Обеспечение заполняемости. При изготовлении отливок из конструкционной стали со стенками толщиной более 5. мм ЛПС обычно не содержит элементов, регулирующих скорость заливки. Последняя регулируется рабочим-заливщиком. При изготовлении отливок с более тонкими стенками (менее 5 мм) или кромками недостаточная скорость заливки приводит к недоливам. Ниже приведена схема расчета ЛПС на скорость заполнения формы сталью. Требующуюся удельную скорость заливки (кг/с) можно вычислить по эмпирической формуле
где ,&
— коэффициент пропорциональности; при подводе металла сверху = 0,05, сбоку k„ = 0,06 и снизу &
= 0,08; а
, /
— толщина и наибольшая протяженность тонкой стенки или кромки отливки.
Для отливок со стенками толщиной более 5 мм можно определять продолжительность заливки по формуле
где р
, бр —плотность, кг/м
, и удельная теплоемкость, Дж/(кг-°С) расплава; t
,
, /
л.к —температура расплава в начале и в конце заливки, °С; Ьф — коэффициент аккумуляции теплоты для материала формы, Дж/(м
-с
/
-
С); ^.„—начальная температура формы, °С.
Согласно законам гидравлики суженное сечение канала и гидростатический напор для случая ньютоновской жидкости, к которой относится заполняющий форму металлический расплав, связаны уравнением
где /о — площадь суженного сечения, м
; Н
— гидростатический напор в суженном сечении, складывающийся из высоты расплава в форме и высоты струи, падающей из ковша, м; Q
— расход расплава через суженное сечение, кг/с; [д, — коэффициент расхода, (.1 = 0,7-=-0,9; р — плотность жидкого металла; для стали можно принять р = 7000 кг/м
; g — ускорение свободного падения, g — = 9,81 м/с
При изготовлении толстостенных отливок из конструкционных сталей, к которым будем условно относить отливки со стенками толщиной более 5 мм, значением Н
можно задаваться, исходя из конструктивных соображений; однако во всех случаях должно быть для стали Н
^ 0,07 м и для алюминиевых сплавов Н
5г 0,21 м; при меньших значениях Н
получение четких кромок у отливок не гарантируется.
Для тонкостенных отливок (а
< 5 мм) имеем также
где 0—поверхностное натяжение расплава, Н/м, для среднеуглеродистой стали ст л; 1,5 Н/м; 0 —угол смачивания стенок литейной формы расплавом, рад, для етали с учетом гистерезиса смачивания можно принять 0 =3,14 рад (180°); а
— толщина тонкой стенки, м.
Расчеты по формуле (3.14) показывают^ что для вхождения расплавленной стали в полость формы шириной 1,5 мм достаточен Н
= 3 см, а для полости шириной 0,5 мм необходим уже Н
= = 9 см.
Опыты по заполнению тонких пластин длиной 80 мм, присоединенных к стояку высотой 280 мм, показали, что большинство пластин толщиной 2,3 мм заполнилось сталью до конца, все пластины толщиной 1,3 мм заполнились не на всю длину, пластины толщиной 0,7 мм заполнялись не более чем на 5 мм. Практика производства подтверждает результаты опытов: при литье по выплавляемым моделям стальных отливок с а
Рис. 3.12. Длина заполненной части стенки I (%) ко всей длине стальной отливки «рамка» в зависимости от положения на стояке (а). Схема формы (.
.
На основе экспериментальных и производственных данных установлено также, что наилучшая заполняемость достигается у отливок, расположенных в средней по высоте зоне стояка (рис. 3.12). Недоливы в верхних ярусах вызваны недостаточным гидростатическим напором. Применение в нижней части стояка зумпфа высотой 30—40 мм улучшает заполняемость отливок нижнего яруса вследствие слива в него первых холодных порций металла и более быстрого создания здесь гидростатического напора.
При подводе металла снизу по сравнению с подводом сверху из-за дополнительных потерь теплоты заполняемость снижается на 50 %, считая по площади тонкой стенки.
Зная Q
и Н
, можно определить площадь суженного сечения по формуле
Иногда вначале задаются /
, если это необходимо, например для получения модельного блока более высокой прочности. Тогда в формуле (3.15)/о и УН
следует поменять местами. Если суженное сечение совпадает с сечением шейки прибыли или питателя, то расчет /
и Н
по формулам (3.13) и (3.15) выполняют как проверочный на обеспечение необходимой скорости Q
. Суженному сечению рекомендуется придавать форму круга или прямоугольника. При нескольких суженных сечениях определяют их суммарную площадь 2/
. --.
В зависимости от конфигурации отливки и конкретных условий производства можно применять различные варианты регулирования скорости заполнения формы металлом (табл. 3.9).
Вариант А применяют наиболее часто при ЛПС всех типор. Суженное сечение отсутствует, скорость заливки регулируется заливщиком. Применение широких литниковых воронок в соответствии с табл. 3.10 обеспечивает условия для заливки с достаточной скоростью. Узкие литниковые воронки или воронки с углом конус-.
Варианты регулирования скорости заливхй
ности более 60° приводят к необходимости притормаживать заливку во избежание возможных выплескиваний металла, что, в свою очередь, способствует образованию недоливов.
При ЛПС типа I целесообразно выполнить проверочный расчет нижнего диаметра d
и высоты h
литниковой воронки как прибыли, питающей стояк [108],.
(3.16)
Где £
, V
—приведенная толщина стояка и его объем; У о, N о — объем единичной отливки и число отливок, питаемых от стояка.
Вариант Б характерен при ЛПС типа VII с питанием от нижнего горизонтального хода и верхней прибыли. Верхний участок стояка целесообразно выполнять более тонким, но толщиной не менее 20 мм, что позволит ускорить достижение необходимого напора.
Вариант В применяют при заливке через верхнюю прибыль —- ЛПС типа VI.
Рекомендуемые размеры (мм) литниковых воронок
Удельная скорость заливки, кг/с | D | m | г |
До 1 | 60 | 10 | 3 |
1—1,5 | 80 | 14 | 3 |
СД. 1. со | 100 | 18 | 4 |
Более 3 | 120 | 22 | 5 |
Примечание. Угол конусности воронки 55—60°; D — диаметр верхнего основания; m — высота цилиндрической части диаметром D, г — радиусы скругленнй.
.
Вариант Г применяют при заливке сверху в сочетании с ЛПС типов I—III и VI. На рис. 3.13 показан заливочный стаканчик с калиброванным суженным сечением, вставляемый в воронку стояка или прибыль. Диаметр выпускного отверстия в стаканчике D
(мм) рассчитывают на оптимальную продолжительность заливки т
(с); оба параметра определяют по эмпирическим формулам; для углеродистой стали при уровне металла в стаканчике, равном 70 мм,
где s — коэффициент, учитывающий способ заливки стали при температуре 1580—1610 °С; для оболочковых форм на основе кварца и этилсиликата s = 1,65 ± 0,07 при заливке через стояк, s — 2,2 ± ± 0,2 при заливке через прибыль; а
— преобладающая толщина стенки отливки, мм; G
„ — масса металла, заливаемого через стаканчик, кг.
Радиус входной кромки заливочного стаканчика принимают г = 0,25Ц>, что обеспечивает получение струи максимального сечения. Газы и воздух из стояка в период заливки- удаляются через щели между стаканчиком и формой.
Пример 3. Рассчитать литниковые каналы для кольцевой отливки с прибылями, размеры которых рассчитаны в примере 2. Последовательность расчета (см. рис. 3.8, в) следующая.
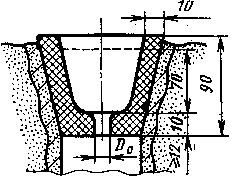
Рис. 3.13. Заливочный стаканчик с калиброванным суженным сечением.
.
1. Расчет необходимой удельной скорости заливки Фза
- Длина тонкой стенки отливки по окружности let = 3,14-280 = 880 мм, При заливке сверху А
= 0,05, тогда по формуле (3.11).
Qeaji ~ Wcr/tfcT “ 0,05-880/4,5 ^ 10 кгус.
.
2.
Выбор конструкции литниковых ходов. Для одновременной подачи металла во все прибыли останавливаемся на центральном стояке с отходящими к каждой прибыли наклонными литниковыми ходами.
3.
Расчет суммарной площади суженных сечений. Приняв Н
= 7 см, по формуле (3.15) находим
Площадь сечения одного литникового хода /
= 13,6/3 = 4,5 см. Принимаем, что суженное сечение имеет форму прямоугольника шириной 16 мм. Тогда высота сечения 4,5-100/16= 28 мм.
4. Расчет центрального стояка. Сечение стояка должно быть на 10—20 % больше суммарной площади суженных сечений, т. е. ~15 см
. Диаметр стояка соответственно будет
Высоту зумпфа принимаем равной 40 мм. Остальные размеры устанавливаем конструктивно.
В практике может встретиться случай, когда, несмотря на правильно спроектированные ходы, в отливке наблюдаются недоливы, вызванные, например, недостаточной технологичностью детали для получения ее литьем по выплавляемым моделям или с трудностями всестороннего учета факторов. При отработке ЛПС в таких случаях необходимо принять во внимание особенности процесса заполнения узкой полости литейной формы.
Как показали опыты на парафине и металле, процесс заполнения узкой полости формы может быть расчленен на четыре стадии. На первой стадии у входа в полость расплав образует выпуклый мениск. На второй стадии, когда все увеличивающийся напор преодолеет сопротивление поверхностного натяжения в мениске, стремительно заполняется часть полости формы. Третья стадия начинается с момента образования на переднем крае потока твердой корочки; скорость потока резко падает, и, наконец, поток останавливается раньше, чем полость заполнится до конца. На четвертой стадии вследствие дальнейшего возрастания напора в стояке или действия инерционных сил наблюдается прорыв передней корочки с образованием узких и маломощных вторичных потоков. Чтобы обеспечить выполнение тонких стенок в пределах второй стадии,необходимо проводить заливку при температуре расплава на 20—30 °С выше температуры ликвидуса. Г.
При отливке тонких стенок большой протяженности возможны все четыре стадии. При заполнении толстостенных отливок первая стадия не имеет значения. При быстром заполнении нагретых форм с узкими полостями достаточно горячим металлом вероятность образования корочки на головной части потока уменьшается и процесс заполнения завершается в пределах второй стадии.
Предупреждение попадания неметаллических включений. Засор. Источники засора: остатки золы из модельного состава, поломка и растрескивание оболочковой формы, заусенцы на краю формы и частицы, проникающие в форму через литниковую воронку. Распределение засора подчиняется закономерностям, которые необходимо учитывать при проектировании ЛПС.
Опыты на прозрачных моделях и натурных образцах, заливаемых стааью, позволили выявить, что падающие сверху частицы неравномерно распределяются по высоте ярусов. Наибольшее число частиц оседает в верхних и затем нижних ярусах. Наименее засоренными являются те отливки, которые располагаются ниже верхнего края литниковой воронки не менее чем на 100 мм и выше дна стояка не менее чем на 30 мм. Размеры этих участков мало зависят от общей высоты стояка. Поэтому целесообразно применять возможно более высокие стояки с зумпфом глубиной ~40 мм.
На поверхности отливки засор также распределяется неравномерно: наиболее поражены засором удаленные от питателя участки отливок; по-видимому, засор заносится туда первыми порциями металла, смывающими частицы со стенок формы. Больше 50 % засора распределяется на нижних поверхностях отливок. Менее всего поражаются засором отливки, заполняемые снизу.
Небольшая вогнутость в донной части стояка (см. рис. 3.11) гасит динамический напор падающей из ковша струи и этим предупреждает размывание формы.
Ю. А. Никишин предложил конструкцию металлоприемного устройства, предназначенного для улавливания шлака, частиц футеровки и других неметаллических включений, попадающих в форму через открытую литниковую воронку. Из литниковой чаши 1 (рис. 3.14), заполненной при заливке металлом, последний сначала попадает в кольцевой коллектор 2, затем протекает через радиальные щели 3 фильтрующего элемента. Благодаря выступу 4 над стояком 5 фильтрующая система является заполненной, и неметаллические частицы, как более легкие, находятся в верхней части каналов металлоприемного устройства.