболочки может привести к трещинам в отливках вследствие торможения их усадки.
К оболочке, представляющей собой капиллярно-пористое тело, Теплота может быть передана излучением (радиацией), конвекцией, теплопроводностью или сочетанием этих процессов. Состав газов в печи должен быть окислительным, чтобы выгорели все остатки модельного состава и продукты деструкции связующего, включая углерод. Продукты сгорания следует непрерывно удалять из области нагрева оболочек. С этих позиций рассмотрим печи для прокаливания оболочковых форм.

Рис. 6.28. Термограммы иагреваоболочек в проходной электропечи сопротивления (/ и 2) и проходной газовой печи 4).
.
Электрические печи. В печах сопротивления оболочковые формы получают теплоту излучения от спиралей и кладки печи. При этом теневые части форм непосредственно не получают теплоту,, в результате чего неизбежно соi здается температурный градиент в различных частях оболочки и замедляется процесс нагрева (рис. 6.28). Последний особо длителен при прокаливании оболочек в опорном наполнителе, масса которого в 8—16 раз больше массы оболочек. В электропечах трудно поддерживать избыток кислорода, необходимый для окисления продуктов деструкции остатков модельного состава, связующего и углерода. Электрические печи сопротивления мало пригодны для прокаливания оболочек и совершенно непригодны, когда применяют выжигаемые модели; их заменяют газовыми.
Газовые печи. В печах этого типа также теплота передается, главным образом, от горячих газов более холодным оболочкам или опокам. Но в отличие от нагрева в электрических печах газы омывают оболочки и опоки, и нет теневых участков (см. рис. 6.28). При этом в газовых печах легко поддерживать необходимый окислительный состав газов. Особенно интенсивно протекают процессы при 550—600 °С, газифицируется и сгорает модельный состав, и при 80Э—900 °С, выгорает углерод из оболочки. При прокаливании в опорном наполнителе требуется теплота для нагрева последнего и затрудняется доступ кислорода к оболочке. Это увеличивает продолжительность прокаливания прймерно в 10 раз по сравнению с прокаливанием истинных оболочек.
Лучший режим нагрева в газовых печах —■ мягкий; он возможен при нижних (рис. 6.29) топках, так как это обеспечивает рециркуляцию газов, что снижает расход топлива в отличие от печей только с острым верхним нагревом. Газы при движении из нижних топок вверх увлекают часть отходящего газа, смешиваются с последним и таким образом осуществляется рециркуляция.
При движении газа и продуктов сгорания вниз происходит пере-дача теплоты оболочкам или опокам, установленным на поддонах. Между днищами поддонов предусматривают промежутки 50—60 мм для осуществления рециркуляции и удаления отходящих газов через боров в дымовую трубу. Через верхние горелки вдувают газ с избытком воздуха только для горения модельного состава и углерода. Устройства для ввода в печь поддонов с оболочками и извлечения их из печи аналогичны применяемым в проходных электропечах. Дверки поднимают и опускают с помощью редукторов с электромо
Рис. 6.2 9. Схема газовой прокалочной печи.
.
торами, причем электрическая схема такова, что невозможно открыть дверь А при открытой двери Б, чтобы в работающей печи не нарушать движение газов и не создавать неконтролируемого подсоса воздуха [47].
Печи с высокотемпературным псевдоожиженным слоем огнеупора.
Схема такой печи с устройством для заливки к охлаждения оболочек (без механической части и крышек) приведена на рис. 6.30 [19]. Топливом служит газ, поступающий через трубки 1 в слой электрокорунда 2 с зернами размерами 0,1—0,12 мм. Газ в смеси с воздухом нагревает электрокорунд и вызывает его «кипение». Оболочковые формы с закрытыми воронками устанавливают в решетчатую кассету и погружают в нагретый до 900—1000 °С псевдокипящий электрокорунд. Оболочка омывается со всех сторон находящимися во взвешенном состоянии зернами горячего электрокорунда и газами, содержащими избыток кислорода, достаточный для сжигания остатков мебельного состава и продуктов деструкции связующего.
Таким ^образом, при этом способе прокаливания нагревается только оболочка, без наполнителя; теплота оболочке передается одновременна излучением (радиацией), конвекцией и теплопроводностью; в газовой смеси поддерживается количество кислорода, достаточное для сгорания продуктов деструкции модельного состава, связующего и углерода; температура псевдокипящего слоя соответствует оптимальной для быстрого протекания реакции газификации и окисления органических остатков в оболочке.
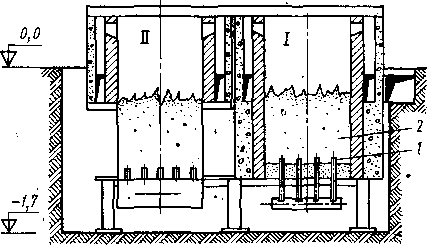
Рис. 6.30. Схема установки для прокаливания, заливки и охлаждения оболочек в псевдокипя-щем слое электрокоруида:.
/ — прокалнванне; II — залив* ка и охлаждение отливок.
Вследствие изложенных особенностей продолжительность прокаливания шестислойной оболочки составляет 6—10 мин. За это время выгорает практически весь углерод, что важно при получении отливок, в которых недопустимо повышение его содержания. Рядом с печью прокаливания расположена установка для заливки оболочек в горячем наполнителе и создания условий направленного затвердевания отливок. Оболочки в кассете переносят и погружают в псев-доожиженный электрокорунд, затем прекращают подачу газовоздушной смеси, наполнитель оседает и обжимает оболочку. Она готова к заливке. После заливки в слой электрокорунда снизу подают сжатый воздух для создания условий направленного затвердевания отливок. Если недопустимо обезуглероживание поверхностного слоя отливок, воздух заменяют газом, не содержащим кислород. Газ препятствует поступлению кислорода воздуха к поверхности отливок и служит источником пироуглерода, откладываемого в оболочке.
Следует отметить, что прокаливать в псевдоожиженном слое электрокорунда необходимо оболочки из термостойких материалов, позволяющих нагревать оболочки без растрескивания с любой скоростью. Таким свойством в наибольшей степени обладает НКС (табл. 6.26). Из него следует также изготовлять защитные колпачки для предотвращения попадания витающих зерен электрокорунда.
Таблица 6.26.
Режимы прокаливания и заливки оболочковых форм (расплав типа стали)
Форма | Основа оболочки | Линейное расширение при иагреве до 1100°С, % | Продолжительность нагрева при прокаливании, ч | Температуря оСолочки, °С | |
после. прока. ливания | при заливке | ||||
Истинно оболочковая | нкс | До 0,04 | 0,1—0,2 | 900—1100 | 20—1000 |
Оболочковая | Белый электроко-руид. Суспензия — дистен-силлиманит Обсыпка — белый электрокорунд Шамот высокоглиноземистый | До 0,4. До 0,4 До 0,4 | 2.5—3. 2.5—3. 3—3,5 | 900—1100. 900—1100. 850—900 | 850—950. 850—950. 800—850 |
Оболочковая в сыпучем сухом опорном наполнителе | Кристаллический. кварц | 1,2—1,4 | 5-6 | 900—950 | 850—900 |
Примечания. I. При иагреве оболочек из кристаллического кварца происходит скачкообразное полиморфное превращение прн 573 °С.
2. Только оболочковые формы из кристаллического кварца заформовывают в опорный наполнитель, остальные прокаливают и заливают без опорного наполнителя.
в полость оболочковых форм. Возможны два способа изготовления колпачков: спеканием из порошков НКС или по технологии получения оболочковых форм с использованием НКС в качестве огнеупорной основы суспензии и обсыпочного материала.
Колпачки должны герметично закрывать внутреннюю полость литниковой воронки и легко сниматься.