Наиболее простым методом анализа структуры является рассмотрение изломов металла с помощью луп.
Для исследования макроструктуры отливку следует подготовить: очистить, разрезать по контролируемому сечению, иногда механически обработать до требуемой чистоты и протравить для отчетливого выявления макрозерен.
Макроструктуры отливок лопаток автомобильного двигателя из железоникелевого сплава представлены на рис. 9.6. При литье по выплавляемым моделям величина зерна зависит от температуры металла и формы. Например, металл или форма при заливке лопатки, показанной на рис. 9.6, слева имела меньшую температуру, чем для лопатки, показанной справа.
Исследования микроструктуры проводят на полированных травленых шлифах, вырезанных из отливки. Структуры сплава исследуют с помощью оптических микроскопов МИМ-7, МИМ-8 и других при увеличении до 2000. На практикё чаще всего пользуются увеличением в 100—500 раз.
Электронные микроскопы, разрешающая способность которых в десятки раз выше, чем оптических, вследствие меньшей длины волны электронного излучения, позволяют исследовать микроструктуры с увеличением в 10—40 тыс. раз и более. Уже применяют микроскопы, на которых достигают увеличения в 500 тыс. раз. При этом можно вести исследования на уровне величин нескольких атомных радиусов (до 0,9 нм).
Рис. 9.6. Макроструктура литых рабочих_лопаток турбии из железохромиикелевого сплава.
.
На рис. 9.7 приведена для примера микроструктура рабочего колеса турбокомпрессора дизельного двигателя из никельхромового жаропрочного сплава типа Ineo 717С. При увеличении в ЮОЗраз (рис. 9.7, а) хорошо видны границы зерен сплава с цепочкой упроч-
Рис. 9.7. Микроструктура литого рабочего колеса турбокомпрессора дизельного двигателя из сплава Inco 717С: а — XI00; б — Х400
Рис. 9.8. Электронные микрофотографии шлифов, вырезанных из турбинных лопаток:.
а — сплав АНВ-300 (0,08 % С); б — сплав АНВ-300У (0,30 % С), Х5000.
.
няющих мелких карбидов хрома. При увеличении в 400 раз (рис. 9.7, б) выявлена основная упрочняющая интерметаллидная ^-фаза на основе соединения Ni
(Ti, А1) и карбидная сетка по границам зерен. По границам зерен также располагаются карбиды титана (светлые включения).
На рис. 9.8 приведены микроструктуры турбинных лопаток автомобильных двигателей из сплавов АНВ-300 и АНВ-300У, отличающихся различным содержанием углерода. Повышение содержания с 0,1 до 0,35 % С позволило повысить жаропрочность сплава на 30 % при совместном интерметаллидном и карбидном упрочнении. На электронной микрофотографии отчетливо видно благоприятное измельчение интерметаллидной фазы с повышением концентрации углерода в сплаве.
Для более точной расшифровки сплава по содержанию отдельных фаз, выявления их химического состава применяют рентгеноструктур* ный анализ. Он основан на свойстве строго определенных для данной фазы кристаллических решеток отражать под определенными углами, в зависимости от расположения кристаллических плоскостей, рентгеновские лучи. Результат рентгеноструктурного анализа — характер отражения рентгеновских лучей от кристаллических плоскостей — фиксируется на фотопленке в виде дебаеграммы, на которой получаются изображения, аналогичные поверхностям, проведенным через группы атомов определенной кристаллической решетки. С помощью имеющихся формул и таблиц специалист идентифицирует кристаллическую решетку соединения металлической или интерметаллидной фазы. ■.
Реактивы для травления образцов при исследованиях макро- и микроструктур приведены р специальной литературе по металлографии,.
Контроль отливок на отсутствие трещин. Трещины в отливках иногда бывают исчезающе малыми, незаметными при визуальном контроле. При контроле внутренних дефектов рентгенопросвечива-нием трещины также трудно выявить из-за большой массы просвечиваемого металла.
Для выявления трещин в отливках используют специальные методы контроля: магнитный, люминесцентный и цветной дефектоскопии.
Магнитный контроль применим для сталей и сплавов, обладающих магнитными свойствами. Принцип магнитной дефектоскопии основан на том, что в намагниченной отливке трещины искажают магнитное поле и силовые линии концентрируются по границам трещин. Намагниченную с помощью магнитного дефектоскопа отливку погружают в суспензию с магнитным порошком, который концентрируется и удерживается на границах трещины, делая ее видимой.
Для обнаружения трещин отливку намагничивают так, чтобы силовые линии магнитного поля пересекали дефект под прямым углом Поэтому для выявления поперечных трещин применяют намагничивание отливки продольным магнитным полем, а для выявления косорасположенных трещин — циркулярное намагничивание. Для выявления трещин любого направления используют комбинированное намагничивание. Перед испытанием отливку обезжиривают. Для обнаружения трещин на фоне отливки применяют чувствительные ферромагнитные черные порошки из магнитной окиси железа.
Люминесцентный или флюоресцентный способ выявления дефектов применим ко всем материалам в тех случаях, когда дефекты выходят на поверхность, в том числе и для немагнитных сплавов.
Флюоресценция — свойство вещества поглощать свет одной длины волны и превращать его в свет другой длины волны. Для дефекте* скопни используют невидимый глазом ультрафиолетовый («черный») свет, под действием которого флюоресцирующая жидкость ярко светится.
Предварительно очищенные и обезжиренные отливки погружают на 10—20 мин в ванну с флюоресцирующей жидкостью. Под действием Капиллярных сил жидкость проникает в трещины или другие дефекты. Излишек жидкости, оставшейся на поверхности отливки, смывают водой. В дефектах жидкость задерживается. 3атем «проявляют» дефекты, дЯя чего отливки опыляют порошком, адсорбирующим жидкость при выдержке 5—10 мин./Порошок не флюоресцирует, НО способствует лучшему выявлению дефектовЛПокрывая поверхность отливки тонким ровным слоем, порошоКГасит флюоресценцию жидкости, оставшейся частично не смытой с поверхности и тем самым уменьшает фон. В местах расположения дефектов порошок впитывает жидкость, вытягивает ее на поверхность. После этого отливки облучают ультрафиолетовым светом. Жидкость, вытянутая порошком на новерхность, флюоресцирует, обрисовывая дефекты в внде ярких, легко видимых глазом светящихся лщщй.
Обычно используют флюоресцирующую жидкость состава: 85,7 % очищенной нефти, 9,3 % олеиновой кислоты и 5 % триэтаноламина. Проявителем служат сухие тонкие порошки окиси магния, углекислого магния, мела, талька, пылевидного кварца. В качестве источника ультрафиолетового излучения используют ртутно-кварцевые лампы ПРК.-4 или ПРК.-2 с приборами включения. Светофильтром для получения «черного света» служит увиолевое стекло. Это стекло пропускает ультрафиолетовый и близкий к нему фиолетовый участки спектра, остальная часть спектра стеклом задерживается.
Сущность метода цветной дефектоскопии заключается в том, что отливку смазывают легкоподвижной краской, способной проникать в мельчайшие дефекты. Затем краску с поверхности смывают и отливку вновь смачивают другой краской — фоном, обладающей поглотительной способностью. На фоне из дефектов выступает ранее нанесенная краска, обозначая тем самым места расположения дефектов.
В состав легкоподвижной краски входит 10 г жирорастворимого темно-красного красителя «судан IV» на 1 л раствора, состоящего из масла МК.-8 и бензола; поглощающая белая краска состоит из 700 см
коллодия, 100 см
ацетона, 200 см
бензола и 50 г густотертых цинковых белил на 1 л жидких составляющих.
Отливки обезжиривают ацетоном, протирают чистой ветошью, просушивают в сушильном шкафу; затем их окунают в красную краску 2—3 раза с интервалом 2—3 мин. Можно наносить краску пульверизатором или кистью. После выдержки (2—3 мин) красную краску с поверхности отливки снимают ветошью, смоченной смесью керосина и трансформаторного масла (70 : 30). На отливку быстро (окунанием или кистью) наносят белую краску ровным тонким слоем. После подсушивания краски осматривают дефекты. Трещины выявляются четкими красными линиями на белом или розоватом- фоне. Раковины и поры— красными точками. Более глубоким дефектам соответствует более яркай красная окраска.
При цветной дефектоскопии необходимо работать с вытйжной вентиляцией и соблюдать меры противопожарной безопасности, так как применяемые материалы токсичны и огнеопас^цл.
Контроль внутренних дефектов в отливках. Внутренние дефекты отливок могут быть выявлены при просвечиваний Отливок рентгеновскими лучамн.
...
Проходя через металл отливки, благодаря малой длине волны (0,ЗГ—0,0006 нм) рентгеновские Лучи частично пронизывают металл, а частично отражаются многочисленными поверхностями металлических кристаллов, создавая рассеянное вторичное рентгеновское излучение. Интенсивность поглощения рентгеновских лучей металлом зависит от плотности элемента и от его места в периодической системе элементов Д. И. Менделеева (от атомного номера). Чем больше атомной номер просвечиваемого элемента, тем больше он поглощает рентгеновских лучей. Рентгеновские лучи также обладают свойством оказывать химическое действие, Что используют в процессе дефэктО-екопии для получения рентгеновского снимка на фотографической.
Рис. 9.9. Схема просвечивания отливки:.
1 — рентгеновская трубка; 2 — бленда; 3 — лучн; 4 — свинцовая диафрагма; 5 — отливка; 6 — защитные свинцовые листы; 7 — кассета с фотопленкой
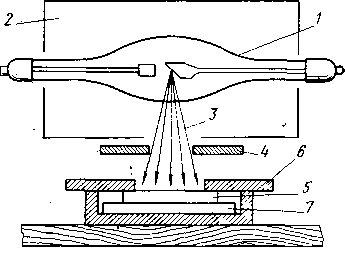
пленке. Поглощенная энергия рентгеновских лучей вызывает появление «скрытого изобрже-ния» вследствие изменений находящегося в эмульсии бромистого серебра и превращения его в металлическое.
Наиболее распространен фотографический метод рентгено-дефектоскопии (рис. 9.9). На пути рентгеновских лучей выходящих из фокуса анода рентгеновской трубки, устанавливают отливку, а за ней фотографическую пленку в кассете или черной светонепроницаемой бумаге, но хорошо проницаемой для рентгеновских лучей. Если на пути лучей встретятся пустоты в отливке (раковины, рыхлоты), то проекция этих мест на фотопленке будет более темной.
Не только пустоты, но и ликвация в отливках, когда в общей металлической массе встречаются более или менее плотные участки с иным химическим составом, хорошо выявляются при рентгенодефек-тоскопии в виде более темных или более светлых^ участков на негативе.
Контрастность и четкость негативов важны для правильной оценки дефектов. Они зависят от длины волны рентгеновского излучения, величины рассеянного излучения, фокуса трубки, расстояния до пленки и применяемой фототехники.
Для предотвращения рассеяния излучения, снижающего контрастность снимка, применяют диафрагмы, экраны и фильтры из свинца. Помещая их в виде фольги между отливкой и пленкой, можно ослабить эффект рассеяния, так как часть излучения поглощается фольгой.
Фототехника, применяемая в рентгенодефектоскопии, описана в специальной литературе.
Стопроцентному рентгеновскому контролю подвергают отливки наиболее ответственного назначения, когда поломка детали может вызвать опасность для здоровья и жизни людей. В менее Ответственных случаях проводят выборочный рентгеноконтроль,.
Рентгенодефектоскопию можно использовать при отработке ЛПС, для выбора оптимальных размеров прибылей. Например, при литье сопловых лопаток тяговой турбины автомобильного газотурбинного двигателя вначале применили цилиндрический стояк (рис. 9.10, а). В изломе отлитых лопаток была обнаружена усадочная рыхлота. С помощью рентгенодефектоскопии выявили, что в случае, когда лопатки расположены широкой частью пера вниз, условия кристаллизации отливок н питания их расплавом неудовлетворительны..
Рис.9.10.
В пере образуется крупная сосредоточенная усадочная рыхлота, отчетливо видимая на позитиве рентгеновской пленки (рис. 9.10, г). Применение литниковой системы с кольцевым коллектором (рис.
9.10, б) при той же ориентации лопаток — широкой частью пера вниз — изменило характер дефекта. Питание лопаток улучшилось, но из-за несоблюдения принципа направленного затвердевания усадочные дефекты в лопатках остались в виде рассредоточенных рыхлот (рис. 9.10, 5). Только при расположении лопаток широкой частью пера к коллектору (рис. 9.10, в), когда было обеспечено направленное затвердевание отливок, они были получены годными, без усадочных рыхлот (рис. 9.10, е).
Контроль ультразвуком основан на регистрации донного эффекта импульса ультразвукового генератора. Ультразвуковые волны с частотой 20—10 МГц распространяются в однородном металле отливки прямолинейно и отражаются от поверхностей различных дефектов (трещин, раковин). С помощью осциллографа определяют место расположения дефекта. Этим методом проверяют в основном простые по конфигурации отливки. Ультразвуковой контроль является одним из наиболее простых методов выявления внутренних дефектов без разрушения отливок и по мере его совершенствования найдет более широкое применение.
Контроль герметичности отливок. Простейшее испытание — проба керосином, который наливают в отливку. Керосин подвижная жидкость, хорошо проникает в рыхлоты, трещины, раковины отливки. При. сквозных дефектах, через несколько часов на поверхности отливки появляется темное пятно просочившегося керосина. Не все отливки можно испытывать этим способом, для отливок с большим числом отйерстий и окон.он не пригоден.
Герметичность отливки можно проверить также под давлением. Для этого все отверстия в отливке закрывают пробками или заглушками с резиновыми прокладками, В одной из заглушек предусматривают штуцер, соединяемый с шлангом для подачи в отливку воды или воздуха под заданным давлением с помощью насоса или компрессора. Для лучшего выявления дефектов отливку следует погрузить в воду или покрыть снаружи мыльной водой, тогда в месте дефекта при утечке воздуха образуются мыльные пузыри. Проверка сжатым воздухом более опасна, чем водой, и ее следует вести с соблюдением всех мер безопасности, преимущественно при низком давлении. При проверке герметичности водой избыточное давление может достичь нескольких десятков мегапаскаль.