Жаростойкие (окалиностойкие)"стали и сплавы характеризуются высокой химической стойкостью к окислению при высокой температуре [17]. Сопротивление окислению при высоких температурах зависит от химического состава сталей и сплавов, стойкости образующихся на их поверхности окисных пленок и состава газовой среды, в которой происходит окисление. Жаростойкие стали и сплавы близки по основным составляющим к коррозионно-стойким сталям, но содержат большее количество легирующих элементов и имеют более сложный фазовый состав. С увеличением содержания хрома повышается окалиностойкость сталей.
Стали, содержащие 10—13 % Сг, имеют хорошую жаростойкость до температуры 750 °С; содержащие 15—18 % Сг — до 900 С°; содержащие 22—25 % Сг — до 1100 °С. Присадка к хромистым и хромоникелевым сталям и сплавам алюминия, кремния и небольшого количества титана, ниобия, бериллия, еще больше повышает жаростойкость.
Повышению жаростойкости способствует образование на поверхности металлов и сплавов тугоплавких, плотных окисных пленок в результате соединения хрома, никеля, алюминия, кремния с кислородом. Эти пленки плотно прикрывают поверхность сплава и препятствуют двусторонней диффузии атомов кислорода и металла (см. табл. 2.4).
Жаропрочные стали и сплавы (см. табл. 2.5) отличаются свойством противостоять пластической деформации под воздействием напряжений при высокой температуре [99].
На жаропрочность большое влияние оказывает природа твердого раствора основы сплава, ее температура плавления и тип кристаллической решетки. Чем выше температура плавления основы, тем выше жаропрочность сплава. Сплавы аустенитного типа на основе железа
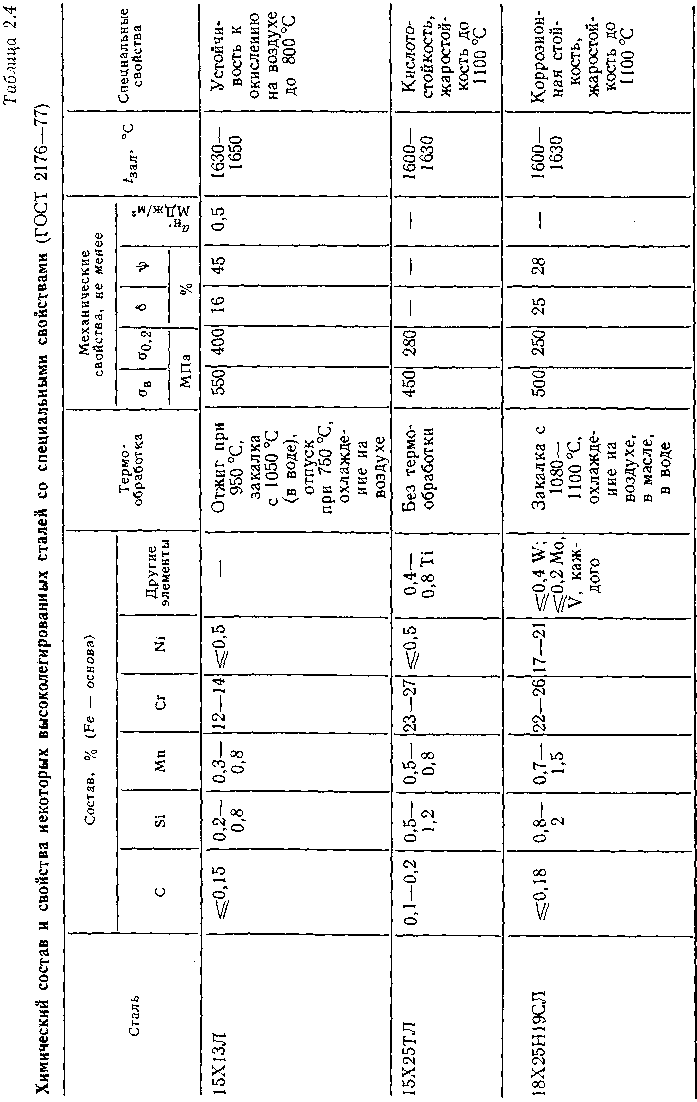
Примечания. 1. Во всех указанных сталях допускается содержание до 0,3 % Си.
2.
В стали 15Х13Л должно быть % Р; в сталях 08Х14Н7МЛ н 16Х18Н12С4ТЮЛ должно быть .
во всех остальных сталях —
< 0,3S и 0,35Р.
3.
У сталей указанных марок свободная линейная усадка 1,7—2,5 %, удовлетворительные жндкотекучесть, свариваемость, хорошая».
обрабатываемость резанием.
Состав, % | Термо. обра. ботка | ||||||||
Сплав | Fe | Ni | С | Сг | Si | Мп | Другие. элементы | ||
20Х26Н19С2Л | Основа | 18 — 20 | 23 — 27 | 2-3 | 0,5-. 1,5 | Закалка с 1100 °С, охлаждение в воде | |||
40Х9С2Л | Основа | 0,35 — 0,5 | 8—10 | 2 — 3 | 0,3 — 0,7 | Без термообработки | |||
20X21 Н46В8Л | Осталь. ное | 43 — 48 | 0,1—0,25 | 19 — 22 | 0,2-. 0,8 | 0,3-. 0,8 | 7 — 9 W; | Старение при 900 °С, выдержка 5 ч, охлаждение на воздухе | |
жсз-дк | Осталь. ное | 0,07 — 0,12 | 11 — 14 | 2,8 Ti;. 4.5 А1;. 4.5 Мо;. 4.5 W; 8 Со;. 0,02 В, 0,02 Се (по расчету) | Закалка с 1215 °С, выдержка 4 ч, охлаждение на воздухе | ||||
ЖС6-К | Осталь. ное | 0,13 — 0,2 | 9,5-. 12 | 0,4 | 0,4 | 3 Ti;. 5 А1;. 4 Мо;. 5 W;. 5 Со. 0,02В; 0,015 Се (по расчету) | Закалка с 1220 °С, выдержка 4 ч, охлаждение на воздухе | ||
АНВ300 | Осталь. ное | 14 — 17 | 1,4—2 Ti, 7,0-10 W, 4,5 — 5,5 А1 | Закалка с 1120 °С, выдержка 10 ч, охлаждение иа воздухе |
Примечания. 1.В сплавах АНВ300У, ЖС6-К. ЖСЗ-ДК содержится: 8. Для сплавов плотность
Механические свойства, ие менее | **зал* | Лннейная свободная усадка, % | Специальные. свойства,. назначение | |||||||
t испытаний, °С | а в | а 0,2 | а 100 | 6 | S. l4 | |||||
МПа | % | |||||||||
20 | 500 | 250 | - | 25 | 28 | - | 1600—1620 | 2,5 | Жаростойкость до 1100°С. Сопловые лопатки ГТД | |
Не нормируются | 1560 — 1600 | 2,3 | Жаростойкость до 800 °С. Жаропрочность до 700 °С. Сопловые венцы турбокомпрессоров | |||||||
20 | 450 | 6 | 8 | 1600 — 1620 | 2,4 | Жаростойкость до 1000 °С. Жаропрочность до 800 °С. Детали двигателей и газовых турбин (рабочие и сопловые лопатки и др.) | ||||
20. 900 | 900. 700 | 800. 500 | 290 | 5. 6 | 8. 8 | 0,3 | 1560 — 1620 (в вакууме) | 2,3 | Жаростойкость до 1100 °С, жаропрочность до 1000 °С. Рабочие турбинные колеса ГТД | |
20. 900 | 900. 800 | 830. 500 | 320 | 1,7. 5 | 6. 8 | 0,1 | 1580 — 1650 (в вакууме) | 2,3 | Жаростойкость до 1100 °С. Жаропрочность до 1000 °С. Рабочие сопловые лопатки и колеса ГТД | |
20 850 | 950. 700 | - | 240 | 1. 1,8 | 3. 1,5 | — | 1540-1600 (в вакууме) | 2,3 | Жаростойкость до 1000 °С. Жаропрочность до 950 °С. Рабочие и сопловые лопатки ГТД небольшой мощности |
с гранедентрированной решеткой имеют большую жаропрочность, чем сплавы ферритного типа с объемноцентрированной решеткой.
Повышению жаропрочных и других свойств сталей и сплавов способствует также легирование. Наибольший эффект достигается при одновременном легировании многими элементами. Введение таких элементов, как алюминий, титан, вольфрам, молибден, ниобий, бор, сильно увеличивает сопротивление сплавов пластической деформации при высоких температурах вследствие образования высокодисперсных интерметаллидных фаз и блокировки плоскостей скольжения при выделении этих фаз из твердого раствора. Кроме того, присутствие этих элементов в твердом растворе задерживает диффузионные процессы, и сплав при высоких температурах не разупрочняется.
При введении большого количества легирующих элементов в сплавы наряду с повышением их жаропрочности снижается пластичность и ухудшается их ковкость. Поэтому наиболее жаропрочны литые сложнолегированные сплавы с гетерогенной структурой. Так как такие сплавы имеют высокую твердость, вязкость и трудно обрабатываются, применение литья по выплавляемым моделям является более целесообразным методом для изготовления деталей сложной формы, например лопаток турбин и соплового венца, крыльчаток, рабочих колес и лопаток турбокомпрессоров.
Свойства жаропрочных сплавов зависят от чистоты шихтовых материалов, применяемых при плавке, и методов рафинирования. Сера из шихты, при повышенном ее содержании, вступая в соединение с никелем, образует легкоплавкую эвтектику (температура плавления 645 °С), которая располагается по границам зерен, в результате чего снижается жаропрочность сплава. Еще в большей степени снижаются жаропрочные свойства сплавов при загрязнении их легкоплавкими примесями (висмут, свинец, сурьма и др.), попадающими из шихты. Поэтому шихту тщательно проверяют, а расплав в процессе плавки рафинируют [36, 87].
Жаропрочность крупнозернистых сталей и сплавов более высокая, чем мелкозернистых. Для литых деталей из жаропрочных сплавов характерна крупнозернистость.
Сплавы принято считать жаростойкими, если при данной температуре за 100 ч испытаний в воздушной среде увеличение массы образцов вследствие образования окалины не превышает 1 г/см
в 1 ч.-Сплавы считают жаропрочными, если при данной температуре за заданный срок испытаний они сохраняют требуемый уровень прочности. Жаропрочные и жаростойкие стали и сплавы большей частью обладают также термостойкостью, т. е. стойкостью к воздействию нагрузки в условиях частой смены температур (нагрев — охлаждение).
Магнитными называют сплавы, обладающие магнитными свойствами: магнитной проницаемостью и восприимчивостью, остаточной индукцией и коэрцитивной силой. Магнитная проницаемость характеризует свойство сплава пропускать магнитный поток. Магнитная восприимчивость характеризует способность сплава к намагничи-.
Химическиб состав некоторых литейных магнитных сплавов (ГОСТ 17809—72)
Сплав | Состав (основные компоненты), % (Fe — остальное) | ||||
А1 | N1 | Си | Со | Другие. элементы | |
ЮНД4 | 13-14 | 24—25 | 3—4 | 0,2—0,3 Ti | |
ЮНТС | 13—16 | 32—35 | — | — | 1—1,5 Si, 0,4—0,5 Ti |
ЮНДК15 | 8,5—9,5 | 19—20 | 3—4 | 14—15 | 0,2—0,3 Ti |
ЮНДК18 | 9—10 | 18—19 | 3—4 | 18—19 | — |
ЮН14ДК24 | 7,5—8,5 | 13,5—14,5 | 2,5—3,5 | 23,5—24,5 | — |
ЮНДКЭ1ТЗБА | 6,8—7,2 | 13—13,5 | 3—3,5 | 30,5—31,5 | 3—3,5 Ti 0,9—1,5 Nb |
ЮНДК40Т8АА | 7,2—7,7 | 14—14,5 | 3—4 | 39—40 | 7-8 Ti |
Примечание. В обозначении марок сплавов буквы в конце марки означают: А — столбчатая кристаллическая структура; АА — монокристаллическая структура.
ванию. Остаточная индукция характеризует степень остаточной намагниченности сплава после снятия магнитного поля. Коэрцитивная сила представляет собой значение напряженности магнитного поля, необходимого для того, чтобы свести к нулю остаточную намагниченность в магнитных сплавах. Химический состав магнитных сплавов, применяемых при литье по выплавляемым моделям, приведен в табл. 2.6.