Все это служит основой для широкого распространения процесса в условиях как опытного и серийного, так и массового машиностроения и приборостроения. В зависимости от организационных, технологических условий, степени механизации на различных предприятиях, производство отливок различается по трудоемкости, себестоимости и другим технико-экономическим показателям. Отливки по качественным характеристикам и общим затратам труда и материалов на изготовление готовых деталей более выгодны по сравнению с поковками: так, при переходе на литье по выплавляемым моделям расход металла и трудоемкость механической обработки сокращаются на 30—80 %; себестоимость изготовления деталей уменьшается на 22—80 % [41 ].
По данным различных отраслей машиностроения, замена поковок отливками по выплавляемым моделям из высокопрочной стали повышает КИМ с 0,182 до 0,754. Только в автотракторной промышленности применение литья по выплавляемым моделям дает экономический эффект свыше 2,5 млн. руб. в год [43].
Рис. 11.1. Определение коэффициента технологии механической обработки К.
.
Наиболее экономичен такой способ производства заготовок, при котором себестоимость их ближе всего к стоимости производства готовых деталей, а затраты на готовые детали при этом минимальные.
Себестоимость отливок при изготовлении моделей в металлических пресс-формах при малых сериях значительно выше, чем поковок, но с укрупнением серии различие в себестоимости литых деталей и кованых заготовок уменьшается. В этом случае решающее влияние на выбор способа изготовления заготовки оказывает трудоемкость и стоимость механической обработки.
По результатам анализа затрат на производство деталей массой 0,2—2 кг из различных заготовок (литых, кованых, штампованных и из проката) установлено, что суммарные затраты на изготовление детали из углеродистой и низколегированной сталей по отношению к затратам на заготовки могут быть выражены формулой
где Р
— стоимость заготовки; К — коэффициент, выражающий уровень совершенства технологии механической обрабтки (рис. 11.1), при обработке на универсальных станках К = 0,1, при обработке на автоматах К = 0,6; N — число размеров, по которым детали подвергают механической обработке; с — коэффициент использования металла, равный отношению массы готовой детали к массе заготовки; А — средняя точность обработки.
! Главное в развитии этого способа литья, как и всего литейного производства, состоит в том, чтобы повысить эффективность его применения и качество отливок на основе научно-технического прогресса, оптимального использования производственных фондов, материальных и людских ресурсов, улучшения управленческой и плановой работы.
В планах развития литейного производства особо подчеркивается социальный аспект, характеризуемый уровнем механизации и автоматизации производственных и транспортных процессов (тяжелый ручной труд должен быть полностью механизирован); созданием оснастки высокой производительности с минимальной вибрацией и шумом; соблюдением норм в отношении чистоты и температуры воздуха в рабочем помещении; освещенности рабочих мест.
Проекты планов обосновывают инженерными и экономическими расчетами в каждом цехе по данным его паспорта. Паспорт цеха должен содержать, например, следующие данные: уровень использования производственных мощностей; коэффициент сменности оборудования; меры по специализации производства; общий организационно-технический уровень производства; технико-экономические показатели.
Паспорт цеха должен быть составлен с использованием только документированных данных не позднее, чем через 10 дней после сдачи годового отчета вышестоящей организации. При разработке планов учитывают встречные планы и результаты социалистического соревнования, что обеспечивает единство планирования и социалистического соревнования.
Большой эффект дает бригадный метод организации труда. Примечателен в этом отношении опыт литейщиков Минского тракторного завода им. В. И. Ленина, организовавших сквозные бригады. Например, в такую бригаду входят все плавильщики, работающие в разные смены. Следствием их заинтересованности в конечном результате всего коллектива являются сокращение потерь времени, рост производительности труда.
Искусство планирования и хозяйственного руководства состоит в умении выявить те конкретные звенья, где ценой минимальных затрат можно получить наибольший конечный результат, в использовании всех стимулов повышения эффективности производства [32,115].
Плановые показатели и нормативы. В настоящее время усиливается значение натуральных показателей, определяющих потребительную стоимость, обусловленную в заданиях и договорах на поставку отливок надлежащего качества в установленные сроки.
Отклонение качества должно быть учтено в технических условиях на отливки с помощью соответствующих коэффициентов, обусловливающих повышение заинтересованности улучшения качества.
Для измерения и оценки общего объема выпуска отливок в настоящее время используют показатель нормативной чистой продукции (НЧП). Он отражает затраты живого труда в данном цехе в отличие от показателей валовой, товарной, реализуемой продукции, которые включали затраты и овеществленного труда.
НЧП суммарная оценка затрат живого труда, при котором норматив представляет собой уровень общественно необходимых затрат живого труда на единицу продукции. Определяют этот показатель при разработке оптовой цены на основе соответствующих статей калькуляции: основной и дополнительной заработной платы, отчислений социального страхования, прибыли и чистой продукции в комплексных статьях (общезаводских и цеховых расходов, текущих затрат на содержание и эксплуатацию оборудования, расходах на подготовку производства, прочих комплексных статьях).
Особую актуальность приобретает сокращение расходов материалов и энергии, так как затраты на них составляют до 73 % себестоимости отливок. В этой связи разработка и внедрение малоотходной технологии является первостепенной проблемой.
В системе плановых показателей в качестве обобщающего измерителя работы и конечных результатов должны оставаться себестоимость продукции, уровень рентабельности производства, оптовых цен.
Трудоемкость. Применение НЧП как планового показателя дает более объективую оценку результатов работы цеха, создает благоприятные условия для снижения металлоемкости и стоимости отливок, поскольку здесь нет заинтересованности в использовании дорогих и повышающих массу отливок исходных материалов. Но эта система предполагает расчет трудоемкости изготовляемой отливки,так как он позволяет установить лимит численности рабочих. Научно обоснованные нормы труда создают условия для равной его интенсивности и напряженности на разнородных работах.
В табл. 11.1 приведены примерные иормы времени на изготовление 1 кг отливок из углеродистой и низколегированной сталей в условиях серийного производства. Принята следующая технология: модели изготовляют из пастообразных составов на шприц-машинах; собирают их в блоки вручную: для получения отливок массой до 0,3 кг модели припаивают к стояку на один питатель массой 0,3—1 кг — на два питателя и массой >1 кг— на три питателя; оболочку формируют трехслойную на блоках моделей для отливок массой до.
2 кг, четырехслойную на блоках отливок массой 2—4,5 кг и пяти-шестислойные-для блоков отливок >4,5 кг; модели выплавляют в горячей воде; заформовывают в сухой опорной наполнитель, прокаливают формы в печи с механизированной загрузкой и выгрузкой; сталь пиавят в индукционных печах типа ИСТ-0,16, заливают формы расплавом вручную с помощью ковша вместимостью до 30 кг; отбивают оболочки на вибрационном станке, окончательно очищают отливки в щелочной ванне и отрезают их от литниковой системы вулка-нитовыми дисками.
По сложности отливки рекомендуется делить на следующие группы.
I группа — простые отливки, компактные, имеющие прямолинейные поверхности с незначительными выступами (1а) и несложные отливки с выступами, углублениями и отверстиями большого диаметра (16).
Масса, кг | Группа сложности отлнвок | |||||
детали | отлив кн | 1 | II | III | IV | V |
0,013 | 0,02 | 36,0 | 40,0 | 45,0 | 52,9 | 63,0 |
0,034 | 0,05 | 25,6 | 30,6 | 34,0 | 39,5 | 48,0 |
0,070 | 0,10 | 19,6 | 23,4 | 26,4 | 31,2 | 37,4 |
0,142 | 0,20 | 16,4 | 18,5 | 22,0 | 25,2 | 30,8 |
0,220 | 0,30 | 15,0 | 16,2 | 18,8 | 20,8 | 27,2 |
0,300 | 0,40 | 13,3 | 15,0 | 17,6 | 19,5 | 24,2 |
0,455 | 0,60 | 12,0 | 13,0 | 15,4 | 17,4 | 20,8 |
0,800 | 1,00 | 10,5 | 11,4 | 13,1 | 14,6 | 17,8 |
1,150 | 1,40 | 9,8 | 10,6 | 11,6 | 13,4 | 17,4 |
1,510 | 1,80 | 8,8 | 9,5 | 10,2 | 11,8 | 15,4 |
2,050 | 2,40 | 8,4 | 9,0 | 9,5 | 11,8 | 13,8 |
3,120 | 3,60 | 7,8 | 8,4 | 8,9 | 10,3 | 12,8 |
3,930 | 4,50 | 7,4 | 8,0 | 8,5 | 9,7 | 12,2 |
4,860 | 5,50 | 7,0 | 7,6 | 8,0 | 9,35 | 11,7 |
5,810 | 6,50 | 6,7 | 7,4 | 7,7 | 8,95 | 11,3 |
6,750 | 7,50 | 6,5 | 7,05 | 7,5 | 8,65 | 10,4 |
8,100 | 9,00 | 6,2 | 6,7 | 7,2 | 8,25 | 9,88 |
9,000 | 10,00 | 6,0 | 6,54 | 7,0 | 8,0 | 9,8 |
Примечание. Нормы времени следует принимать с коэффициентами в зависимо* сти от вида производства: 1,25 при мелкосерийном; 0,75 прн крупносерийном и массовом» комплексно-механизированном; 0,7 прн автоматизированном массовом. Следует также учи» тывать сложность приготовления литейного сплава, так коэффициент 2,5 рекомендуется при использовании высоколегированных (типа коррозионно-стойких и подобных им) сталей открытой плавки; 4,5 при использовании жаропрочных сплавов вакуумной плавки; 2,25 при использовании алюминиевых сплавов.
.
II группа — отливки средней сложности, состоящие из сочетаний криволинейных и прямолинейных плоскостей с отверстиями и ребрами, а также отливки простые по геометрии, ио тонкостенные с развитой поверхностью.
III группа — сложные отливки, представляющие собой сочетание криволинейных и прямолинейных поверхностей с выступами и углублениями, с виутреииими полостями.
IV группа — особо сложные отливки, с большим числом выступов,углублений, отверстий, тонких стеиок, ребер, а также отливки, представляющие собой сочетание различных фигур, расположенных в разных плоскостях.
В табл. 11.2 приведены данные о трудоемкости основных операций иа пяти заводах с серийным производством. Из этих данных видно, что наибольшие трудовые затраты приходятся иа изготовление и сборку моделей в блоки.
Выход годных отливок и расход основных материалов. Выход годных отливок — это отношение массы годных отливок к массе металлической шихты. Зиая выход годного ( %), определяют расход металла — основного материала. К основным относят те материалы, из которых состоит отливка, Выход годного тем выше, чем проще от-
Основная операция | Заводь! | Расчетная трудоемкость при средней массе отлнвкн 100 г | |||||
А | Б | В | г | Д | |||
Изготовление моделей | 38—41 | 40—42 | 27—35 | 25,2 | 26 | 32 | |
Сборка моделей в блоки | 8,3—11,8 | 2,8— | 9—12 | 12 | 10,4 | 7 | |
3,5 | |||||||
Изготовление оболочки | 8,2—9,9 | 12—14 | 8—11 | 9,5 | 12,5 | 9 | |
формы | |||||||
Формовка и прокалива | 8,2—9,9 | 11—12 | 6,5 -1 | 12 | |||
ние форм | |||||||
Плавка и заливка ме | 3,4—5,6 | 20—21 | 10—11 | 12,8 | 22 | 8 | |
талла | |||||||
Выбивка | 3,2—9,9 • | 4,5 | 4 ) | 1 | |||
Отрезка литниковой си | 8,3—11 | 8,2 | | 9 | ||||
стемы | 21—24 | 30 | 29,1 | ||||
Очистка отливок, ис | 8,4-7,8 | 12,0 j | 22 | ||||
правление дефектов, тер | |||||||
мообработки |
ливка по конфигурации и больше ее масса, выше квалификация работающих в цехе, а также ииже требования, предъявляемые к качеству отливок. На рис. 11.2 приведена зависимость выхода годного для углеродистой стали от сложности отливок. С повышением выхода годных отливок сокращается расход металла, модельных и формовочных материалов, электрической энергии, снижается себестоимость отливок, повышается эффективность использования оборудования и производительность труда. При этом снижаются неизбежные потери металла на угар его при плавке. Чем выше выход годных отливок, тем выше КИМ и КИМо.
Данные о выходе годных отливок служат основанием для расчета расхода металла на единицу отливок. Методы расчета норм расхода металла, КИМ и КИМо приведены в гл. 7.
Расход вспомогательных материалов. К вспомогательным относят те материалы, которые не составляют массу отливок, но необходимы в процессе их изготовления. Модельные и оболочковые материалы — главные из них, так как они составляют 15—18 % себестоимости отливок.
Расход модельных материалов увеличивается со снижением выхода годных отливок, так как возрастают доля ЛПС, количество забракованных отливок и технологические потери оболочек форм. Например, расход модельного состава Р-3 на одну тонну годных отливок, в случае выплавления его из оболочек горячей водой, составляет 68—114 кг при выходе годного 50 % и 86—142 кг при выходе годного 40 %, В гл. 10 приведен метод расчета необходимого коли-
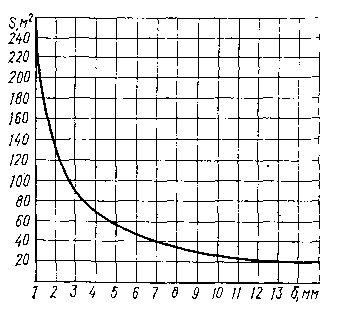
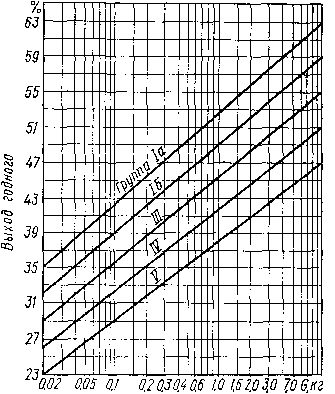
Рнс. 11.2. Выход годных отлнвок в зависимости от их массы G и сложности
чества модельного состава для массового комплексно-механизированного производства автомобильных отливок.
Расход материалов для изготовления оболочек форм увеличивается с увеличением площади поверхности 1 т отливок (рис. 11.3), т. е. чем они более сложны и тонкостенны, а также чем меньше выход годного.
Площадь поверхности отливки (м
) рассчитывают по формуле
где М — масса отливки, кг; р — плотность сплава при 20°С, кг/м
; б — толщина стенки отливки, м, или определяет по графику, показанному на рис. 11.3.
Пример расчета. Расход суспензии (средний) на 1 м
отливок и ЛПС с учетом потерь ее 15 % составляет 6,5—7 кг/м
. Состав суспензии: 26—28 % связующего ЭТС 40 (орг-1 или орг-2), 72—74 % пылевидного кварца кристаллического. Расход обсыпочного материала (по массе) примерно такой же, как суспензии.
Определяем среднюю толщину стенок отливок. Примем, что толщина их б = = 4-г-5 мм, тогда по рис. 11.3 площадь поверхности 1 т отливок S = 60 м
. К этой площади надо прибавить площадь ЛПС. Площадь ЛПС со стояком диаметром 40 мм находим по табл. 11.3; при выходе годного 50 % она составляет ~14 м
на 1т отливок. Тогда суммарная площадь поверхности отливок и ЛПС при выходе годного 50 % будет.
60 + 14 = 74 м
/т.
Расход суспензии на 1 т отливок.
6,5-74= 481 кг/т, в том числе связующего ЭТС (иа 1 т отливок).
481-36/100 я* 173 кг/т.
Масса и площадь поверхности ЛПС со стояком круглого сечения
Размеры, мм, элементов ЛПС | Чи. сло. отлн. вок | Масса,. ЛПС,. кг | Площадь поверхности ЛПС | |||||
Стояк | Воронка | см 2 | м’ на I т отливок, при выходе годных отливок, % | |||||
диа. метр | вы. сота | диаметр. вверху | высота | 50 | 40 | |||
28 | 280 | 50 | 40 | 20 | 1,862 | 345,5 | 19,45 | 29,4 |
32 | 300 | 60 | 50 | 30 | 2,75 | 449,0 | 17,2 | 25,8 |
40 | 300 | 60 | 50 | 30 | 3,918 | 533,5 | 14,16 | 21,49 |
Норма расхода ЭТС 40 при содержаиии в связующем 16 % двуокиси кремния 173-16/40 = 69 кг/т отливок.
Расход электроэнергии (примерный) на технологические нужды приведен в табл. 11.4. Расход установлен для плавки в индукционных печах с кислой и основной футеровкой, для нормализации термообработки отливок и прокаливания форм в методических печах.
.
Таблица 11.4.
Расход электроэнергии
Операция технологического | Расход, кВт-ч, на 1 т | |
процесса | шихты | годных. отлнвок |
Плавка стали: | ||
углеродистой | 580 | — |
коррозионно-стойкой | 630 | — |
Нормализация отливок из стали: | ||
углеродистой | — | 1100 |
кор розионно-стой кой | — | 1800 |
Прокаливание оболочковых форм (в опорном наполнителе) | — | 1860 |
Сушка материалов | — | 450 |
Известны следующие способы снижения расхода электроэнергии: подогрев шихты газовыми горелками перед плавкой, прокаливание об-лочковых форм в газовых печах вместо электрических; применение материала основы оболочки с малым термическим расширением, например порошков непрозрачного кварцевого стекла.
Себестоимость. В качестве обобщающего измерителя работы и конечных результатов в настоящее время выступает себестоимость отливок-.
Себестоимость прямо связана с трудоемкостью, которая тем выше, чем меньше масса отливок и чем они сложнее. С увеличением объема производства и степени механизации технологического процесса трудоемкость и себестоимость^изготовления отливок уменьшаются,.
однако соотношения между себестоимостью (руб.) и трудоемкостью непостоянны, так как различны и темпы их изменений.
Себестоимость включает заработную плату основных рабочих, приходящуюся на 1 т отливок, стоимость потребляемых материалов и электроэнергии, расходы на оснастку (по статье специальные расходы), цеховые расходы и потери от брака.
Для улучшения и облегчения контроля за выполнением нормативов по расходу материалов и электроэнергии и применения в отрасли норматива чистой продукции, целесообразно использовать структуру себестоимости, показанную в табл. 11.5, выделив лимит (в процентах) на оплату вспомогательных материалов и электроэнергии в отдельные статьи.
Таблица 11.5.
Типовая калькуляция себестоимости, руб., на 1 т отливок из углеродистой и низколегированной стали
Лнмнт, | Отливки | ||||
Статья | себестои. мости | простые | средней. слож. ности | сложные | особо. сложные |
Основные материалы | 6 | 45,2 | 51,0 | 62,1 | 69,0 |
Вспомогательные материалы | 20 | 151,0 | 170,0 | 207,0 | 230,0 |
Заработная плата основных рабочих | 15 | 113,8 | 127,5 | 155,25 | 172,5 |
Заработная плата вспомогательных рабочих | 15 | 113,0 | 127,5 | 155,25 | 172,5 |
Отчисления иа социальное страхование | 2 | 15,1 | 17,0 | 20,7 | 23,0 |
Электроэнергия | 16 | 120,5 | 136,0 | 165,6 | 184,0 |
Специальные расходы | 5 | 34,0 | 42,5 | 51,75 | 57,5 |
Цеховые расходы | 19 | 144,3 | 161,5 | 196,65 | 218,5 |
Потери от брака | 2 | 15,1 | 17,0 | 20,7 | 23,0 |
Себестоимость | 100 | 755,0 | 850,0 | 1035,0 | 1150,0 |
Себестоимость, расчитанная по табл. 11.5, соответствует действительности только при условии, что затраты на материалы, электроэнергию и по другим статьям калькуляции, кроме оплаты живого труда, постоянно составляют одинаковую часть себестоимости. Из этого следует, что снижение себестоимости отливок — конечную цель производства — надо искать в совершенствовании технологии и организации производства.
Специальные расходы. К специальным расходам относят стоимость изготовления и доводки пресс-форм, металлических стояков-каркасов и подобной оснастки. С уменьшением серии отливок расходы на изготовление пресс-формы, отнесение на одну отливку, возрастают как по абсолютному значению, так и в процентах по отношению к общим затратам на ее изготовление. С укрупнением серии отливок экономичней использовать более совершенную оснастку, хотя и дорогую (табл. 11.6).
Серия. выпу. скаемых. отлнвок,. шт. | Пресс-форма | Трудоем. кость. изгото. вления. пресс-. формы,. мнн | Затраты времени на одну модель, мнн | Продол. житель. ность. изгото. вления. одной. модели,. мнн | Суммарная трудоемкость на одну модель, мнн |
500 | Одногнездная из легкоплав | 4 800 | 9,6 | 2 | п,б |
5 000 | кого сплава. Шестигнездная из легкоплав | 10 800 | 2,17 | 2 | 2,5 |
100 000 | кого сплава. Шестигнездная из стали | 21 000 | 0,21 | 0,75 | 0,34 |
Примечание. Способ удаления моделей — выплавление.
Пример влияния механизации технологического процесса на трудоемкость изготовления и себестоимость отливок приведен в табл. 11.7.
Таблица 11.7.
Примерная трудоемкость изготовления 1 кг отливок
Отлнвкн | Процесс изготовления отлнвок | Трудо-. емкость,. чел.-ч |
Средней сложности массой до 1,6 кг из стали: | ||
углеродистой | Механизированный | 0,5 |
Ручной | 1,2 | |
коррозионно-стойкой | » | 3,0 |
жаропрочной | » | 4,2 |
Сложные массой до 1,6 кг из стали: | ||
углеродистой | Механизированный | 0,55 |
Ручной | 1,5 | |
коррозиоиио-стой кой | » | 6,6 |
При механизированном процессе изготовления отливок степень их сложности не оказывает существенного влияния на затраты труда, тогда как при ручном изготовлении сложных отливок эти затраты на 1 кг отливок значительны.
Цеховые расходы после выделения из них заработной платы вспомогательных рабочих и ИТР, стоимости вспомогательных материалов и электроэнергии составляют почти пятую часть себестоимости отливок. Оставшиеся в их составе затраты на обслуживание бытовых помещений, транспортные расходы, амортизацию зданий и инвентаря, выплату за услуги других цехов, за простои и другие в значительной мере зависят от организации хозяйственной деятельности и могут быть сокращены до 12—15 % вместо 19 %, предусмотренных.
в проекте типовой калькуляции (см. табл. 11.5). Следует отметить, что такое сокращение является нормой на многих заводах. Вопрос о сокращении потерь от брака в связи с задачей повышения качества отливок и эффективности производства имеет не только экономическое, но и социальное значение.
Расчет экономической эффективности от внедрения новой техники выполняют, сравнивая исходные показатели по себестоимости и затратам внедрения, с последующим умножением результатов сравнения на годовой объем производства по формуле
где С
и С„ — себестоимости единицы отливок до внедрения новой техники и после внедрения, руб.; К
и К
— удельные капитальные затраты на единицу до внедрения новой техники и после внедрения, руб.; Е — нормативный коэффициент, Е = 0,15; А
— объем производства отливок в год после внедрения новой техники, т (или в других единицах).
Срок окупаемости дополнительных капитальных затрат в годах определяют как отношение разности удельных капитальных затрат к разности себестоимостей по формуле
Требуется электролитического никеля (99,8% Ni; 0,1 С; сумма примесей 0,6%) 38,0—22,56 = 15,44 кг (принимая 100 % Ni).
Расчет содержания Si. Требуемое содержание в отливках 2,5 % Si (У =15)
Вносится Si в шихту с возвратом [2,3-120/100] = 2,76 кг. Следует ввести Si в шихту с ферросилицием 5,88—2,76= 3,12 кг. Требуется ферросилиция (76,5% Si; сумма примесей 1,2 %) 3,12-100/76,5 = 4,07 кг.
Расчет содержания Мп. Требуемое содержание в отливках 1 % Мп.
(У =
Вносится Мп в шихту с возвратом [0,8-120/100] = 0,96 кг. Следует ввести Мп в шихту с ферромарганцем 3,4—0,96 == 2,44 кг. Требуется ферромарганца (82,0 % Мп; 1,2% С; сумма примесей 2,6%) 2,44-100/82 — 3,0 кг.
Расчет содержания Fe. Железо является основным компонентом сплава, содержание его должно быть 52,35 (у = 2)
Вносится Fe в шихту с возвратом 52,0-120/100 = 62,4 кг (по разности в химическом составе возврата). Вносится Fe в шихту с ферросплавами 12,7 кг. Следует ввести Fe шихту с низкоуглеродистой сталью
Требуется низкоуглеродистой стали (98,5% Fe; 0,1 % С; сумма примесей 1,4%)
Расчет содержания С. Требуемое содержание в отливках 0,15 % С («=10)

Вносится в шихту: с возвратом 0,17-120/100 = 0,204 кг, с низкоуглеродистой сталью 0,032 кг, с ферросплавами 0,088 кг,

Тпебуется дополнительно ввести С в шихту:

(16 г углерода в виде дробленого боя графитовых электродов).
Далее рассчитанный состав шихты следует проверить на допустимое содержание вредных примесей S и Р. Допускается S — 0,03 %, или 0,06 кг; Р — 0,035 %, или 0,07 кг. Вносится в шихту (для S и Р, у = 0): с возвратом 0,02-120/100 = 0,024 кг S и 0,024 кг Р (по 0,02 %); с низкоуглеродистой сталью 0,009 кг S и 0,009 кг Р (по 0,03%); с ферросплавами 0,011 кг S и 0,013 кг Р (0,03 % S; 0,03—0,3 % Р).
Содержание серы: 0,024 + 0,009+ 0,011 = 0,044 кг или 0,022 % S
< 0,03 % .
Содержание фосфора: 0,024+ 0,009+ 0,013 = 0,046 кг или 0,023 % Р
< .
Расчетное содержание S и Р в шихте меньше допустимого предела.
Если проведенные проверки по содержанию углерода, серы и фосфора в шихте показывают повышенное их содержание, то следует применять для шихты сталь с меньшим содержанием углерода и ферросплавы с меньшим содержанием примесей.
Весьма незначительным количеством углерода (0,16 г в приведенном примере), необходимого для подшихтовки, в практической работе можно пренебречь, так как это составляет менее 0,01 % и значительно меньше возможных ошибок при взвешивании шихты.