Модельные составы могут быть классифицированы по ряду признаков, например, в зависимости от природы и количественного соотношения образующих их компонентов, свойств, методов изготовления моделей, способа удаления последних из форм. Наиболее существенным является первый классификационный признак, так как природа и соотношение компонентов модельного состава определяют его физико-механические, химические и технологические свойства, следовательно и рациональные методы использования.
По указанному признаку модельные составы разделены В. А. Озеровым на семь групп (табл. 5.1).
Группа 1 — воскообразные составы, используемые для изготовления моделей как из расплавов, так и из паст. Эти составы наиболее универсальны и широко распространены как в СССР, так и за рубежом. Их главные компоненты — парафины, натуральный и синтетический церезин, стеарин, буроугольный или горный (монтановый) и торфяной воски (битумы), сложные эфиры высших кислот, в отдельных случаях (в настоящее время редко, преимущественно в зарубежной практике) — натуральные воски; пчелиный, кандилльский, карнаубский.
Груп. па | Наименование | Примеры составов * |
1 | Воскообразные выплавляемые составы | ПС 50-50; ПСЭ 70-25-5; ПЦБКо 70-12-13-5 (Р-3); ПЦПэв 62-25-13 (МВС-ЗА); ПБПсм 60-25-15 (ИПЛ-2); ПБТТэ 25-35-35-5 (ВИАМ-102) |
2 | Составы на основе натуральных и синтетических смол с добавками воскообразных и других компонентов | КПсЦ 50-30-20; КЦПэБн 80-18-1,6-0,4 (МАИ-Зш) |
3 | Водорастворимые составы | КбБк 98-2; КбНк 90—10 (МОН-ЮК); КбПвсМс 95,5-2-2,5 (МПВС) |
4 | Термопласты компактные и вспенивающиеся, удаляемые из оболочек форм выжиганием | Полистирол блочный, полистирол суспензионный, вспенивающийся (например, ПСВ-ЛД) |
5 | Легкоплавкие металлы и сплавы | Ртуть, амальгамы ртути (в практике отечественного производства не применяются) |
6 | Модельные составы, представляющие собой смеси или сплавы составов различных групп | MB (мочевинно-восковой состав, например, смесь расплавов карбамида и состава ПБТТэ 50-25-20-5) |
7 | Выплавляемые составы с твердыми наполнителями | РМ (сме |
* В скобках указаны условные наименования (торговые марки), ие несущие информацию о компонентах состава. Например, «ИПЛ» означает Институт проблем литья, где состав был создай.
В качестве добавок, улучшающих реологические свойства составов, повышающих их прочность и теплостойкость, снижающих хрупкость, используют такие продукты, как, например, кубовый остаток горячего крекинга парафина, касторовое масло, триэтанола-мин, пластичную смазку, сибирский воск, этилцеллюлозу, канифоль, а также полиэтилен.
В начальной стадии промышленного применения процесса литья по выплавляемым моделям в СССР широко использовали парафиностеариновые составы ПС 50-50, ПС 70-30, ПСКм 65-32-3,.
ПСЭ 70-25-5 *, обладающие хорошими реологическими свойствами в пастообразном состоянии и пригодные для изготовления моделей как на машинах, так и с помощью ручных (шприцев. Однако ввиду ряда существенных недостатков (малой прочности и теплостойкости; наличия дорогого, дефицитного стеарина, склонного к взаимодействию с растворителями этилсиликатных связующих и омылению в горячей воде) эти легкоплавкие составы были позже в большдагстве цехов заменены более экономичными бесстеариновыми, применение которых обеспечивало получение более прочных и теплостойких (следовательно, более точных) моделей, невзаимодействующих со связующими суспензии и водой при выплавлении из оболочек форм. Наиболее распространенными из второго поколения воскообразных модельных составов являются ПЦБКо 70-12*13-5, ПБПсм 60-25-15, ПБТТэ 25-35-35-5 [41 ].
В последние годы созданы и получили промышленное применение воскообразные составы третьего поколения, особенность которых заключается в том, что в них помимо парафина и других перечисленных выше главных компонентов вводят синтетические полимеры, например, полиэтиленовые воски ПВ-200 и ПВ-300, улучшающие свойства составов, в основном их теплоустойчивость и прочность. К таким составам относятся МВС-ЗА, МВС-15, ППК.-1- Свойства наиболее распространенных составов группы 1 приведены в табл. 5.2. Составы Р-3, ИПЛ-2, МВС-ЗА, ВИАМ-102, ПЦБ 62-25-13 выпускают централизованно [46, 54, 74].
Воскообразные составы из буроугольного воска (до 55 % по массе) и церезина (15—45 %) с добавкой 7—12 % канифоли широко используют в ГДР и ЧССР. Для улучшения технологических свойств в эти составы добавляют синтетические воски, неочищенный парафин, стеарин.
Воскообразные составы различного назначения, централизованно выпускаемые в США и Англии, содержат канифоль, парафин, церезин, пчелиный и карнаубский воск, акравоск В и другие синтетические воски, полиэтилен, дигликольстеарат и другие продукты. Различные составы из этих компонентов имеют температуру капле-падения 65—95 °С, прочность при статическом изгибе 4,8—8 МПа, зольность 0,07—0,38 %, свободную линейную усадку 0,5—1,5 %.
Область рационального применения составов группы 1 весьма широка — от массового выпуска мелких стальных отливок для
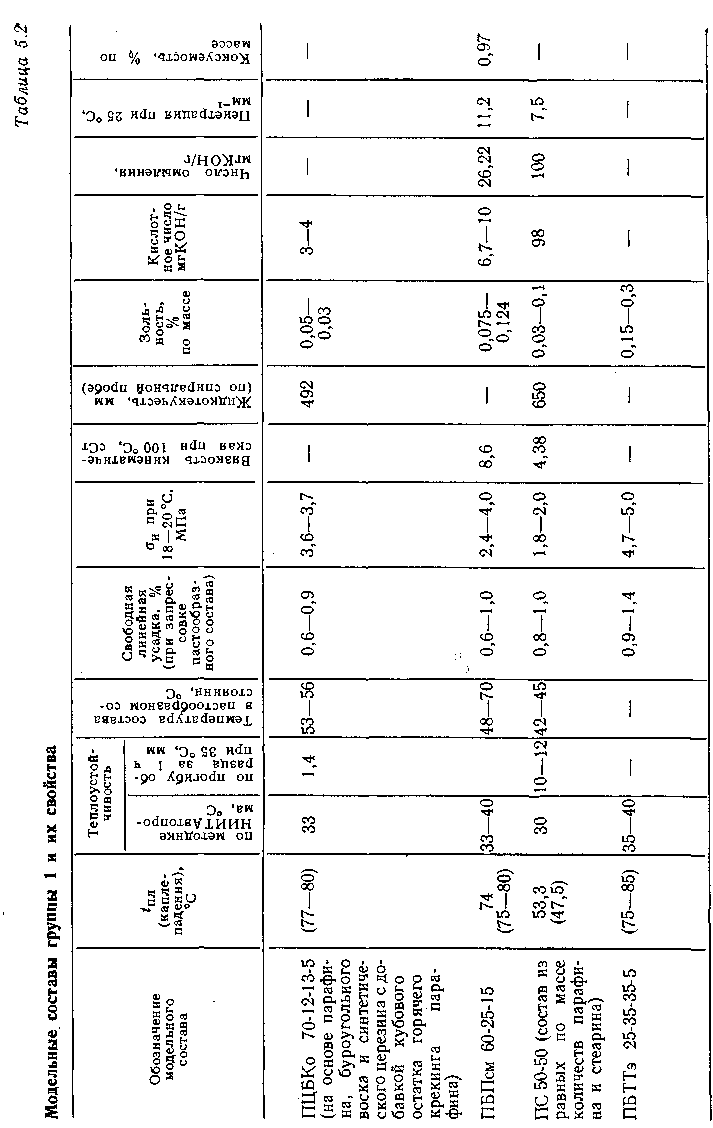
автомобилей, тракторов, сельскохозяйственных и дорожных машин до серийного производства сложных по конфигурации тонкостенных отливок из специальных сплавов, например жаропрочных, в том числе со сложными внутренними полостями, выполняемыми с помощью керамических или растворяемых солевых стержней.
Группа 2 — составы на основе натуральных и синтетических смол, термопластов, например полиэтилена и полистирола, с добавками воскообразных материалов (например, синтетического церезина и парафина). Используются эти составы для изготовления выплавляемых, а в ряде случаев — выжигаемых моделей.
Типичные представители составов группы 2 — КПсЦ 50-30-20 и КЦПэБн 80-18-1,6-0,4, главные характеристики которых приведены в табл. 5.3. Они отличаются от составов группы 1 более высокой прочностью и теплоустойчивостью. Однако применение этих составов ограниченно вследствие специфических недостатков у каждого из них. Составы типа МАИ имеют высокую температуру плавления и запрессовки, температуру каплепадения -~100
С, что исключает воз-.
Таблица 5.3.
Свойства некоторых модельных составов групп 2 и 3
Модельный состав | Состав, % по массе | °н. при 20"С, МПа | Свободная лииейиая усадка, % |
КЦПэБн 80-18-1,6-0,4 | 80 канифоли, 18 церезина, | 6,2 | 0,7 |
(МАИ-Зш) | 1,6 полиэтилена, 0,4 битума нефтяного | ||
КПсЦ 50-30-20 | 50 канифоли, 30 полистирола, 20 церезина | 7,5—8,0 | 0,9—1,43 |
КПсЦ 73-8-19 (модернизированный вариант) | 70—75 канифоли, 5—12 полистирола, 18—20 церезина | 0. 1. N0 | О. 00. & |
КбПвсМс 95,5-2-2,5 (МПВС-2) | 94—96,5 карбамида, 1,5—3 поливинилового спирта, 2— 3 MgS0 4 | 12,0—17,0 | 0 to. 1. о. ъ> |
_КбНк 90-10 (МОН-ЮК) | 90 карбамида, 10 калиевой селитры (KN0 3 ) | 15,0—19,0 | 0,15—0,4 |
Модельный состав | Коэффициент. термического. расширения,. 1/°С | Теплостойкость, °С (по методике НИИТАвто-прома) | ^ПЛ ° с | Зольность, % по массе | Плот. ность. кг/м 8 |
КЦПэБн 80-18-1,6-0,4 | 12-10- 6 | 35 | 90—92 | 0,05—0,08 | 1000 |
(МАИ-Зш) КПсЦ 50-30-20 | 25-10" 6 | >40 | Капле- | 0,03—0,05 | 1000 |
КПсЦ 73-8-19 (модерни | падение. 140 | 0,04—0,05 | 1000 | ||
зированный вариант) КбПвсМс 95,5-2-2,5 | 2,5-10- 6 | 68—72 | 110 | 0,1—0,15 | 1300 |
(МПВС-2). КбНк 90-10 (МОН-ЮК) | 2,6-10- 6 | 70—78 | 125 | 0,15-0,18 | 1320 |
можность применения при их использовании типового оборудования для приготовления модельных составов и изготовления моделей, в котором теплоносителем в обогревающих устройствах служит горячая вода. У этих составов — повышенная зольность и склонность к образованию трещин, плохая смачиваемость суспензией и высокий коэффициент расширения при нагреве. Часто образующиеся на поверхности моделей из этих составов мелкие поверхностные дефекты (обычно — усадочного происхождения) трудно различимы при визуальном контроле, так как составы типа МАИ имеют темно-бурый цвет.
Прочные и теплоустойчивые до 60 °С сплавы на основе канифоли и полистирола с добавками церезина или парафина (типа КПсЦ и КПсП) имеют следующие недостатки: высокую вязкость в расплавленном состоянии, вызывающую необходимость перегревать состав до 160—175 °С при запрессовке и применять давления прессования до 1 МПа и выше, плохую выплавляемость из форм, вследствие чего возврат модельных материалов для повторного использования обычно не превышает 60 %, а при изготовлении весьма тонкостенных отливок столь невелик, что модели используют, как выжигаемые. Ввиду высокой температуры начала плавления и плохих реологических свойств этих составов модели при выплавлении из форм длительное время расширяются, находясь в твердом или высоковязком состоянии. Вследствие этого оболочка испытывает постепенно нарастающее давление расширяющегося модельного состава и должна обладать высокой прочностью, чтобы противостоять этому давлению, не разрушаясь. Для повышения сопротивления оболочки разрушающему действию расширяющейся модели приходится применять дорогой и трудоемкий способ формовки с жидким твердеющим наполнителем. Вследствие необходимости применять значительные давления при запрессовке модельных составом КПсЦ и КПсП исключается использование гипсовых пресс-форм, экономичных в условиях мелкосерийного и опытного производства.
Группа 3 — водорастворимые составы на основе карбамида, азотных и азотнокислых солей щелочных металлов" (нитраты и нитриты калия и натрия), гидратированных сернокислых солей (алю-моаммонийных квасцов, сернокислого алюминия и магния), плавящихся при температуре не выше 35р °С, обладающих малой усадкой, хорошо растворимых в воде. Такие составы применяют в отечественном производстве точного литья более 30 лет. В эти состава вводят улучшающие добавки, например борную кислоту, поливиниловый спирт.
Наиболее распространенные представители составов группы 3— КбБк 98-2, КбНк 80-20, НкНн 55-45, а также приведенные в табл.5.3 КбНк 90-10 и КбПвсМс 95,5-2-2,5. Модельный состав на основе карбамида, недавно запатентованный в Швейцарии, используют при изготовлении крупных тонкостенных отливок (например, воздушных колес компрессора) массой до 35 кг.
Как видно из табл. 5.3, составы группы 3 прочны, теплоустойчивы, имеют малую линейную усадку, в 2—5 раз меньшую, чем у воскообразных составов (см. табл. 5.2). Главные компоненты составов дешевы и недефицитны. Составы на основе карбамида обладают высокой текучестью в расплавленном состоянии, что в сочетании с малой усадкой позволяет получать модели, даже сложные и тонкостенные, методом свободной заливки расплава. Это послужило основанием для использования карбамидных составов при изготов-лении тонкостенных отливок с глубокими узкими полостями, выполняемыми керамическими стержнями. При этом после установки керамического стержня в пресс-форму запрессовку модельного состава, часто вызывающую деформацию и поломку стержня, заменяют заливкой карбамидного расплава, ввиду чего стержень практически не испытывает силовых воздействий. Сохранность стержня обеспечивается и тем, что после изготовления оболочки формы модели на основе карбамида удаляют без нагрева растворением в воде, следовательно, они не оказывают давления на стержень, как выплавляемые, расширяющиеся при нагреве их до температуры начала плавления модельного состава.
Использование модельных составов группы 3 ограничено из-за следующих специфических их недостатков: гигроскопичности, хрупкости, сравнительно высокой температуры плавления (выше 100 °С), большой объемной массы (до 2,1 г/см
), практической непригодности для повторного использования (после растворения), трудностей утилизации раствора. Кроме того, обладающие щелочными свойствами солевые расплавы и их водные растворы могут взаимодействовать с кислыми огнеупорами основы оболочки и пленками связующего, вызывая образование мелких поверхностных дефектов отливок (типа засоров). Защиту поверхности солевых моделей путем нанесения на них тонких пленок негигроскопичных и химически инертных по отношению к материалам суспензии веществ, пока в производстве не используют. Этот метод практически может быть применен, очевидно, только в условиях серийного производства крупных отливок.
Специальной областью применения составов группы 3 является изготовление из них растворяемых в воде стержней для получения в выплавляемых моделях (преимущественно из составов группы 1) сложных каналов и полостей, невыполнимых в пресс-форме, с помощью металлических стержней (см. п. 5.6).
Группа 4 — термопласты, из которых на практике применяют только компактный (монолитный) полистирол и находящийся в стадии производственного опробования, ограниченно используемый вспенивающийся полистирол.
Так как полистирол при нагреве не плавится, а только размягчается (температура.начала размягчения ~80 °С), переходя в вязкопластичное состояние, технологические свойства его стремятся повысить специальными добавками, например, введением до 10 % жирных кислот для снижения вязкости, повышения текучести в нагретом состоянии (при прессовании моделей) и уменьшения хрупкости готовых моделей.
Суспензионный полистирол Для вспенивания перспективен, как материал для получения выжигаемых моделей в условиях массового производства мелких отливок, взамен воскообразных выплавляемых составов, а также при серийном выпуске сравнительно крупных тонкостенных и переменного сечения отливок, например лопаток турбин протяженностью до 0,5 м [551. К преимуществам рассматриваемого материала относятся: теплоустойчивость моделей, что позволяет сушить слои оболочки формы ускоренно, при 70—80 °С, достаточная общая и поверхностная прочность при малой кажущейся плотности: 120—250 кг/м
для мелких тонкостенных и даже 40— 80 кг/м
для отдельных крупных моделей. Уменьшение объемной массы моделей сопровождается снижением их прочности, точности размеров и повышением шероховатости поверхности. Для исключения последнего недостатка О. К. Кошевым, В. М. Белецким и.
Н. Д. Шулаком предложен метод нанесения акрилатного покрытия на рабочую поверхность пресс-формы перед заполнением ее гранулами полистирола для вспенивания.
По данным разработчиков процесса литья в многослойные оболочковые формы по выжигаемым пенополистироловым моделям, отлитым под давлением (ХФ ВНИИЛитмаш), точность получаемых деталей превосходит точность, достигаемую при литье по выплавляемым моделям из легкоплавких модельных составов [5]. Однако, как показали эксперименты [1], выполненные в условиях комплексномеханизированного производства стальных отливок по выжигаемым пенополистироловым моделям, повышенная по сравнению с литьем по выплавляемым воскообразным моделям точность деталей может быть обеспечена только при строгом соблюдении определенных условий их изготовления (температура впрыскиваемого модельного состава -—• 180 °С, пресс-формы 29—34 °С, кажущаяся плотность моделей р = 200-ь220 кг/м®, оптимальное время выдержки моделей в пресс-форме и на воздухе после извлечения из последней), а также с учетом других факторов, в том числе конструкции модели у места подвода, модельного состава. Стабилизация размеров пенополисти-роловых моделей благодаря обеспечению наиболее благоприятных условий их формирования позволяет получать отливки с точностью размеров выше квалитета 13 (СТ СЭВ 144—75), тогда как при традиционном процессе литья по выплавляемым моделям из составов типа Р-3 это обычно не достигается.
Для изготовления литых пенополистироловых моделей Охтинским НПО «Пластполимер», совместно с ХВ ВНИИЛитмаш, разработана специальная марка вспенивающегося полистирола ПСВ-ЛД (выпускаемого ПО «Пластик» в г. Узловая (по ТУ 6-05-05-148—78). Основные технические характеристики ПСВ-ЛД: относительная вязкость 1,55—1,65; содержание порообразователя 4,5—5,5 %; содержание мономера стирола не более 0,035 %; влажность не более 1 %; зольность не более 0,02 %; показатель текучести расплава (ПТР) (15 ± 6) г/10 мин; содержание третичного додецил-меркаптана 0,025 %.
К группе 4 следует отнести и разрабатываемые в Московском авиационном технологическом институте им. К. Э. Циолковского (МАТИ) составы из вспенивающихся в пресс-форме и отверждающихся полиэфиров.
Группа 5 — легкоплавкие металлы и сплавы. Из металлов промышленное применение в качестве модельного материала получила ртуть, свободно заливаемая в пресс-формы при комнатной температуре и замораживаемая в ацетоне, охлажденном до —60 °С. Процесс литья по ртутным моделям («меркаст-процесс»), подробно описанный в английской и американской специальной литературе, несмотря на высокое качество получаемых отливок, широкого распространения в мировой практике литья по выплавляемым моделям не получил и в СССР не применяется вследствие исключительной токсичности паров ртути, сложности метода, высокой стоимости модельного материала.
В зарубежной литературе неоднократно сообщалось о возможности использования для изготовления моделей легкоплавких, преимущественно эвтектических сплавов металлов, например сплава Вуда (основа — висмут, t
„ = 68 °С). Однако сведений о промышленном применении таких модельных сплавов нет.
Группа 6 — модельные составы, представляющие собой механические смеси или сплавы составов, например, водорастворимых (группа 3) и воскообразных (группа 1). По данным Н. С. Севостья-нова и В. В. Апиллинского, в таких составах удается значительно уменьшить Недостатки образующих их составляющих: гигроскопичность, хрупкость и склонность к взаимодействию с формой карба-мидных составов, малую прочность и теплоустойчивость воскообразных легкоплавких материалов. Однако приготовление комбини* рованных составов усложняется ввиду плохой совместимости компонентов, а при запрессовке их необходимо применять давления (>0,5 МПа), существенно превышающие применяемые для воскообразных составов. Наличие же последних в смеси приводит к снижению прочности и теплоустойчивости, характерных для карба-мидной составляющей.
При удалении моделей в горячей воде повторно может быть использована только воскообразная часть комбинированного состава и возникают трудности с утилизацией карбамиднош раствора.
Группа 7 — составы с твердыми наполнителями. Основа их — преимущественно составы группы 1, в которые вводятся порошки, например, синтетических смол или тугоплавких восков; плотность их близка к плотности расплава основы. Такие порошки образуют твердую взвесь в расплавах основы состава, снижая и стабилизируя усадку, следовательно, повышая точность моделей, а также увеличивая их прочность и формоустойчивость. Введение в расплав воскообразного модельного состава 10—15 % порошка синтетической смолы снижает свободную линейную усадку этого состава при зат-рердеванщ с 1,5—2 до 0,5 %,