отработку ЛПС для исключения образования в отливках недопустимых дефектов;.
нормализацию как результат обобщения ЛПС применительно к конкретной номенклатуре литых деталей и характеру их производства.
Сравнительный анализ вариантов. Производство однотипных литых деталей обычно может быть обеспечено при использовании различных вариантов ЛПС. Намечая несколько вариантов и сравнивая их между собой, можно выбрать наиболее экономичный. Варианты сравнивают по нескольким показателям.
Выход годного определяют по уравнению
где G
— масса единичной отливки, кг; G
— масса шихты, кг, определяют с учетом потерь на угар; N
— число отливок в блоке; V
и У
— объемы единичной отливки и ЛПС, дм
, определяют по чертежу без учета коэффициента объемной усадки |3 или по результатам взвешивания.
В практике производства отливок по выплавляемым моделям обычно ВГ = 0,1-7-0,6. Используя (3.19), можно получить выражение для относительного расхода залитого в форму металла, приходящегося на одну отливку (кг/отл.), это выражение

позволит перейти к сравнению вариантов по металлоемкости.
Разность расходов залитого металла на отливку при сравнении двух вариантов ЛПС будет

Снижение металлоемкости при увеличении ВГ на 0,1
Вариант ЛПС | Снижение металлоемкости, кг | ||||
Исходный | При улучшении ВГ | ||||
ВГ | ^зал. о, кг/отл. | ВГ" | ^зал о, кг/отл. | на одну отливку | на 1000 отлнвок |
0,1 | 1 | 0,2 | 0,5 | 0,5 | боа |
0,2 | 0,5 | 0,3 | 0,33 | 0,17 | 170 |
0,3 | 0,33 | 0,4 | 0,25 | 0,08 | 80 |
0,4 | 0,25 | 0,5 | 0,2 | 0,05 | 50 |
0,5 | 0,2 | 0,6 | 0,167 | 0,033 | 33 |
0,6 | 0,167 | 0,7 | 0,143 | 0,024 | 24 |
Здесь и далее число штрихов означает условный номер варианта. Данные табл. 3.11 иллюстрируют степень снижения металлоемкости при G
= 0,1 кг и повышении ВГ всего на 0,1.
Пример 4. Поясним роль ВГ подробнее на конкретном примере уже приводившейся выше стальной детали «рамка» (см. рнс. 3.12), отливаемой по ЛПС типа I (центральный стояк). Примем для этого варианта: масса отлнвки G
= 0,015 кг, N
= 7-4 = 28 отливок в блоке; центральный стояк круглый диаметром d
= 30 мм и высотой he = 202 мм. Не учитывая брака и пренебрегая массой питателей и некоторым увеличением массы на участке воронки, получим, что масса блока при плотности стали р = 7,8 кг/дм
будет

откуда, при коэффициенте объемной усадки (5 = 0,06,

Для второго варианта при центральном стояке того же диаметра, но высотой = 422 мм, параметры будут следующие: N" — 17-4= 68 отливок,

Соответственно металлоемкости по вариантам составят

Вариант 2 экономичнее по металлоемкости в сравнении с вариантом 1 на

т. е. на 40 % массы отливки.
Показатель ВГ достаточно хорошо отражает металлоемкость ЛПС без учета брака. Это позволяет сравнивать варианты до реализации их в производстве. Однако ВГ недостаточно полно отражает металлоемкость ЛПС с учетом брака или изменения G
. В самом деле, из.
формулы (3.19) следует, что ВГ может быть улучшен путем снижения не только удельной массы ЛПС, но и массы бракованных отливок, как в рассматриваемом примере с деталью «рамка», или путем задания излишних напусков и припусков на механическую обработку.
Отметим попутно, что увеличение высоты стояка закономерно приводит к снижению трудоемкости изготовления отливок благодаря следующему:.
сокращению числа необходимых стояков и числа спаев при звеньевой сборке моделей. Если число стояков при варианте 1 принять за 100 %, то при варианте 2 их потребуется лишь ~17%.
меньшему падению температуры металла в период заливки, так как сокращается число переносов ковша от формы к форме. При емкости ковша 35 кг потребуется блоков
меньшему числу установок блока с отливками на станок для их отрезки; отношение числа установок в вариантах 1 и 2 равно 100 к 17 по числу необходимых блоков.
Коэффициент выхода отливок, определяемый как отношение числа годных отливок N
к числу залитых N
,
В примере с отливкой «рамка» принято, что абсолютная высота нижнего и верхнего участков стояка с дефектными отливками не зависит от общей высоты стояка, т. е. ощбее число бракованных отливок в блоке для обоих вариантов одинаково
Лбр = Лвр = Лвр = 20 отливок,
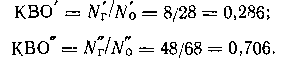
КВО вариантов будет соответственно равно
При анализе КВО следует иметь в виду, что брак отливок в большинстве случаев может быть отнесен не только за счет ЛПС, но и определяется особенностями технологического процесса литья и технологичностью отливки с учетом сплава. В примере, взятом из производственной практики, толщина стенки «рамки» с учетом ее протяженности находится в предельной области.
Коэффициент использования залитого в форму расплава
где (7
— масса единичной детали, кг.
КИР не следует смешивать с более общим показателем — коэффициентом использования металла КИМ, равным отношению массы готовой механически обработанной литой детали к норме расхода металла, в которой учитываются, с одной стороны, безвозвратные потери, с другой — возврат литников и отходов в шихту. Вместе с тем, очевидно, что КИР влияет на КИМ.
При G
— const повышению КИР способствует также уменьшение массы отливки путем сокращения припусков на механическую обработку и напусков.
Коэффициент использования площадей, кг/м

Таким образом, анализ позволил выявить возможность повышения КИР в 2 раза и более по сравнению с реально использованным вариантом 1.
КИР по аналогии с ВГ дает возможность вычислить расход металла, залитого в форму, на деталь:

Для детали «рамка» имеем

Соответственно, снижение расхода залитого металла (кг/деталь) при сравнении вариантов будет

Второй вариант в примере дает снижение на 0,124 кг/деталь, т. е. больше массы самой детали более чем в 9 раз.

где 5
б
— площадь блока отливок с ЛПС в плане, считая по габаритным размерам, м
2
В рассматриваемом примере при диаметре блока = 0,128 м имеем 5б = = 0,013 м
2
, откуда

Анализ вариантов в данном случае позволил найти решение для сокращения необходимой площади в 6 раз, в том числе для сокращения площади рабочего пространства прокалочных печей и транспортных средств. Результаты расчета сведены в табл. 3.12, из которой видио, что вариант 2, несмотря на небольшое усовершенствование, дает более экономичное использование трудозатрат, металла и площадей.
Укажем также на работу [35], где решена на ЭВМ задача, включающая расчеты: оптимального расположения и числа моделей в блоке; масс отливок и стояков; коэффициента выхода отливок. Сроки разработки технологических процессов сокращены в 15 раз.
Отработка ЛПС., Даже тщательно спроектированная ЛПС требует доработки по результатам изготовления пробных отливок. При отработке технологического процесса следует исходить из того, что ЛПС с отливкой данного наименования представляет собой уникальный комплекс, в котором небольшие, на первый взгляд, изменения размеров могут существенно отразиться на качестве отливки. От-
Показатель | Вариант ЛПС | Эффект | |
1 | 2 | ||
Диаметр стояка, мм | 30 | 30 | |
Высота стояка, мм | 202 | 424 | — |
Число отливок в блоке: | |||
всего | 28 | 68 | +40 |
годных | 8 | 48 | +40 |
ВГ | 0,259 | 0,288 | +0,029 |
Заливается из одного ковша вмести | |||
мостью 35 кг: | |||
блоков | 23 | И | — 12 |
годных отливок | 176 | 480 | +304 |
КВО | 0,286 | 0,706 | +0,420 |
КИР | 0,068 | 0,187 | +0,119 |
Металлоемкость, кг: | |||
отливки М зал 0 | 0,058 | 0,052 | —0,006 |
детали Мда л# д | 0,193 | 0,069 | —0,124 |
КИП, кг/м а | 9,3 | 55,6 | +46,3 |
метим некоторые практические приемы, направленные на устранение характерных дефектов в отливках.
Недоливы — это незаполнение металлом участков тонких сечений и кромок. При обнаружении систематических недоливов прежде всего следует увеличить скорость заливки путем увеличения площади суженного сечения /
или гидростатического напора Н
в этом сечении (см. формулу (3.15)1. Нередко недостаточная скорость заливки предопределяется малым верхним диаметром литниковой воронки, когда рабочий-заливщик вынужден притормаживать подачу металла во избежание его выплескивания из литниковой воронки. Это же явление может наблюдаться, если угол конусности воронки более 60°. В некоторых случаях скорость нарастания гидростатического напора в суженном сечении удается увеличить путем создания местных суженных сечений по высоте центрального стояка или боковой прибыли (см. табл. 3.9).
Для исключения недоливов можно также повышать температуру литейной формы непосредственно перед заливкой, например, путем увеличения температуры прокаливания форм, сокращения продолжительности выстаивания форм в период от выдачи из прокалочной печи до заливки, применения теплоизолирующих слоев формы.
В отдельных случаях, когда стенки отливки или кромки лопаток чрезмерно тонки, и имеющиеся в цехе возможности повышения начальной температуры формы исчерпаны, необходимо увеличить толщину стенок и кромок в возможных пределах.
Усадочные раковины проявляются обычно в виде концентрированных пустот, осевой рыхлости или рассеянной пористости. Учитывая, что объемная усадка является органическим свойством затвердевающего металла, желательно не ограничиваться визуальным осмотром пробных отливок, а провести контроль, например, просвечиванием их рентгеновскими лучами.
Если для устранения усадочной раковины прибегают к увеличению размеров прибыли, то необходимо следить, чтобы при этом был исключен дополнительный обогрев теплового узла отливки. В противном случае более мощная прибыль может не только не дать желаемого эффекта, но и вызвать усиление усадочной раковины в отливке. Поэтому с увеличением прибыли необходимо одновременно несколько отдалить ее от отливки путем удлинения шейки. Даже при достаточной по объему прибыли, если она расположена слишком близко к тепловому узлу отливки, затвердевание этого узла замедляется и часть усадочной раковины проникает в отливку.
Сокращение объема усадочной раковины в отливке может быть достигнуто за счет замедления процесса затвердевания отливки. Покажем это на примере ГАЗа [91 ]. В цехе точного литья на детали «коромысло клапана» из стали 45 брак по усадочным раковинам был сокращен на 30—40 % благодаря применению форм с малотеплопроводным слоем покрытия, содержащего пеностекло. Этот слой наносился поверх обычной пятислойной этилсиликатной оболочки и в процессе обжига литейных форм вспенивался с увеличением толщины слоя с 0,8—1 до 2,3—5,6 мм. В результате затвердевание отливки замедлилось и питание ее осуществлялось более полно.
В отдельных случаях при сравнительно небольших размерах нижних тепловых узлов избежать образования усадочной раковины удается применением холодильников. В некоторых крупных отливках с протяженными стенками возникновение местной осевой рыхлости оказывается неизбежным или требует применения чрезмерно развитых ЛПС. В этих случаях иногда возможно допустить наличие местной осевой рыхлости, не выходящей на поверхность отливки.
Неметаллические включения могут заноситься в форму при заполнении ее потоком высокой турбулентности, характеризуемой известным числом Рейнольдса.
Re = 64R/v, (3.25).
где v — средняя линейная скорость потока расплава, м/с; v = = Y%gH
R— гидравлический радиус, R = f/P (/ — площадь живого сечения потока; Р — смоченный периметр); v—кинематическая вязкость, для сталей, медных и алюминиевых сплавов в первом приближении v = 6 -10
м
/с. Имеется
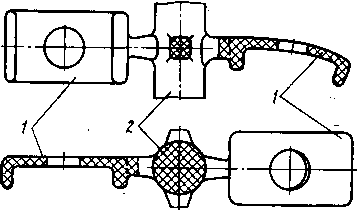
Рис. 3.17. Влияние ориентации отливки в форме на коробление выплавляемых моделей.
1 — модель; 2 — стояк.
Рекомендации по нормализации ЛПС
Нормализуемый фактор | Тип производства * | Масса единичной отливки, кг (по стали) | ||||
Объект | Параметр | >0,5—2 | >2 — 8 | >8 | ||
Тип ЛПС | о, с | I—IV | I—III, VI, VII | V, VI, VIII | ||
м | I, II | — | ||||
Блок. отливок | Высота, мм | 0, с | 3-400 ** | 3-400 ** | 3-400 ** и индивидуально | Индиви. дуально |
м | ||||||
Ширина в плане, мм | 0, с | По размерам норма оснастки и приспособлений | лизованной | Ограниченно | ||
м | — | |||||
Цен. траль. ный. стояк | Форма. сечения | 0, с | Круглая | |||
м | Экономически. целесообразная | |||||
Высота . с литниковой воронкой, мм | 0, с | 3-400 ** | ||||
м | S&400 ** | |||||
Прибыль | Конструкция и размеры | 0, с, м | — | С учетом конкретной номенклатуры отливок | ||
Диаметр. выпора | о, с, м | 0,3—0,35 от верхнего основания прибыли | ||||
Литни. ковая. воронка | Конструк. ция | 0, с, м | Конусная с углом при вершине 55—60° | |||
Диаметр. верхнего. сечения | 0, с, м | По табл. ЗЛО | ||||
Зумпф | Высота, мм | 0, с, м | 30—40 |
* О — опытное; С — серийное; М — массовое.
** По высоте рабочего пространства печей для прокаливания форм.
в виду, что расплав к концу заполнения формы имеет температуру не менее чем на 20 °С выше температуры ликвидуса и представляет собой ньютоновскую жидкость, вязкость которой не зависит от уровня внутренних напряжений.
Уровень поражения отливок неметаллическими включениями может быть снижен путем сокращения Re в 1,2—1,5 раза. При этом во избежание увеличения брака отливок по недоливу и усадочной раковине, необходимо соблюдать удельную скорость заливки Q
в соответствии с формулой (3.11). Проверка показала, что при отработанной технологии условные значения Re, рассчитанные по скорости подъема расплава в полости формы соответствующей отливке, обычно не превышают 2300.
Коробление отливок. При этом виде дефекта влияние ЛПС носит частный характер; приведем пример из производственной практики. При горизонтальном расположении модели (рис. 3.17) более 50 % их прогибалось под действием силы тяжести. Изменением положения модели на вертикальное этот вид дефекта был исключен.
Нормализация ЛПС при литье по выплавляемым моделям в значительной мере определяется массой единичной отливки (табл. 3.13). В мелкосерийном и опытном производстве нормализация позволяет ограничиться небольшим парком универсальных пресс-форм для ЛПС. Некоторый перерасход модельного переплава и металла при этом компенсируется снижением стоимости оснастки и более быстрым освоением производства новой номенклатуры отливок.
Для отливок массой до 1 кг целесообразно применять ЛПС в виде центральных стояков, в том числе с отходящими от них горизонтальными коллекторами (типы I и II).
В массовом производстве небольших отливок экономия на стоимости технологической оснастки меньше. Для снижения себестоимости продукции здесь основное значение имеет сокращение расхода материалов и времени на сборку модельных блоков, изготовление форм и отрезку отливок. Поэтому в массовом производстве более рационально применять индивидуальные ЛПС, у которых нормализуют отдельные элементы: литниковые воронки, центральные стояки с учетом применения металлических каркасов единого типоразмера, обеспечивающие рациональное и эффективное использование технологического оборудования и нормализованной оснастки (см. также ГОСТ 19551—74 — ГОСТ 19568—74).