В своих опытах я разработал подобный метод для работы со стерлинговым серебром. Пайка стерлингового серебра не нуждается в применении припоя, но всецело зависит от физико-химических свойств самого сплава. При образовании на поверхности гранул обогащенного слоя серебра возникает разница в температурах плавления, именно это позволяет контролировать процесс пайки. Грануляция по большей части дело практики, чем теоретических знаний. Никакое количество прочитанной литературы не заменит тех наблюдений и выводов, которые вы сделаете, экспериментируя.
.
Инструменты, оборудование и материалы.
Большинство инструментов и материалов, необходимых для этого процесса, входят в стандартный набор инструментов ювелирной мастерской. Вальцы и муфельная печь помогут сэкономить время, но их наличие необязательно.
• горелка для пайки с наконечниками №1(или 1А)и №3.
• угольный блок для пайки.
• флюс для пайки.
• ножницы.
• пинцет с тонкими губками (часовой).
• кисточки из собольего меха (000 и 00).
• отбел (сернокислый раствор или Спарекс).
• латунная щетка.
• термостойкая посуда и форма для пирога.
• необязательно: муфельная печь, графитовый тигель, перчатки и клещи.
• неглубокая посуда или большая ложка.
• сито и контейнеры для хранения гранул.
Изготовление зерни.
Гранулы изготавливаются из серебряной фольги толщиной от 0,16 до 0,255 мм (36-30 B&S). Если имеются вальцы, фольгу можно сделать из небольших кусочков чистого (без припоя) листового стерлингового серебра, постепенно сводя валы до тех пор, пока они полностью не сомкнутся. Несколько прогонов через вальцы позволят получить фольгу необходимой толщины. Если до изготовления фольги листовое серебро уже подвергалось отжигу, последующего отжига не требуется. Поскольку фольга в процессе обработки будет измельчена, трещины по краям не представляют проблемы. Если вальцов нет, купите как можно более тонкую фольгу или прокуйте листовое серебро на чистой наковальне. Более толстой фольгой также можно работать, ее просто труднее измельчать .
Прокатывайте чистый лист серебра, пока он не станет очень тонким, затем измельчите его, сделав бахрому и нарезая ее поперек.
.
Расстелите лист бумаги под тисками, чтобы на него падали партинки.
Прим, переводчика.
B&S (Brown & Sharp gauge) - стандарт, принятый в США, для измерения диаметра проволоки или толщины листового металла. Используется только при работе с цветными металлами.
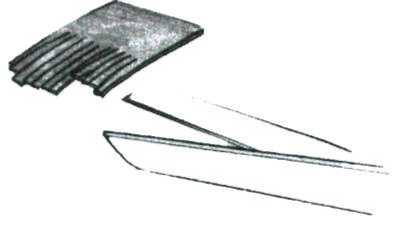
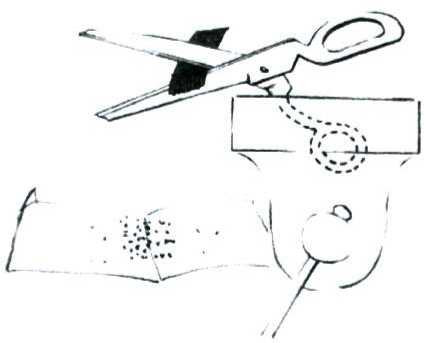
Хорошо очистите фольгу, затем порежьте ее на крошечные партинки точно таким же образом, как если бы вы резали листовой припой. Кусочки фольги должны быть размером около.
1,5 квадратных миллиметров (1/16 квадратного дюйма), если используется фольга толщиной до 0,16 мм (36 B&S). Так как нельзя нарезать идеально ровных партинок, то и гранулы получатся несколько различных размеров.
Примите меры предосторожности, чтобы партинки не падали на пол. Если требуется большое количество зерни, зажмите одну ручку ножниц в тисках, как показано на рисунке.
Под тиски подложите большой лист бумаги, чтобы на него падали кусочки фольги. Когда получено необходимое количество партинок (а их понадобится большое количество -не экономьте), ее можно будет расплавить в сферические гранулы (зернинки). Это можно выполнить либо в муфельной печи, либо при помощи горелки на специально подготовленном угольном блоке.
.
Сплавление в муфельной печи.
Нагрейте муфельную печь до 1038 С (1900 F) и дайте ей полностью прогреться. Пока прогревается печь, приготовьте такое количество пыли из древесного угля, достаточного для того, чтобы наполнить имеющийся у вас графитовый тигель. Ее можно приготовить, сточив напильником или измельчив старые угольные блоки для пайки. Работайте грубым напильником над куском ткани или заверните уголь в пакет из плотной бумаги и измельчите его деревянным молотком. В целях экономии угольных блоков для пайки, используйте старые блоки или древесный уголь для барбекю. Лучше всего этим заниматься на улице, процесс может оказаться очень грязным.
Попеременно укладывайте слои пыли и партинок в тигель.
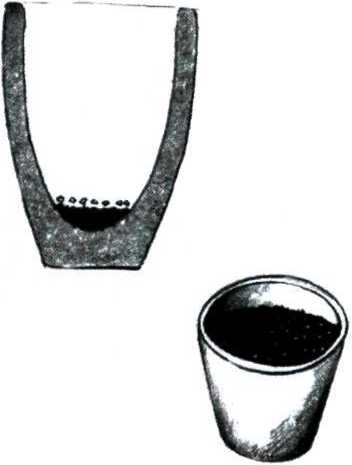
На дно тигля насыпьте слой пыли толщиной 6,5 мм (1/4 дюйма), поверх него набросайте небольшое количество серебряных партинок. Партинки должны быть распределены как можно более равномерно, поскольку те, которые будут соприкасаться, в результате сплавятся между собой. Чередуйте слои пыли и партинок до тех пор, пока до края не останется 6 миллиметров, последний слой -угольная пыль. На тигель положите несколько отрезков железной проволоки (например, крючок от плечиков) и накройте его неглазурованной керамической плиткой или листом из огнеупорного кирпича.
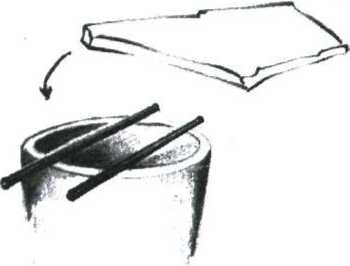
Крышку для тигля сделайте из куска керамики или огнеупорного кирпича, уложите ее на крючки от плечиков или сварочные электроды.
Когда температура в печи достигнет 1038°С (1900°F), при помощи клещей осторожно поставьте в нее закрытый тигель. Конечно, необходимо надеть защитные рукавицы, чтобы избежать ожогов. Наполненный тигель нужно перемещать очень осторожно, чтобы избежать оседания партинок. Если это произойдет, в результате на дне окажется кусок металла вместо множества крошечных зернинок.
После того, как печь нагрелась до необходимой температуры, тигель необходимо выдерживать в печи в течение 15 минут. Вообще, время, необходимое для того, чтобы партинки полностью расплавились, будет зависеть от количества металла и от размеров и толщины стенок самого тигля. Через 15 минут выньте тигель из печи и зачерпните ложкой верхний слой. Если партинки верхнего слоя полностью расплавились и превратились в сферические гранулы, вероятнее всего, что то же самое произошло и с партийками нижнего слоя. Если процесс плавления незавершен, тигель нужно снова накрыть и поместить в печь на некоторое время. Проверяйте течение процесса каждые 10 минут до тех пор, пока все партинки не превратятся в гранулы.
Когда плавка завершена, выньте тигель из печи и высыпьте уголь с гранулами с высоты 2 5 - 3 0 сантиметров (10 - 12 дюймов) в чашку из термостойкого стекла с водой (высота воды не должна быть менее 7 см (3 дюймов)). Эта операция может быть проделана, когда содержимое тигля станет тускло-красного цвета. Сам тигель быстро охлаждать нельзя. Поместите чашку с содержимым под тонкую струю воды, при этом вся угольная пыль и пепел смоются водой. После этого воду аккуратно отфильтровывают, оставляя россыпь идеально ровных гранул. Переложите гранулы в другую чашку из термостойкого стекла, наполненную отбелом. Зернинки должны оставаться в отбеле до тех пор, пока их поверхность не станет ровного белого матового цвета. Этот процесс можно ускорить, если раствор подогреть, но не доводить до кипения.
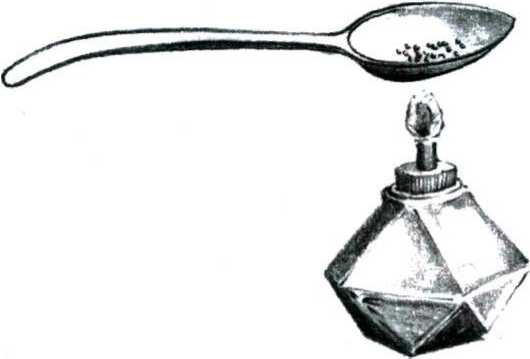
Высушите промытые гранулы в ложке при помощи слабого огня.
.
.
Когда гранулы протравятся, остудите отбел и тщательно промойте зернинки, чтобы удалить все остатки кислоты. Аккуратно слейте воду из чашки, поместите их в ложку и осторожно подогрейте снизу на медленном огне. Нагревать нужно только для того, чтобы выпарить оставшуюся влагу. Когда зернинки высохнут и начнут свободно кататься по дну ложки, погасите огонь и оставьте их остывать. Теперь гранулы готовы к дальнейшему использованию. Если гранулы нуждаются в сортировке, сделайте это сразу и разложите гранулы разного размера по отдельным контейнерам.
.
Изготавливая гранулы при помощи горелки, обогните угольный блок медной рамкой. Это не позволит зернинкам скатываться в стороны.
Метод «свободного падения»
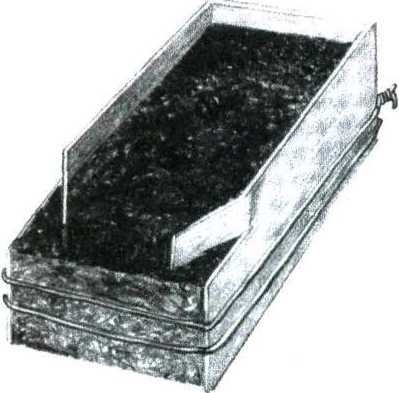
Для второго способа изготовления зерни требуется только угольный блок и горелка, чтобы сплавить металл. Несмотря на то, что оборудования требуется меньше, этот процесс более трудоемкий, потому что за один раз можно изготовить лишь небольшое количество гранул. Когда я использую этот метод, я устанавливаю угольный блок в специальную металлическую рамку-каркас, которая предотвращает скатывание зернинок в разные стороны.
Нарежьте серебряных партинок так, как было описано выше.
Насыпьте их на угольный блок, который должен быть установлен под небольшим углом к поверхности открытой стороной вниз над чашкой из термостойкого стекла, наполненной водой, на высоте около 3 0 см (12 дюймов). Горелкой с наконечником №1 или №2 расплавьте каждую партинку отдельно, начиная с нижнего края и постепенно поднимаясь вверх. Превратившись в шарик, зернинка скатится в воду. Металлическая рамка не позволит гранулам скатиться в стороны и направит их в чашку с водой. Процедура повторяется до тех пор, пока вы не получится достаточное количество зерни. Затем гранулы отбеливаются, промываются и сушатся так, как было описано ранее.
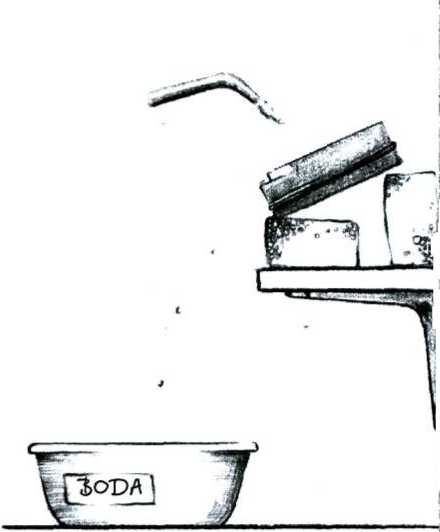
Поскольку блок установлен под наклоном, зернинки, приобретая форму шариков, будут скатываться вниз. Убедитесь, что времени падения достаточно для того, чтобы гранулы застыли перед падением в воду.
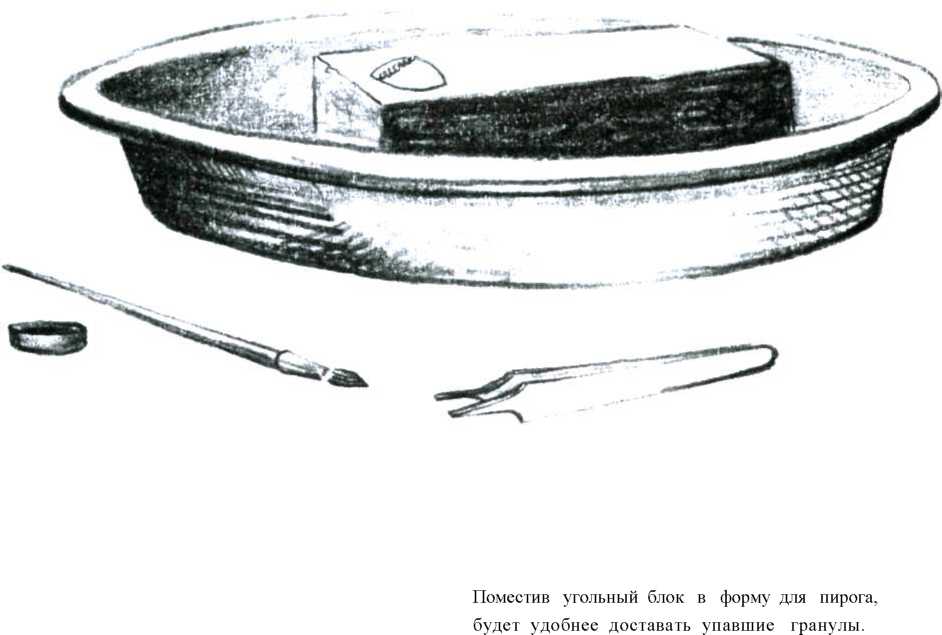
Подготовка поверхности.
Основа или поверхность, куда будет напаиваться зернь, должна быть толщиной 0,511 - 0,813 мм (24 - 2 0 B&S). Более тонкие поверхности быстро перегреваются и могут расплавиться до того, как начнет припаиваться зернь. Небольшие диски диаметром 1,2 - 2,0 см (1/2 - 3/4 дюйма), вырубленные при помощи вырубного штампа и сформированные в анке, идеально подходят для тренировки.
До посадки гранул основу необходимо как следует подготовить. Если грануляция производится на стерлинговом серебре, требуется слегка шероховатая основа. Для придания шероховатости (практически невидимой) пользуйтесь пастой High rouge, поскольку пемза и наждачная бумага делают поверхность более грубой. Основа должна выглядеть так, как если бы ее подвергли пескоструйной обработке. На основе не должно быть ни зазубрин, ни царапин, так как после напайки гранул удалить царапины практически невозможно.
После предварительной подготовки основу промывают в мыльном растворе, чтобы удалить остатки пасты, жиров и т. д., а затем обрабатывают раствором нашатырного спирта. При ополаскивании вода должна свободно стекать с поверхности. Если вода собирается в капли, процедуру очистки следует повторить. Чистой салфеткой вытрите поверхность насухо, удерживая образец за края, чтобы не оставить на ней отпечатков пальцев.
Поместите образец на угольный блок, установленный в форме для пирога, как показано на рисунке.
.
.
Укладка гранул.
Для того чтобы перенести гранулы на основу, слегка смочите кисть №1 во флюсе и обмакните ее в контейнер с гранулами. Очень удобно сначала поместить небольшое количество зерни на основу, чтобы затем выкладывать ее по рисунку.
Начиная с одного края рисунка, укладывайте гранулы при помощи кисточки из собольего меха (000 или 00) и пинцета с тонкими губками. Если флюс быстро испаряется, добавьте кисточкой каплю дистиллированной воды. Добавлять флюс не следует, поскольку его излишек может привести к его кипению и смещению зерни в процессе напайки. Когда выкладка узора завершена, оставшуюся зернь бережно уберите как с основы, так и с угольного блока на дно формы (так их легче будет снова пускать в работу). Удалите излишек влаги сухой кисточкой, после чего дайте изделие полностью просохнуть (обычно это занимает около 15 минут).
Разместите изделие на угольном блоке ближе к углу, чтобы иметь пространство для работы горелкой. Используя наконечник №3, отрегулируйте пламя горелки таким образом, чтобы игла пламени была слегка желтой (точно такая же температура используется для пайки). Удерживая головку горелки на высоте 5 сантиметров (2 дюймов) над рабочей поверхностью, плавно понижайте давление горючей смеси до тех пор, пока пламя не приобретет форму гриба 4-5 сантиметров (1,5
Наплавка зерни
- 2 дюйма) в диаметре. Внутри отрегулированного таким -образом факела создается восстановительная среда.
Медленно приближайте пламя к изделию, пристально отслеживая испарения флюса и любые сдвиги зерни. Работайте горелкой на уровне глаз, чтобы площадь обзора была максимальной. Если сдвигов нет, совершайте горелкой возвратнопоступательные движения, направленные перпендикулярно изделию. Пока все изделие не нагрелось до красного свечения, его необходимо держать внутри факела, чтобы избежать образования оксидной пленки. По мере достижения необходимой степени нагрева уберите пламя, чтобы обеспечить равномерное рассеивание тепла и предотвратить перегрев гранул.
При нагревании до краснооранжевого цвета поверхность начнет запотевать и становиться блестящей, похожей на зеркало. В этот момент происходит процесс сплавления. Поскольку с виду похожий на ртуть ободок появляется только у основания гранулы и только на мгновение, очень важно расположить рабочую область на определенной высоте так, чтобы процесс сплавления хорошо просматривался.
Процесс сплавления проходит локализовано, поэтому изделие необходимо вращать и нагревать, пока процесс сплавления не пройдет по всему рисунку. Я советую полностью отвести пламя, дать возможность изделию остыть до ярко красного цвета, а затем переходить на. новый участок. Если в этот момент поддерживать пламя, то возможно как частичное оплавление, так и разрушение всего изделия. Когда процесс завершен, проверьте качество соединения зерни с основой, аккуратно надавливая на зернинки пинцетом. Если качество удовлетворительное, выключите горелку, оставьте изделие остывать, а угольный блок промокните влажной грубой тканью. Изделие нельзя быстро охлаждать, поскольку струи пара могут сместить гранулы.
В этот момент гранулы и основа стали единым целым с гомогенной структурой. После отбеливания изделие можно паять, не опасаясь расплавления зерни. По сути, мои наблюдения говорят о том, что повторное нагревание улучшает качество связи зерни с основой.
Очистка и окончательная обработка .
После остывания изделие отбеливается обычным способом -сернокислым раствором или Спарексом, ополаскивается раствором пищевой соды для нейтрализации кислоты, которая может оставаться в зазорах между гранулами, и промывается водой. Осторожно обработайте поверхность латунной щеткой, используя жидкое мыло и воду в качестве смазки. Это придаст гранулам определенный блеск. Если требуется более высокая степень полировки, после крацевания отшлифуйте поверхность пастой High rouge. Гранулированную поверхность ни в коем случае нельзя подвергать полировке на шлифовальном моторе. Даже используя пасту, гранулы легко стираются, становятся плоскими, тем самым они теряют сферическую целостность. Кроме этого, их можно зацепить и сорвать с поверхности. Изделие с грануляцией оксидируется в растворе «серной печени», как и любой предмет из стерлингового серебра. Выступающие части узора можно осветлить при помощи пальца с небольшим количеством пемзы, или латунной щетки. Эффект светлой зерни на более темном фоне основы используется для подчеркивания рельефа.
Некоторые наиболее распространенные проблемы
Науглероживание зерни.
При изготовлении зерни в муфельной печи поверхность гранул часто чернеет, что не всегда удается снять отбелом. Почерневшая, поверхность является результатом науглероживания или поглощения углерода вследствие длительного нагревания партинок в наполненном угольной пылью тигле. Такое часто происходит, когда тигель помещают в холодную печь, а затем нагревают. Постепенное повышение температуры позволяет серебру соединяться с углеродом, в результате на поверхности серебра образуется слой металлического карбида, крайне стойкого к действию отбела. Чтобы избежать науглероживания, помещайте тигель в печь только после того, как она прогрелась до необходимой температуры. Выдерживать же тигель в печи нужно ровно столько времени, сколько требуется для сплавления партинок в гранулы.
Если же науглероживание все-таки произошло, гранулы необходимо повторно нагреть и погрузить в теплый сернокислый раствор до тех пор, пока их поверхность не станет матово-белой. Если гранулы просто поместить на длительное время в отбел, карбид не удалится, а металл покроется коррозионной пленкой вследствие контакта с кислотой. Для снятия углеродной пленки необходимо не менее 2-3 циклов нагревания -отбеливания. При этом гранулы нагреваются только до температуры 2 04-2 60 ° С (400-500 ° F) . Небольшой лист бумаги, уложенный на дно сосуда, в котором нагревается зернь, служит отличным индикатором температуры. Когда бумага начнет становиться бурого цвета (233°С, 450°F), гранулы нужно будет немедленно опустить в теплый отбел, в котором их необходимо выдерживать не более 2 -3 минут перед повторным циклом.
Окисление.
Образование оксидной пленки на поверхности основы в течение начальной стадии нагревания обычно служит показателем того, что пламя горелки не отрегулировано или неправильно охватывает поверхность, то есть не создается достаточная восстановительная атмосфера. В определенной степени окисление будет присутствовать, но обычно с этим легко справляется флюс. Когда же количество оксидной пленки превышает допустимый уровень, единственный вариант справиться с ней - заново отбелить основу и зернь и все начать сначала. Поскольку окисление препятствует образованию «ободков» в зоне контакта гранулы с основой, продолжать нагревание бессмысленно, а также потенциально опасно. Попытки ускорить сплавление зерни путем повышения температуры часто заканчиваются разрушением или оплавлением изделия.
Перегрев.
Средства от перегрева не существует, единственное решение -четкий контроль над температурой. Если изделие продолжать нагревать после запотевания, очень быстро начнут проявляться признаки распада и, в итоге, изделие полностью расплавится. А это, в свою очередь, приведет к скрежету зубами и ругани.
Первая степень перегрева -деформация поверхности основы. Это хорошо заметно на выпуклых поверхностях, поскольку перегретые области изделия прогибаются и оседают. На плоских поверхностях, установленных на угольном блоке, эффект менее очевиден и проявляется в виде легкой деформации.
Следующая степень чрезмерного нагревания - воздействие на сами гранулы. Они становятся неспособными сохранять свою сферическую форму и начинают растекаться, образуя аморфные холмики на поверхности. Приблизительно в то же самое время края изделия начинают разрушаться, и изделие может полностью расплавиться. Временной интервал от момента запотевания поверхности и полного плавления занимает считанные секунды.
Оседание, деформация и расплавление гранул - три проблемы с одной причиной, имя которой - перегрев.
Образование пор, каверн и вздутий.
При грануляции стерлингового серебра следует ожидать появления некоторых поверхностных дефектов. Они могут быть как незначительными, так и портящими внешний вид изделия. В большинстве случаев деформация поверхности происходит вследствие одного или нескольких факторов:.
• общий или местный перегрев поверхности.
• излишек флюса.
• отпечатки пальцев или другое загрязнение поверхности.
• чрезмерное количество оксидной пленки, которая образуется на начальной стадии нагревания.
• пламя горелки находится в непосредственной близости от рабочей поверхности.
Неполное сплавление.
Даже при самом благоприятном стечении обстоятельств одна или несколько зернинок из всего узора могут не присоединиться к поверхности. Если это произошло, просто поместите изделие в отбел, очистите его, установите гранулы в нужное положение и снова нагрейте. Если ни одна гранула не присоединилась к основе, причину следует искать в избыточном окислении или низкой температуре горелки. Единственный выход - все начать заново.
Слабое или пористое соединение.
Образование слабых, пористых «ободков», а также частичное присоединение зерни является следствием окисления или низкой температуры. Очень важно в процессе напаивания отчетливо проследить образование «ободков».
Проблемы с выкладкой узора.
Одним из наиболее утомительных (и раздражающих) аспектов грануляции является выкладка узора зернью. Временами гранулы будут вести себя весьма своевольно. Гранулы могут скатываться и образовывать характерные фигуры: треугольники из трех зернинок, и пирамиды из четырех. Если гранулы слишком сухие, их трудно сдвигать. Если они слишком влажные, последнее неосторожное движение может разрушить уже полностью выложенный узор. Неосторожное обращение с изделием после сушки также влечет полное исчезновение узора. Большинство из этих проблем преодолевается терпением и опытом. Делайте перерывы, чтобы расслабиться, и пользуйтесь глазными каплями для снятия напряжения.
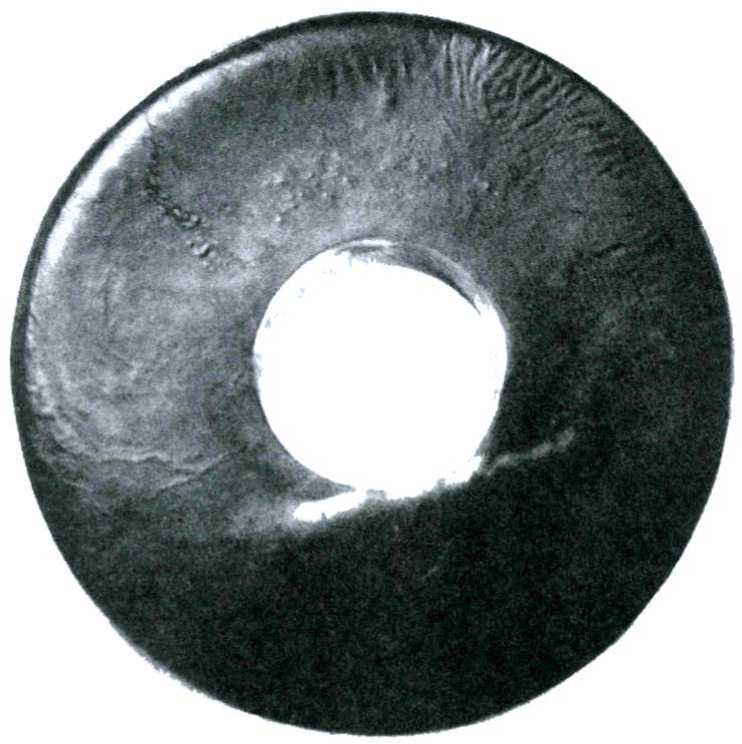
Чернь.
Чернь - блестящее вещество, изготавливаемое ювелирами, обычно используется для декоративных работ подобно эмалированию. Несмотря на то, что с технической точки зрения чернь - не металл, она выглядит, плавится, режется и полируется, как металл. Чернь - уникальный материал, занимающий выдающееся место в истории искусств.
Чернь изготавливается путем сплавления меди, серебра и свинца в тигле с последующим добавлением в сплав серы для получения смеси сульфидов. Окраска этого хрупкого материала варьируется от сероголубого до черного цвета. Со времен античности чернь использовалась для выделения декора на изделиях из золота или серебра. Чернь неэластична и не поддается ковке, но становится жидкой при относительно низкой температуре и легко соединяется с поверхностью благородного металла. Наплавленную на металл, чернь можно полировать до зеркального блеска при помощи стандартных приемов обработки металлов.
Происхождение черни неизвестно, возможно она имеет доисторическое происхождение, возможно, ее случайно изобрели алхимики. С ранних времен техника чернения встречается в Европе, Египте, на Среднем и, чаще всего, на Дальнем Востоке, особенно в Таиланде. Она приобрела популярность благодаря легкости использования, доступности компонентов и способности усиливать контраст между сочетаниями света и тени, которые присущи узорам на художественных изделиях.
В Эпоху Возрождения в Италии все, что касалось искусства, развивалось и процветало. В течение этого времени резцовой гравюрой занимались ювелиры, они изготавливали копии художественных полотен на металле, поскольку художникам - живописцам не хватало технических навыков. Интересен тот факт, что до XV века людьми не осознавалась возможность использовать выгравированные на металле изображения в качестве клише для книгопечатания. Несмотря на то, что механическая гравировка и химическое травление широко использовались для создания рисунка на металле, возможности использования данной технологии для печати тогда не рассматривались.
Для гравера естественно периодически проверять ход своей работы путем втирания темной пасты в гравюру. Дело оставалось за малым.
- очистить поверхность после покрытия ее чернилами, оставляя краску в углублениях. Когда на подготовленную таким образом гравюру накладывали лист влажной бумаги и плотно прижимали, на бумаге оставался отчетливый оттиск изображения с одним отличием -рисунок отпечатывался в зеркальном отражении.
Я в своих исследованиях пришел к выводу, что гравюра как процесс создания рисунка явилась переходным этапом, ведущим к появлению технологии глубокой печати, которая процветает с XVI века, а техника чернения дала толчок ее развитию.
Естественно предположить, что мастера того времени быстро оценили, насколько выгодно делать копии отпечатков. «Зачем браться за изготовление одного изделия, когда можно сделать много?». Появление этой мысли привело к разделению назначений гравюры: прямое назначение гравюры как художественного изделия и клише для производства оттисков (печатных форм).
Отношения ювелир - гравер -печатник продолжались относительно недолго - около 100 лет. Популярная иконография в то время включала числа, обозначающие конкретную дату, девизы, эпиграфы или афоризмы, которые можно было бы прочитать на гравюре, но которые давали зеркальное отображение оттиска. Очень скоро стало понятно, что выгравированная надпись, которую можно было бы прочитать на оттиске, означала многократное получение оттисков. Ювелир -гравер, изготовивший уникальное изделие, заполнял углубления гравюры чернью, фиксируя изображение и, тем самым, делая его использования для печати невозможным. Таких мастеров стали называть niellist, а их работы -nielli. К XVIII веку такие работы стали достаточно большой редкостью и оказались предметом поиска знатоков искусства и коллекционеров, тем самым, создавая благоприятные условия для их подделок.
Открытый горн с некоторыми усовершенствованиями.
Приточно-вытяжная вентиляция.
Отвести вредные и опасные пары продуктов горения металлов, флюса и серы можно при помощи самодельного вытяжного шкафа. Идеально подходит лабораторный газоуловитель, хорошо с этим справляется и коксовый кузнечный горн с сильным восходящим потоком воздуха, но, если под рукой нет ни того, ни другого, представляю самодельную модель, которая неплохо служила мне в прошлом.
На рисунке изображен вытяжной шкаф, который я сделал из картона и старой мебели. Начните работу с поиска окна, которое и будет служить для отвода вредных газов, предпочтительно вдали от людей и улиц с интенсивным движением. Установите в окно 60-сантиметровый (24-дюймовый) вентилятор, проще говоря, просто поставьте его на подоконник. При необходимости для устойчивости закрепите его скобами.
Когда вентилятор установлен, можно определить размеры самого шкафа, которые в свою очередь зависят от размеров оконной рамы. Обратите внимание на то, что шкафы меньших размеров оперируют меньшей воздушной массой, а поэтому более эффективны. Переднюю стенку можно оставить полностью открытой или вырезать в ней отверстие, как показано на рисунке.
Я сконструировал несколько подобных шкафов, поскольку руковожу работой нескольких мастерских по всей стране, и могу сказать, что наиболее удачный вариант - простой шкаф, сделанный из гофрокартона. Можно использовать и простую коробку, но боле прочный шкаф получится, если сначала изготовить каркас из деревянных реек, отрезанных по размеру и скрепленных гвоздями. Затем к каркасу приклеивается картон и закрепляется скотчем. Необходимые материалы -картонная коробка от холодильника, молоток, однодюймовые (25 мм) мебельные гвозди, большие ножницы, перочинный нож и клей. Всю конструкцию можно собрать в течение одного часа. Теоретически можно изготовить шкаф для отвода вредных газов из огнеупорных материалов, который действительно прослужит вам сотни часов, хотя я с возгоранием картонных вытяжных шкафов никогда не сталкивался. Надеюсь, что ваш здравый смысл и соображения безопасности не создадут исключения из этого правила.
Проверьте силу тяги, поместив под шкаф плотно скомканный газетный лист. Подожгите его, а затем потушите, чтобы создать дым. Если дым моментально полностью не выветривается, уменьшите шкаф в размерах и проверьте тщательность стыков. Под шкафом будут скапливаться отвратительные запахи, и вы сможете предотвратить попадание их в свои легкие при помощи собственного же мастерства.
Я всегда сожалею, когда мне приходится разбирать хороший вытяжной шкаф.
На рисунке представлен вариант вытяжного шкафа, который изготовлен из картона на деревянном каркасе, с использованием обычного бытового вентилятора.
Рабочий стол.
Работа выполняется на устойчивом столе с огнеупорной поверхностью. Для этой цели достаточно на обычный деревянный стол выложить ряд из трех кирпичей. Наиболее подходящая высота - уровень кухонного стола. Тигель будет находиться на кирпичах, установленных в шкафу, это я называю «Островом Тигля». Он приподнимает тигель с тем, чтобы его было легче вынуть, а также позволяет задвигать тигель глубже внутрь, если этого требует тяга.
.
Тигли.
Для работы подойдут керамические, графитовые тигли и тигли, сделанные из гнесинской глины. Я предпочитаю использовать тигли марки «Burno», емкость которых 155 г (100 пеннивейт). Съемная крышка помогает аккумулировать тепло, облегчая процесс плавки.
.
Тигельные щипцы.
Захватывающие концы железных щипцов необходимо отковать, придав им форму пальцев, тем самым вы обеспечите себе уверенный и удобный захват тигля. Изготовление черни требует постоянного внимания и контроля, поэтому в обращении с тиглем требуется такая сноровка, как если бы вы работали голыми руками. Времени на колебание не будет, кроме того, это небезопасно, поскольку содержимое тигля может пролиться. Одна рука у вас будет занята горелкой, поэтому вторая должна быть натренирована. Придайте щипцам нужную форму и тренируйтесь ими до тех пор, пока вы не сможете снять крышку без колебаний.
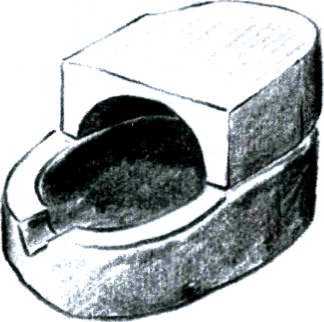
Такие щипцы можно либо купить, либо сделать самому. Они должны быть отрегулированы таким образом, чтобы обеспечить уверенный захват тигля. Шабер и ложка для помешивания, сделанные из стального прута, помогут вам в работе.
.
Я предпочитаю тигли подобного типа, хотя можно использовать и другие. Перед использованием я протачиваю канавку на задней стенке тигля, чтобы было проще работать щипцами.
Шабер и ложка для помешивания.
В процессе приготовления порции черни тигель необходимо выскабливать, а смесь перемешивать. Для обеих операций можно использовать обычный железный стержень, но лучше иметь два разных приспособления, которые изготавливаются из двух стержней около 60 см (2 футов) длиной и, как минимум, 6,5 мм (1/4 дюйма) в диаметре. Инструмент, представленный на рисунке, является образцом, но вы можете придать инструменту любую форму, которая будет способствовать удовлетворению ваших потребностей. Помните, что инструмент, используемый для приготовления черни, можно применять исключительно для этой цели: вы же не хотите появления следов черни, которые загрязняют золото или серебро, в процессе литья или пайки.
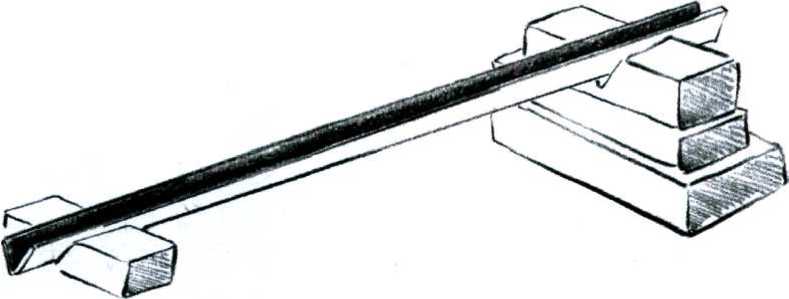
Железный уголок установлен на деревянных брусках для создания наклона, представляя собой изложницу для черни Splendid Rod.
Изложница.
В своей работе я преимущественно использую чернь Splendid Rod, хотя некоторые мастера предпочитают работать с порошком, используя технику эмалирования. Для этого чернь выливается в воду, в самодельную изложницу или на лист металла. Теперь чернь можно измельчить и превратить в пыль при помощи ступки и пестика. Для розлива черни я предпочитаю использовать желоб из железного угольника, расположенный под наклоном, который предварительно нужно прокоптить. Перепробовав несколько типов желобов, я остановил свой выбор на стандартном стальном уголке с полкой 2,5 - 4 см (1 - 1,5 дюймов), установленном на деревянных брусках, как показано на рисунке. Для работы в мастерской я использую уголок длиной 120 - 150 см (4-5 футов), хотя я использовал изложницы длиной 360 см (12 футов), а для черни Splendid Rod - длиной 3 метра (10 футов 2 дюйма).
Вспомогательные инструменты.
• весы.
• емкости для серы и флюса и ложки с длинными ручками. Они легко изготавливаются путем припаивания железного стержня к чайной ложке.
• небольшая коробка с песком, чтобы устанавливать емкости в разных положениях.
• небольшие емкости для металлических компонентов.
• пинцет для снятия готовой черни.
Полезно, чтобы у вас вошло в привычку выкладывать все инструменты и материалы перед началом работы. Вообще, я бы порекомендовал окинуть их беглым взглядом, чтобы убедиться, что все на своих местах и в рабочем состоянии. Изложница должна быть под рукой, в одном шаге от горелки и тигля.
.
Рецепты.
Литературы по технике чернения недостаточно, и часто авторы противоречат друг другу. Будучи студентом, мне посчастливилось иметь доступ к книге Н. Wilson "Silverwork and Jewelry", одна из глав которой содержит несколько рецептов черни. Несомненно, Вилсон перепробовал несколько вариантов пропорций и, в конечном счете, выбрал сплав из 6 частей серебра, 2 частей меди и одной части свинца. Экспериментируя сам, я остановился на сплаве, в который добавил еще одну часть свинца, а именно:.
6 частей чистого серебра,.
2 части меди,.
2 части свинца.
Завершают рецепт 2 столовые ложки с горкой серы, этого количества достаточно, чтобы превратить эти металлы в их сульфиды. Поскольку изготовление черни - процесс, требующий пристального контроля, сначала я рекомендовал новичкам начинать с небольших количеств. Но потом изменил свое мнение, так как с большими порциями легче работать. Лично я начинал с 12 граммов серебра (соответственно по 4 грамма свинца и меди).
Я предпочитаю использовать чистое серебро, бескислородную медь и чистый свинец, но я также изготавливал чернь и из стерлингового серебра, медной стружки, свинца для слесарных работ и серы, используемой для удобрений. При качественном подходе к изготовлению черни и эти материалы дают превосходный результат.
В принципе, нет необходимости идеально соблюдать весовые пропорции компонентов. Плюс-минус полграмма не сыграют большой роли. Основным фактором успеха является то, как вы используете огонь.
Крайне важно поддерживать сплав нагретым, но не перегревать его.
Если вы впервые используете тигель, его необходимо покрыть слоем флюса. Нагрейте тигель до ровного красного цвета, а затем покройте внутреннюю поверхность бурой (Borax flux), при необходимости повторите операцию.
В результате тигель должен быть покрыт изнутри чистым блестящим слоем флюса.
Введите медь и доведите ее до плавления. Бросьте серебро и продолжайте нагревать тигель. Размешивайте сплав до тех пор, пока он не образует однородную массу.
Всегда имейте в виду, что, начиная с этого момента, сплав можно перегреть или сделать процесс очень длительным.
Введите свинец и слегка взболтайте тигель круговыми движениями, чтобы металлы смешались. Достаточно двух оборотов. На этом этапе необходимо тщательно контролировать температуру нагрева и работать без промедления. Поместите тигель на подставку и включите вытяжку. Одним ловким движением опустите в сплав столовую ложку серы. Сера моментально воспламеняется, создавая при этом впечатляющее зрелище с клубами дыма, с которыми должна легко справляться вытяжка. Одно неуверенное движение при засыпке серы - и она загорится прямо в ложке, которую вы можете, не заметив, опустить обратно в бутылку. Это опасно.
Возьмите ложку для помешивания и буквально вмесите в сплав горящую массу серы. Горящая сера может выплескиваться, если помешивающие движения слишком резкие, а это грозит сильными ожогами. Будьте осторожны. Рекомендую надеть защитные перчатки, очки и фартук.
В этот момент чернь будет иметь температуру в 650°С (1200°F). В определенный момент она будет иметь вид массы красного цвета, плавающей в горящей сере. Добавьте еще серы, но в меньшем количестве, и продолжайте помешивание. Сплав очень быстро насытится серой, и при последующем добавлении сера будет выгорать, лишь продлевая процесс плавки.
При помощи щипцов снимите тигель и, нагревая его горелкой, дайте выгореть остаткам серы. Подогревая тигель горелкой, вы тем самым поддерживаете чернь в расплавленном состоянии и сжигаете излишки серы.
В этот момент очень важно сделать несколько вращательных движений тиглем, чтобы слегка взболтать чернь. Таким образом, остатки свободной серы смогут отделиться и собраться в центре тигля на поверхности черни, образуя подобие шлака. Если на этом этапе чернь перегреть, шлак расплавится и соединится с жидкой массой. Это будет большой ошибкой, потому что шлак в данном случае способствует очищению, притягивая к себе компоненты, которые не участвуют в образовании черни. Шлак может составлять до трети общей массы черни.
Совершайте горелкой возвратнопоступательные движения, чтобы поддерживать температуру в тигле. Помогая студентам, я использую счет «раз», чтобы создать ритм в толчкообразных движениях горелки. Идея состоит в том, чтобы поддерживать чернь в жидком состоянии, не допуская ее перегрева. В конце концов, установление подобного ритма между огнем и металлом станет вашей второй натурой.
Если расплав станет слишком горячим, шлак в нем растворится. Если он станет слишком холодным, чернь нельзя будет вылить. Нужную температуру не так трудно поддерживать, хотя, несомненно, требуется црактика. Подойдите к изложнице и поднесите к ней тигель. Поддерживая температуру, достаточную лишь для текучести черни, наклоните тигель и тонкой струей вылейте расплав в изложницу. Не мешкайте, но в то же время не торопитесь, чтобы не расплескать чернь.
В большинстве случаев у вас получится стержень 25 - 50 см (10 -20 дюймов) длиной. Поставьте тигель на подставку и закройте крышку. Нагревая его до ярко красного цвета, расплавьте шлак до вязкой консистенции. Переверните его вертикально и вылейте остатки шлака, выскребая стенки шабером. Теперь тигель снова чист, разогрет и готов для приготовления следующей порции черни. Остатки черни, смешанной с флюсом, можно оставить для дальнейшего использования или экспериментов, если, конечно, вы склонны экспериментировать .
После того, как вы приготовили 3-4 порции черни, поломайте готовые стержни на части примерно.
2,5 см (1 дюйм) длиной. Вторая фаза процесса приготовления черни заключается в том, что вам нужно сплавить все куски черни вместе. Если у вас под рукой есть чистый тигель - это оптимальный вариант для достижения лучшего результата. Перед использованием покройте его флюсом. Чем чище тигель, тем лучше будет качество черни. Повторите процесс плавления, как описано выше, но, не добавляя ни металла, ни серы, ни флюса. Если появится небольшое количество шлака, не перегревайте расплав. Взболтайте чернь круговыми движениями и вылейте ее в изложницу. Теперь у вас получится дважды отлитая чернь исключительной чистоты: Splendid Rod!.
Наложение черни.
Для получения темного фона чернь можно наносить непосредственно на поверхность золота или серебра.
Слой черни толщиной 0,05 мм (0,002 дюйма) непрозрачен. При толщине.
0,012 мм чернь становится слегка прозрачной с коричневатым отливом. Техника чернения, пожалуй, наиболее часто используется при заполнении линий и узоров, выполненных путем гравировки, чеканки, штамповки, резьбы, травления, машинной обработки и литья.
Перед нанесением черни все процедуры по пайке изделия должны быть закончены. Поверхность под чернение должна быть очищена при помощи шлифовки с абразивом, отбеливания, пескоструйной обработки или электрохимической очистки; и офлюсована либо 25-50% раствором пасты «Handy Flux», либо 100% флюороном.
.
Порошковый метод.
При помощи пестика и ступки раздробите чернь на мелкие кусочки, песчинки или зерна в зависимости от того, какой размер вы предпочитаете. Смешайте порошок черни с флюсом до консистенции густой пасты и наносите ее на изделия при помощи небольшой лопатки или кисти. В печи можно обжигать плоские или практически плоские изделия, поскольку по законам гравитации в жидком состоянии чернь очень быстро стечет вниз.
.
Грифельный метод.
Удерживая стерженек черни рукой или при помощи пинцета, я нагреваю офлюсованное изделие до температуры, при которой флюс создаст ровное блестящее покрытие 600°С, (1100°F) . Данная температура с лихвой превосходит температуру плавления черни. Убрав пламя горелки в сторону, но, поддерживая изделие нагретым, я слегка касаюсь грифелем рабочей поверхности. При этом чернь плавится, проходит сквозь флюс и соединяется с очищенным металлом. Избыточное количество черни не только не повредит, но и часто является необходимым.
При нанесении черни на золото или серебро избегайте сильного перегрева или продолжительного нагревания изделия, поскольку в этом случае соединения серы с серебром начнут распадаться, сера выступит на поверхность, а серебро начнет образовывать в черни кристаллы самым непредсказуемым образом. В редких случаях образование дендритов (хлопьевидных кристаллов) в качестве декоративной отделки - желаемое явление, но в большинстве своем это нежелательное, причиняющее неудобства событие, которое приводит к удалению относительно больших кусков серебра там, где они уже соединились с поверхностью изделия. Чтобы иметь более или менее действенный метод контроля над подобным явлением, необходимо проводить специальные исследования. Вследствие перегрева на поверхности появляются белесые пятна, которые представляют собой следы серебра там, где ожидается более темный оттенок черни.
Когда чернь вытесняет расплавленный флюс, на поверхность изделия могут выступить капли флюса. С приобретением опыта их можно удалять либо самим черневым грифелем, либо стальным стержнем. Если это очень сложно, их можно удалить механически, когда изделие остынет. Капли флюса, имея сферическую форму, образуют кратеры и препятствуют формированию ровной поверхности. После их удаления необходимо нагреть изделие только для того, чтобы выровнять поверхность. Флюс также можно удалить и путем стандартной процедуры - отбеливания, после которой тщательно промойте изделие.
.
Окончательная обработка.
Излишек черни можно быстро снять при помощи обработки наждачной бумагой, шлифовки, опиловки или при помощи бормашины. Приведенные методы довольно агрессивны, и я предпочитаю более мягкие и медленные способы снятия излишков черни. Для плоских или слегка изогнутых поверхностей идеально подходит трехгранный шабер с остро заточенными краями. Он позволяет снимать очень тонкие слои и не оставляет частиц стали, как это происходит при использовании напильника. Помните, что черневые опилки при правильном хранении можно повторно использовать. Хотя для новых изделий я всегда готовлю новую чернь, собирая черневые отходы для дальнейших экспериментов по созданию более длинного бруска Splendid Rod.
После того, как излишки черни удалены, и начинает прорисовываться узор, я перехожу к другому участку, никогда не углубляясь дальше в рисунок. Данная процедура повторяется до тех пор, пока узор не станет просматриваться полностью.
При работе с изящной гравюрой я использую не шабер, а набор кремниево-углеродной абразивной бумаги, аккуратно удаляя чернь под струей теплой воды. Я редко использую абразивную бумагу грубее, чем №320, а постепенно перехожу от №400 к №600, чтобы создавать гамму оттенков: мягких, матовых, сероватых и шелковистых.
Машинная шлифовка значительно ускоряет процесс чистовой обработки, но создает массу проблем, устранение которых требует внимания и определенного мастерства. Чернь можно довести до идеального блеска при помощи одной лишь пасты Tripoli, которая, на мой взгляд, является оптимальным средством окончательной обработки. Я не рекомендую использовать пасту High Rouge. Поскольку машинная шлифовка будет снимать чернь быстрее, чем серебряную или золотую основу, будьте очень осторожны! Экспериментируйте в выборе средств окончательной обработки, чтобы определиться в последовательности их применения, которая больше вам подходит.
.
флюс чернь
Решение некоторых проблем
Проблема | Причина / Способ решения |
Раковины в готовом изделии | В идеальном варианте все оксиды должны быть удалены при помощи флюса и быстрого нагревания изделия при нанесении черни. Продолжительное нагревание или повторное сплавление могут существенно ухудшить условия. При помощи очень тонкого сверла удалите окалину, офлюсуйте поверхность и снова расплавьте чернь. |
Капли флюса остались под слоем черни | Изделие с самого начала не нагрето до необходимой температуры, в связи с чем флюс остается слишком твердым и для расплавленной черни. |
В черни появляются комки серебра | Недостаточное количество серы в черни или серьезный перегрев. |
Дендриты проявляются на поверхности во время чистовой обработки | Длительный перегрев изделия во время нанесения черни, который мешает соединении черни с металлом. |
Чернь выглядит бледной и имеет металлический блеск | Близко к условиям, описанным выше, но в данном случае дендриты более мелкие и более размыты по поверхности. |
После отливки, в черневом стержне появляется серебряное ядро, окруженное чернью хорошего качества | Ошибка в формуле при приготовлении, недостаточное количество серы или перегрев в процессе приготовления, либо расплав отливался при слишком высокой температуре. |
После отливки чернь становится серой и тусклой, особенно хорошо это заметно на отдаленном конце черневого стержня | Недостаточное количество серы при приготовлении расплава, слишком высокая температура при отливке, ошибка в формуле при приготовлении, превышение времени приготовления. |
При ближайшем рассмотрении нижняя поверхность черневого стержня покрыта тонким слоем серебряных гранул | Это не является серьезной проблемой, поскольку серебро не содержится внутри самого стержня. Просто осторожно соскоблите серебряную пленку. |
После полировки чернь отказывается становиться чистой и блестящей | Для полировки черни могут идеально подходить одни составы и совершенно не подходить другие. Попробуйте другое средство. |
При отливке чернь не образует ровный стержень | Это не совсем проблема качества, а скорее она заключается в неуверенности при отливке. Либо угол наклона изложницы слишком мал. |
Рабочее место, готовое для приготовления черни. Тщательность при его подготовке составляет разницу между успешной работой и неудачей.
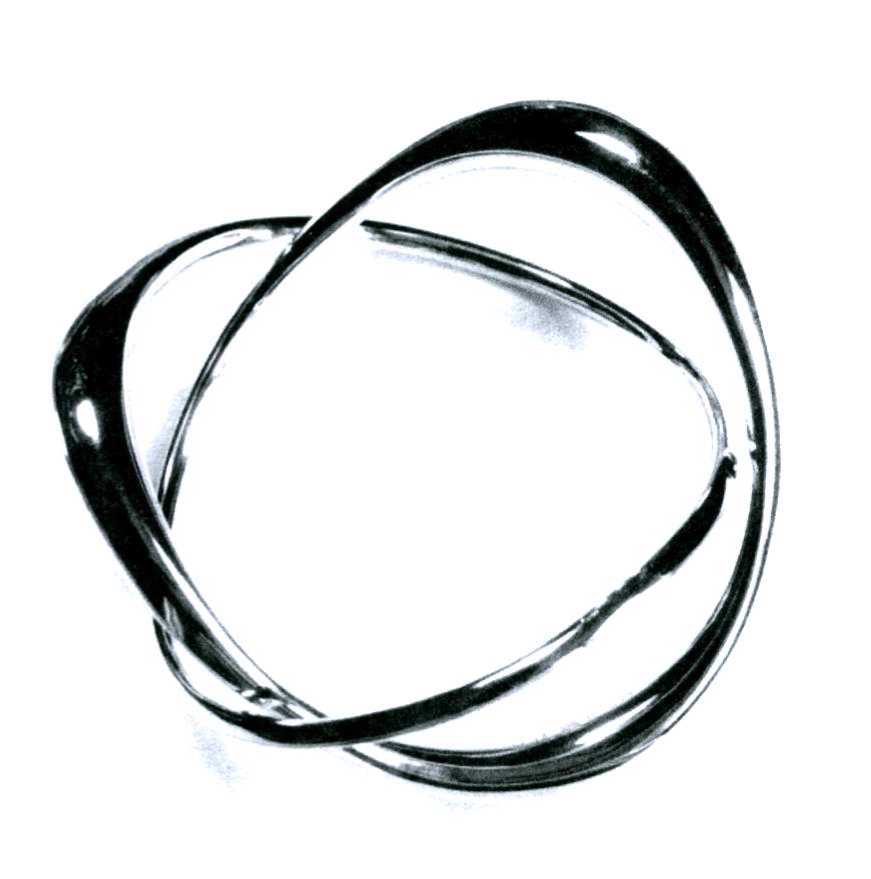
Антикластическая выколотка.
Долгое время формообразование листового металла представляло собой в основном синкластическое формообразование, при котором основные оси искривляются в одном направлении. Это логическая форма (так, например, вы сгибаете ладони, образуя пригоршню), а поскольку она имеет преимущества в практическом использовании, синкластика очень широко распространена.
Альтернативный способ выколотки, при котором основные оси изгибаются в противоположных направлениях, используется ограниченно, например, при изготовлении желобков, горлышек или рукояток. Только совсем недавно ювелиры обратили свое внимание на технику под названием «антикластическая выколотка», начав раскрывать широкий круг возможностей, которые она предоставляет.
Здесь я описываю и иллюстрирую только те формы, которые можно изготовить из одного листа металла. Для более полного представления о терминологии и технике антикластической выколотки я рекомендую изучить "Form Emphasis for Metalsmiths" автор Heikki Seppa (1978, Kent State University Press).
.
История.
Впервые я начал работать с тонколистовым металлом в 1968 году, пытаясь заняться изготовлением ювелирных изделий для, что называется, «поддержания штанов». В своих ранних работах я пытался использовать каждую технику, которую видел или о которой читал, экспериментируя в десятках различных направлений одновременно. Очевидно, что работы страдали от недостатка единой концепции. После неудачных попыток занять свою нишу на рынке я переплавил все свои изделия в лист металла. Получился рулон из листового золота 585 пробы.
(14 К) толщиной 0,36 мм (27 B&S). В этом есть своя доля иронии, но металл именно этой толщины я до сих пор использую в своих работах. Первоначально изделия того периода имели вид плоских объектов, вырезанных из этого листа и прокованных для придания формы и жесткости. Затем я начал экспериментировать, пытаясь одновременно придать жесткость и объем металлу.
Методом проб и ошибок я преуспел в технике по формированию полых форм из металла и создал на эту тему ряд ювелирных изделий. Именно в тот период времени знакомый ювелир рассказал мне о Хайки Сеппа, профессиональном ювелире и преподавателе, чья книга об образовании выпуклых форм готовилась к печати. Все следующее лето я провел в мастерской Хайки Сеппа (Haystack School, Maine), обучаясь мастерству и начиная строить дружеские отношения и профессиональное сотрудничество, которые продолжают оставаться наиболее важными аспектами моей карьеры.
Глоссарий.
.
Синкластика.
Процесс формообразования металла, при котором плоскому листу придается форма путем осадки краев и вытягивания центральной части. Основные оси данной формы изгибаются в одном направлении и образуют между собой равные углы. Лист металла, таким образом, принимает форму купола, полусферы.
.
Антикластика.
Процесс формообразования металла, при котором центр лист металла осаживается, а края вытягиваются. Основные оси данной формы изгибаются в разных направлениях, образуя между собой равные углы.
.
Осевая дуга.
Термин, используемый для описания воображаемой линии, которая проходит вдоль наковальни в процессе антикластической выколотки.
.
Формирующая дуга.
Другая воображаемая линия, описывающая окружность вокруг наковальни.
.
Синусоидальная наковальня.
Инструмент, обычно изготовленный из стали, дерева или пластика, используемый для поддержки металла в процессе формообразования. Ее можно купить, либо сделать самому. Термин происходит от латинского корня «волнистый, извилистый».
.
Хвостовой молоток.
Молоток или киянка с клиновидным бойком.
.
.
.
.
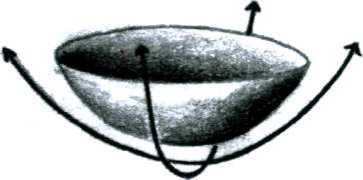
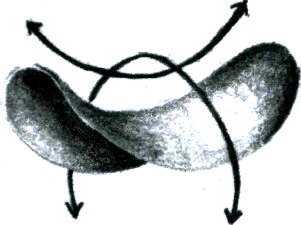
Антикластическая выколотка производится на синусоидальной наковальне, сделанной из дерева, твердого пластика или стали. Обычно пластиковая или деревянная киянка используется при работе на стальной наковальне и наоборот - стальной молоток используется при работе на деревянной или пластиковой наковальне. Стальная наковальня способствует быстрой деформации металла, но этот процесс сложнее контролировать. Поэтому нет ничего удивительного в том, что изделие при окончательной обработке требует дополнительной рихтовки (правки). Другими словами: экономия времени на формообразовании компенсируется потерей времени на дополнительной окончательной обработке. Соответственно, использование деревянной и пластиковой наковальни приводит к более медленному деформированию, но в то же время процесс выколотки легче контролировать, в некоторых случаях практически полностью избавляясь от необходимости править готовое изделие.
Инструмент подбирается в соответствии с размером заготовки. Размеры наковальни определяют пределы, до которых металл может деформироваться. Поперечный участок (поперечное сечение) наковальни в любой точке будет определять максимальный изгиб осевой дуги. Подобным образом, каждая синусоидальная впадина будет определять максимальный изгиб формирующей дуги. Ширина заготовки не должна превышать расстояния между двумя соседними вершинами синусоидальной наковальни. В любом случае радиус закругления киянки должен быть немного меньше радиуса соответствующей впадины синусоидальной наковальни. Это продемонстрировано на рисунках (см. верхний рисунок на стр. 35) .
Сторона клетки должна равняться 1,27 см (1/2 дюйма).
- увеличьте рисунок на 33%, чтобы получить лекало.
Киянка на рисунке слева и две верхние формы этой странице изготовлены из прочного пластика, например Delrin или нейлон. Молоток и синусоидальная наковальня - из стали.
Ход работы.
В качестве примера я описываю процесс изготовления веретенообразной конусной трубки с открытым швом («спикулум»), подобной той, что показана на рисунке. При изготовлении этой формы применяется все многообразие приемов формообразования и окончательной обработки, используемых в антикластике. Когда вы научитесь изготавливать спикулум, вы сможете экспериментировать с любыми другими формами и техниками. Для примера я описываю изделие по приведенной ниже развертке, которое изготавливается из металла толщиной.
0,36 мм (27 B&S). Приводимый мною пример предложен в качестве руководства к действию, но я надеюсь, что наиболее дерзкие мастера пожелают работать с произвольными формами. В любом случае, вам не помешает отслеживать и записывать изменения формы первого изделия. Таким образом, вы сможете его дублировать, если оно изготовлено правильно, и избежать повторения ошибок, если нет.
Вырежьте заготовку и обработайте края напильником, пока они не станут ровными и гладкими. Это важно, поскольку вы можете порезаться во время работы, и от этого будет зависеть внешний вид изделия. Симметрия не является необходимым параметром в антикластике, но мы начнем работу с симметричной фигуры. Отожгите, отбелите и высушите заготовку. Теперь вы готовы к началу работы.

Развертка для спикулума величину.
натуральную
Рабочее название данной формы -антикластический спикулум с открытым швом. В этой главе описывается изготовление этого изделия.
Заготовка располагается на наковальне таким образом, что между поверхностями образуется пустота. Начинайте работу с верхнего края.
.
Зажмите синусоидальную наковальню в тиски. Обогните наковальню отожженной заготовкой и уложите ее в углубление, так чтобы ее края плотно прилегали к уклонам. Крепко удерживайте заготовку за концы, чтобы она не распрямлялась при проковке. Удары киянки должны быть направлены в точку, расположенную немного ниже точки соприкосновения металла с наковальней. Таким образом, при ударе деформируется лишь небольшой участок заготовки. Постепенно перемещая заготовку вокруг наковальни, вы получите ровную канавку вдоль края.
Начинайте работать от края изделия по направлению к середине.
За редким исключением, когда этого требует дизайн изделия, необходимо внимательно следить за тем, чтобы удары киянки приходились под одним и тем же углом к наковальне. Если это условие не соблюдено, изделие будет выгибаться либо вправо, либо влево в зависимости от угла удара. Если изделие, подобное описываемому, имеет веретенообразную форму, то самые широкие его участки необходимо дольше подвергать обработке. Делайте столько проходов, сколько необходимо для получения ровного изгиба вдоль края изделия.
Во время работы важно удерживать концы заготовки.
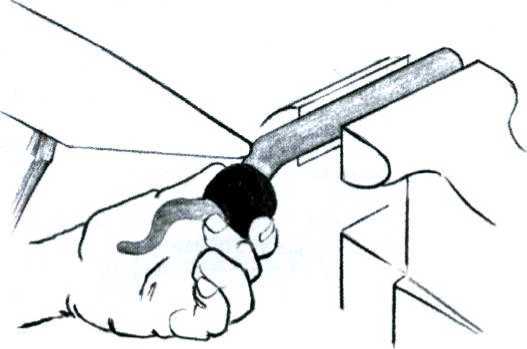
В процессе работы изделие перемещается вокруг наковальни, при этом удары киянки должны приходиться в одну и ту же точку наковальни.
Поверните заготовку на наковальне на 180 . Теперь непрокованный край изделия находится ближе к тискам. Повторяйте процесс формирования изгиба. Таким образом, вы завершаете первый этап формирования изделия.
Поместите заготовку на наковальню так, чтобы между ней и наковальней было пустое пространство, как показано на среднем рисунке. Направляйте следующую серию ударов слегка ниже точки контакта, поворачивая изделие, чтобы каждый последующий удар слегка перекрывал предыдущий. Проведите серию ударов, вращая изделие и создавая второй изгиб внутри первого. Снова поверните заготовку на 18 0° и повторите процесс на противоположном краю. Как и в начале, работайте по направлению к центру. Поскольку металл имеет свойство осаживаться, в процессе работы посередине заготовки будет образовываться выступ. При: попытке ускорить процесс проковки путем быстрого перемещения заготовки по наковальне с появляющимся выступом и образующейся складкой будет тяжело справляться. Если это все же происходит, отожгите изделие и возобновите работу, делая удары более мягкими и частыми.Продолжайте выколотку по этой схеме, постоянно направляя удары к центру, пока не завершите первый этап антикластическои выколотки. Помните, что удары молотка должны идти внахлест, перекрывая один другой. Осторожно отожгите ставшую жесткой в процессе работы форму. Температуру выбирайте в соответствии со сплавом, с которым вы работаете.
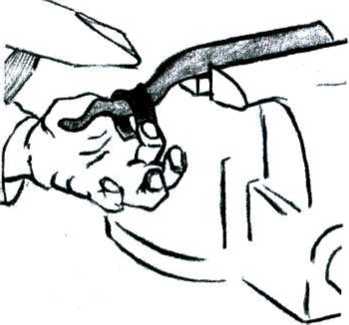
После первого прохода по одному краю по всей длине формы снимите ее с наковальни, переверните, поместите на наковальню в нужную позицию и повторите процесс.
В процессе работы над вторым краем изделия по центру будет образовываться округлый выступ. Его необходимо выровнять и смягчить перед следующими этапами работы.
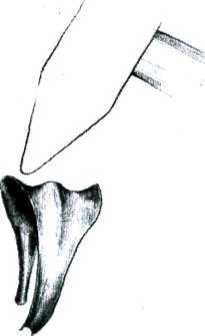
Чтобы начать второй этап работ, форму размещают на наковальне, как это было в начале. Если сжимать изделие по осевой дуге, формирующая дуга будет распрямляться. Поэтому получится так, что ваша красиво сомкнутая форма разомкнулась. Да, это случилось, но не стоит отчаиваться! Если исчерпаны возможности по формовке на данном изгибе наковальни, возможно, есть необходимость переместиться на более узкую/крутую впадину. За исключением особых случаев, обычно требуется два прохода молотком по каждому краю заготовки прежде, чем перейти к следующему изгибу на наковальне. Вы можете продолжать работать на стальной наковальне или перейти на пластиковую. Попробуйте оба варианта, чтобы определиться, что вам подходит.
Продолжайте поочередно работать по каждому краю, перемещая удары от края по направлению к центральной линии.
.
Продолжайте работу до тех пор, пока заготовка не приобретет желаемую форму. Простучите хвостовым молотком внутри образовавшейся впадины, всегда удерживая концы сомкнутыми для того, чтобы предотвратить распрямление металла. Поместите заготовку на наковальню, чтобы под ней в месте нанесения удара молотком было свободное пространство. Помните, что синусоидальную наковальню можно перевернуть и использовать изгибы с другими радиусами.
Прокованное изделие имеет несколько замечательных свойств.
Его конструкция достаточно прочна, но изделие, тем не менее, можно легко растянуть в двух направлениях, и оно свободно скручивается вокруг своей оси. При «скручивании» и «раскручивании» изделия по осевой дуге оно раскрывается, а по формирующей -закрывается.
Методично скручивая и сгибая заготовку, синусоидальную форму можно поворачивать практически в любом направлении. Вогнутая сторона спикулума всегда останется с внешней стороны дуги, придавая форме устойчивость и определенность. Если антикластическую форму сгибать вдоль оси, ось укорачивается, а формирующая дуга распрямляется.
Если выбрано конкретное направление, обычно после первого этапа работы, заготовка возвращается на наковальню для последующей проковки. Не забывайте поддерживать заготовку до тех пор, пока не получена желаемая форма. Если изделие в процессе работы принимает нежелательную форму, снимите его с наковальни и руками придайте желаемую форму. Очень важно внимательно следить за процессом формообразования, чтобы вовремя остановить и исправить отклонения от желаемой формы. Процесс может быстро выйти из-под контроля!.
Наиболее частая проблема, возникающая у людей, которые изучают антикластическую выколотку, состоит в том, что в процессе работы изделие слишком быстро перемещается. Я не могу переоценить важность достижения гладкой равномерной и плавной кривизны в нижней части впадины, прежде чем переходить к окончательному формованию краев. В антикластике просто не существует быстрых способов получения гладких линий и аккуратно выполненных изделий, равно как нет способов скрыть небрежную работу. Не торопитесь, делайте все очень аккуратно, прежде чем перейти к окончательной обработке. При выглаживании металлическая поверхность становится ровной и гладкой. В нашем случае это означает, что изделие находится между пластиковой наковальней и стальным молотком, при этом молоток выполняет роль гладилки. Само собой разумеется, что для достижения желаемого результата рабочие поверхности молотка и наковальни должны быть тщательнейшим образом отполированы.Когда изделие готово к заключительной стадии обработки, в самой широкой его части сечение имеет форму незамкнутого овала, а края изделия смыкаются строго над центром. В процессе придания формы края изделия закругляются и смыкаются, а сечение принимает форму окружности. Если после первичной проковки сечение имело форму разомкнутой окружности, в процессе окончательного придания формы оно примет форму овала. Зажмите в тисках кольцевой ригель или хорошо отполированный бородок в горизонтальном положении. Если вы хотите, чтобы все, кто на него напорется, вспоминали вас добрым словом, после окончания работы оставьте ригель в тисках. Поместите изделие на ригель так, чтобы в месте соприкосновения между поверхностями ригеля и формы не было зазоров. Расположение изделия на ригеле очень важно, поскольку зона соприкосновения очень мала. Правильное положение формы на ригеле показано на следующей странице, как раз в момент окончательной обработки изгиба. Чувствуйте металл и действуйте по наитию. Центральные участки спикулума правьте у основания ригеля, где диаметр наибольший, постепенно перемещаясь к его концу для правки суживающихся частей. Не забывайте вращать изделие вокруг ригеля во время работы. Продолжайте работу, продвигаясь очень медленно, до тех пор, пока края спикулума не сомкнутся, образуя аккуратный ровный гладкий симметричный шов по всей длине изделия.

А.
.
Перед началом заключительной стадии обработки поперечное сечение в центральной части должно иметь форму овала (А). Если в этот момент оно имеет форму круга (В), то после смыкания краев спикулум приобретет овальную форму.
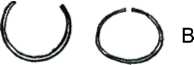
Округлые поверхности молотка и ригеля создают минимальную зону контакта со спикулумом. Необходимо нанести удар по касательной именно в ту точку, которая «закроет» шов.
Работая на стандартном кольцевом ригеле, сжимайте края спикулума, чтобы «закрыть» форму.
.
.
В связи с тем, что для придания изделию окончательной формы, где края должны быть плотно сомкнуты, площадь контакта изделия с опорой должна быть минимальной. Поскольку изделие касается боковой поверхности ригеля, в процессе обработки его форма сохраняется только благодаря естественной жесткости и упругости металла. Любой неосторожный удар по отожженному спикулуму может привести к плачевному результату. Огромное внимание необходимо уделять тому, чтобы удар направлялся в точку, которая располагается именно над местом соприкосновения поверхности изделия и ригеля.
Теперь вам практически ничего не стоит от антикластики перейти к синкластике, где металлический лист проковывается вдоль осевых линий, которые изгибаются в одном направлении, или в целом к процессу, который называется «свободная выколотка».
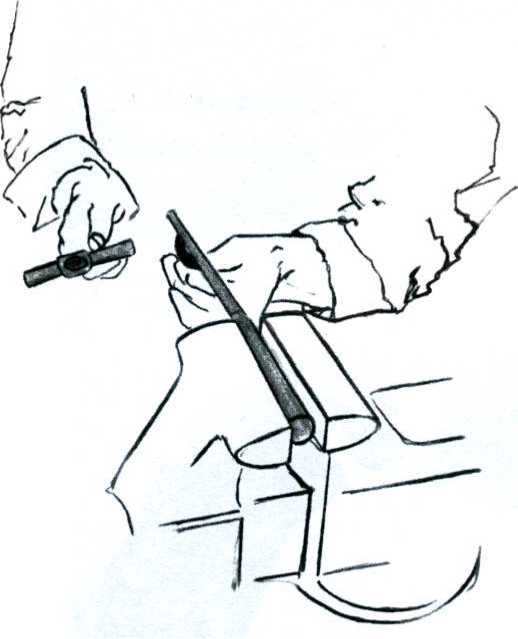
Резюме.
Частично красота изделия, выполненного в технике антикластической выколотки, зависит от способности мастера из небольшого количества материала создать жесткую конструкцию. Это означает, что в выколотке можно использовать не только благородные, но и другие цветные металлы.
Принципы антикластического формообразования могут быть применимы как к большим, так и к малым формам, поэтому размеры ваших изделий могут ограничиваться лишь размерами инструментов и вашей сноровкой при работе с материалом. Сочетание антикластической и синкластической выколоток создает огромный простор для творчества в создании моноформ.
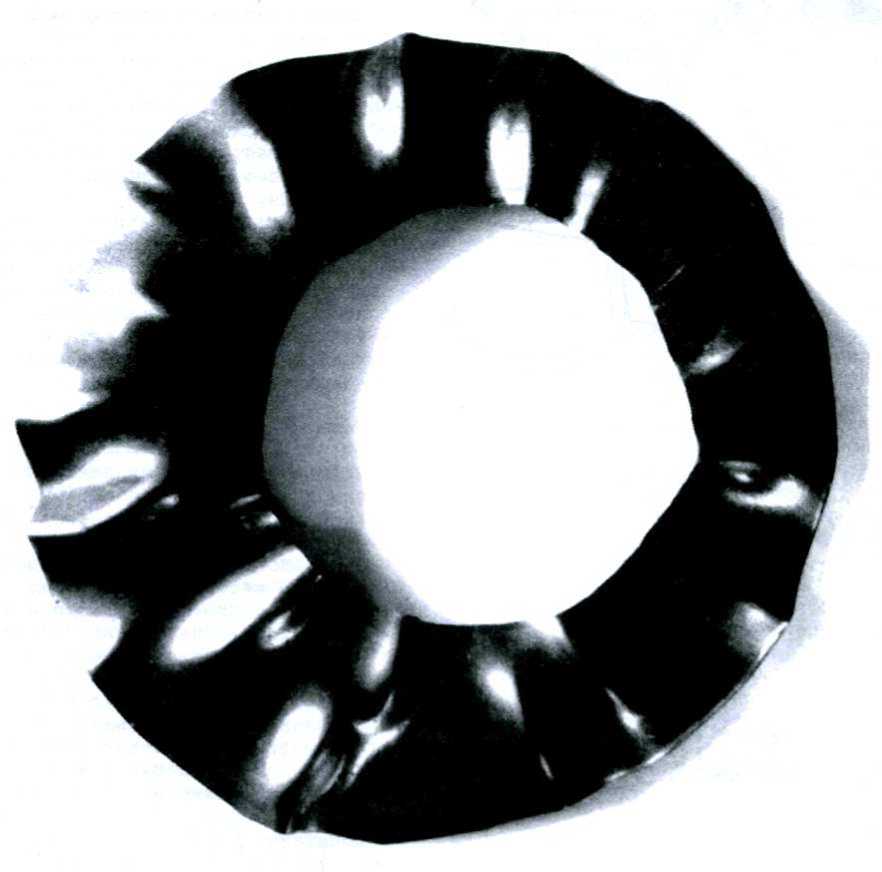
Одночастные пресс-формы.
Штамповка это древний прием, которым пользовались разные народы на протяжении всей истории человечества. Этрусские и греческие ювелиры, например, применяли штампы для изготовления повторяющихся составных частей серег и цепочек. Они вырезали формы в бронзовых пластинах и вбивали в них тонкие золотые листы, подкладывая под молоток толстый листовой свинец. Используя ту же идею, я заменила бронзу на гравированную акриловую форму, свинец - на уретан, а давление создала при помощи гидравлического пресса. Использование мной односторонних пресс-форм является развитием старых приемов в сочетании с технологией XIX и материалами XX века. Удивительно, но гидравлические прессы, очень похожие на те, что я описываю в этой статье, использовались еще до 1850 года.
Я начала применять штамповку в 1978 году, вскоре после того, Марк Пейсин описал этот процесс в Goldsmiths Journal (VIII, №6, декабрь 1977). Его исследования базировались на технологии применения мазонитовых штампов, разработанной Ричардом Томасом в Кренбрукской Академии, и на работе, проделанной Рут Жирард в Калифорнийском университете в Беркли. Как художник я любознательна, а как специалист по работе с металлами - люблю инструменты и работу руками.
Большая часть из того, что я знаю о штамповке, было выяснено путем проб по принципу «а что, если» и последующим обдумыванием, как можно применить полученные результаты. Обучающие семинары по штамповке позволили мне учиться на ошибках и успехах других мастеров. В 1990 году я начала работать с Ли Маршалом, инженером и изобретателем, который сконструировал малый гидравлический пресс. Он создал компанию «Bonny Boon» для разработки и производства инструментов для штамповки и продемонстрировал возможности этой технологии широкому кругу людей.
Эта деятельность привела к удивительному росту количества изобретений и открытий в этой области.
Введение.
Пресс-форма применяется для тех же целей, что и молоток, стойка, пуансон или инструмент для чеканки, но заменяет мускульную силу на гидравлику, а многочисленные удары молота - на плавное выдавливание изделия. Штамповка это простой, эффективный и быстрый процесс, который меняет сложившееся мнение о том, что работа по металлу требует много времени, упорства, сноровки и физической силы. Процесс штамповки позволяет мастеру напрямую и в полной мере использовать пластические свойства металла.
Штамповка позволяет воспроизводить много раз один и тот же объект, но это только одна из возможностей этого приема. Важно помнить, что пресс - формы это инструменты, а не просто шаблоны для производства одинаковых предметов. Форма и особенности штампа работают по тому же принципу, что и молоток или стойка, которые оставляют свои особые отпечатки на заготовке, а конечный результат зависит от мастерства исполнителя. Штамповка позволяет придать изделию объем, и поскольку объемные изделия конструкционно прочнее плоских, можно использовать более тонкий металл. А это позволяет, в свою очередь, изготавливать ювелирные изделия меньшего веса, одновременно улучшая их потребительские качества и снижая затраты на производство. Штамповка менее травматична для металла, чем ковка, потому что давление равномерно распределено по всей поверхности. Это позволяет изготавливать изделия из мокуме или биметаллов с меньшим риском расслоения. Подобным же образом, металл, декорированный прокаткой в вальцах и травлением, может быть отштампован без повреждения поверхности. В любом случае, штампованный металл гладкий и на нем нет следов от молотка.
Приемы, описанные здесь, рекомендуются для цветных металлов. Медь, стерлинговое серебро, чистое серебро, пьютер и алюминий легко формуются. Желтое золото и латунь тоже подходят для этого, как и титан и ниобий. Более жесткие металлы как нейзильбер и бронза лучше не применять.
.
Штампы.
В гидравлических прессах могут бьть использованы обычные пробойники, но для формования полусферических форм, тиснения и сгибания деталей годятся самые разнообразные инструменты. В прессе можно также использовать вырубные и обжимные штампы.
Двучастные пресс-формы состоят из двух точно соответствующих друг другу верхней и нижней частей, между которыми формуется металл. Иногда без них не обойтись, когда требуется получить сложные формы. Такие пресс-формы могут быть изготовлены в домашних условиях из материала XX века Devcon, который представляет собой эпоксидную смолу со стальной стружкой в качестве наполнителя. Подробную информацию относительно таких пресс-форм и материалов можно найти в упомянутой выше статье Марка Пэйсина в Goldsmiths Journal, в моей статье "Hydraulic Die Forming for the.
Artist/Metalsmith", Metalsmith, Summer 1985, или в моей книге Hydraulic Die Forming for Artists am. Metalsmiths.
Одночастные пресс-формы, применяемые вместе с уретаном, открывают многочисленные возможности в творчестве. Поскольку весь штамп состоит лишь из одной части, такие пресс-формы дешевле и проще в изготовлении, чем двучастные. Кроме того, они обеспечивают разносторонность применения. В следующем разделе описывается оборудование, необходимое для штамповки, и даются инструкции по изготовлению и использованию трех типов штампов, состоящих из одной части (одночастных): пуансонов, матриц и рельефно-формовочных штампов.
Каркасный пресс.
Многие из прессов первого поколения с рамами из сварной стали, сделанные в 7 0е годы XX века, все еще используются. Их рамы изготовлены из L- или U-образного стального профиля, с подвижными плитами, или срединной плитой, которая покоится на поршне, расположенном внутри цилиндра, приваренного к станине пресса.
Очень важно, чтобы поверхности плит были гладкими и параллельными. Возвратные пружины облегчают работу с прессом.
В 197 9 г. Робин Касади после консультаций с механиками и уточнения технических характеристик конструкции, рассчитанной на давление в 2 0 тонн, сконструировал сборный пресс. Одно важное преимущество этого пресса (помимо того, что не требуется быть сварщиком, чтобы его изготовить)-это то, что он может быть отрегулирован по высоте, что позволяет варьировать размеры изделий. Стоимость этого пресса зависит от поставщика деталей и от доли работ по его сборке, которую вы сможете произвести самостоятельно. По причине того, что для плит требуется достаточно много стали, а также за счет стоимости сверления плит, расходы могут вылиться в приличную сумму. Пресс Bonny Doon состоит из сварной рамы из 5 0-миллиметрового (2-дюймового) квадратного стального профиля и стальных плит размером 150*150*25 мм (6*6*1 дюйм). Мощные пружины, установленные внутри профиля, обеспечивают как самовыравнивание конструкции, так и «возврат». Это компактная, безопасная и эффективная конструкция для работы в мастерской. Пользоваться недорогими прессами, которые можно приобрести со скидкой у распространителей, не рекомендуется. Они неоправданно большие, зачастую недостаточно мощные, требуют существенных модификаций, не снабжены манометрами и часто ломаются.
Пресс Bonny Doon с автомобильным (бутылочным) домкратом.
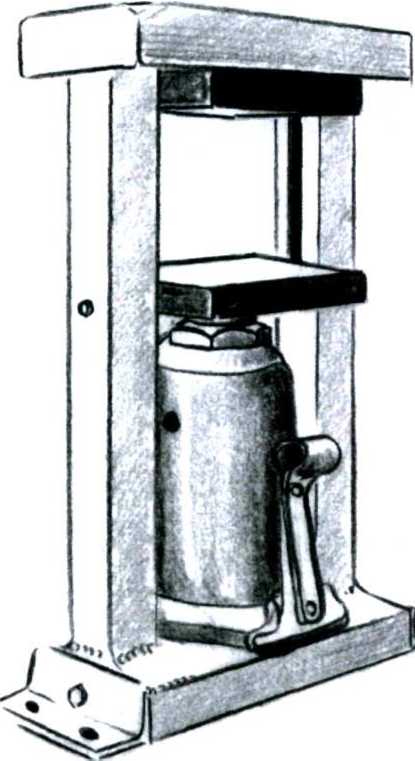
Мощность.
Давление в штамповочном прессе обеспечивается стандартным гидравлическим 2 0-тонным автомобильным (иногда называемым бутылочным домкратом), который можно приобрести в автомагазинах. Домкраты мощностью 10 тонн подходят для некоторых пресс-форм, но одночастные пресс-формы требуют мощности в 20 тонн. Настоятельно рекомендуется дополнительное устройство в виде манометра, которое позволяет измерять развиваемое усилие, контролируя процесс и стабильность результатов.
Альтернативной гидравлической системой является раздельная система, состоящая из гидравлического цилиндра и двухступенчатого насоса с манометром, соединенных между собой шлангом высокого давления. Эту конструкцию также можно собрать из деталей, которые продаются в автомагазинах. Это оборудование несколько более дорогое, но с двухступенчатым насосом легче работать.
Третья альтернатива - это использование сжатого воздуха в качестве привода для насоса. Эта система рекомендуется для серийного производства и для тех, кому нужен процесс, не требующий приложения-физической силы. Давление воздуха может быть использовано для точного воспроизведения, кроме того, временные показатели в этом варианте уменьшаются, по сравнению с ручной накачкой.
.
Уретан.
Уретан - это плотное резиноподобное вещество. Используемое вместе с одночастными пресс-формами, оно становится под давлением второй частью штампа. В отличие от резины, которая сжимается и изнашивается в процессе использования, уретан растекается под давлением, равномерно распределяя его по поверхности без эффекта удара в момент соприкосновения. После использования он возвращается к первоначальной форме и может быть использован вновь тысячи раз. Изношенный внешний вид материала после продолжительного использования не влияет на качество процесса. Резиновые листы или блоки могут быть использованы в одночастных пресс-формах, но результаты будут непредсказуемыми и менее выразительными, к тому же резина склонна к быстрому изнашиванию.
Я считаю, что неплохо иметь набор из нескольких уретановых подкладок и блоков разных размереров, толщины и жесткости. Жесткость измеряется в дюрометрах и для уретана она находится в промежутке от 95 (самый твердый) до 80 (более мягкий) дюрометров. В общем, уретан жесткостью 95 применяют для штамповки, в то время как 8 0-ый рекомендуется для чеканки и более тщательной проработки деталей.
Поскольку уретан «растекается» под давлением, то при использовании с пуансонами он обычно находится в контейнере с крепкими стенками, к что он заполняет пространство вверху и вокруг пуансона. Контейнер выглядит следующим образом: отрезок стальной трубы с толщиной стенки 6 мм (1/4 дюйма) заполняется уретаном так, чтобы до верхнего края оставалось 12 мм (1/2 дюйма). Диаметр трубы подбирается в зависимости от размеров изделия. Обычно такие контейнеры не имеют дна. Для развития наибольшего давления, позволяющего проработать, максимум деталей, используйте контейнер с дном. Контейнеры обычно заполнены уретаном жесткостью 95, но, когда требуется предельно четкая проработка деталей, используется уретан 80.
Уретановые подкладки изготавливаются из уретана жесткостью от 8 0 до 95 дюрометров и толщиной от 1,5 мм (1/16 дюйма) до 25 мм (1 дюйма) . Они используются, когда штамп не подходит по размеру к контейнеру.
С такими подкладками обычно используются матричные пресс-формы. Толщина используемой подкладки зависит от глубины и размера пресс-формы. Большие формы, в которых желательна глубокая штамповка, требуют более толстыхподкладок. Самые тонкие подкладки используются для тиснения.
Раньше для изготовления таких подкладок и блоков предлагался к использованию самополимеризующийся двухкомпонентный наливной уретан Flexan (Флексан). Но, поскольку, недавно было установлено, что этот материал опасен, его нельзя рекомендовать к работе. Опасность проявляется во время его смешивания и полимеризации. Даже противогазы не обеспечивают необходимой защиты. Готовые подкладки из Флексана не представляют опасности. Этот материал всегда следует резать ножницами или острым ножом.
.
Никогда не нагревайте, не обрабатывайте на абразивном круге, не сжигайте, не шлифуйте и не распиливайте никакие виды уретана, поскольку выделяются опасные испарения.
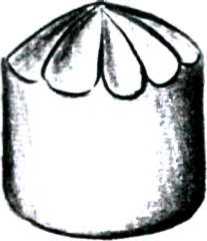
Типовой пуансон, вырезанный из акрила
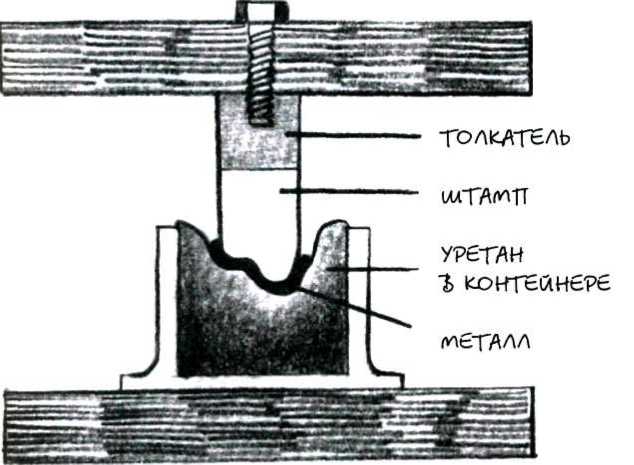
Штамп вдавливается в уретановую подкладку, которая растекается вверх и вокруг него. Уретан помещен в цилиндр с приваренным дном. Заметьте, что толкатель привинчен к верхней плите пресса болтом.
Пуансоны.
Пуансон (иногда называемый «папа») представляет собой инструмент, который давит на металл и вдавливается в него для придания ему требуемой формы. Это обычно «позитив» требующейся формы, как показано на рисунке внизу. Уретан в контейнере является другой частью пресс-формы.
Из литого акрилового (Acrylite, Plexiglas, Lucite) стержня получается удивительно хороший штамп. Акрил вполне доступен, недорог и легко обрабатывается, а так же способен выдерживать статические нагрузки до 130 кг/см
(1800 фунтов на квадратный дюйм). В случаях, когда на пуансоне есть острые детали или намечается длительное использование, я рекомендую использовать Delrin, более прочный и дорогой материал. Какой бы материал вы не взяли., торцы стержня должны быть параллельными и срезаны под углом 90° к оси. Я рекомендую длину в 25 мм (1 дюйм). Самому трудно отторцевать заготовку аккуратно, поэтому я рекомендую, чтобы резка выполнялась поставщиком.
Акрилу можно придавать форму с помощью грубых напильников или резать его фрезами при помощи бормашины. Когда работаете с акрилом, надевайте респиратор и защитные очки, а также избегайте обработки на большой скорости. Если акрил становится липким или издает резкий запах горящего пластика, вы его перегрели, поэтому необходимо уменьшить обороты и давление. Продукты разложения, возникающие при нагреве, могут быть опасны. Соберите пылесосом всю пыль сразу же после окончания работы. Когда вы вырезаете штамп, начните с черновой формы. Слишком глубокие спилы и поднутрения вызовут разлом штампа. Острые углы могут разорвать металл прежде, чем он примет форму.
По мере образования формы делайте оттиски со штампа, контролируя ход своей работы. Пуансоны -это детали для формовки и поэтому контуру детали надо уделять особое внимание. Текстура также может быть частью дизайна, но она будет просматриваться только при использовании тонких листов металла (0,33 мм (28 B&S) или тоньше).
Другие материалы, использующиеся для изготовления штампов: торцевые спилы твердых пород дерева, никель, латунь, алюминий и сталь. Штампы могут быть вырезаны, составлены из частей или отлиты. Выбор материала для штампа будет зависеть от его размера и сложности, материала изделия и необходимого количества дубликатов. Не используйте хрупкие материалы, которые могут дать сколы, а также штамм не должен быть высоким.
Высота в 25 мм (1 дюйм) , рекомендованная для акриловых штампов, подходит также для других материалов. Поскольку штампы вдавливаются в контейнер со стальными стенками, в случае поломки они там и останутся.
Для работы со штампом выбирайте такой уретановый блок, диаметр которого близок к диаметру пуансона. Пуансон может быть прикреплен к верхней плите пресса несколькими способами. Он может быть привинчен непосредственно к.
верхней плите или установлен и зафиксирован при помощи двустороннего скотча. Поскольку уретан не заполняет весь контейнер, может потребоваться спейсер (толкатель), удлиняющий пуансон для погружения его в уретан. Я обычно изготавливаю пуансоны высотой 25 мм (1 дюйм) и прикрепляю их с помощью двухстороннего скотча к толкателю, который прикручен к верхней плите пресса.
Всегда работайте с отожженным металлом. Металлическая заготовка должна быть меньше штампа. При использовании заготовки большего размера, она будет заворачиваться на штамп (как пивная крышка на бутылку) и ее будет трудно снять. Это будет препятствовать вдавливанию рельефа штампа в металлическую пластину, что будет причиной плохой проработки деталей, То, насколько хорошо пропечатаются детали на поверхности изделия, зависит от толщины используемой металлической заготовки: чем тоньше металл, тем больше деталей. Чтобы максимально проработать все детали можно использовать несколько приемов. Первый из них - это отжиг с повторной прессовкой. Формируемая заготовка может быть зафиксирована на штампе липкой лентой. Другой способ максимально проработать отпечаток - это использование стального контейнера с дном. Контейнеры обычно наполняют уретаном жесткостью 95 дюрометров, а контейнеры с дном - уретаном 8 0, которые используются для оттиска более мелких деталей. В ходе работы ведите записи для каждого образца, чтобы при необходимости воспроизвести результаты.
Работая с пуансоном в прессе, вы можете наблюдать за тем, как идет процесс. Пуансон будет опускаться в контейнер, погружаясь в уретан и вдавливая в него заготовку. Вы можете опустить пуансон в контейнер на 2/3 глубины (если у него есть дно). Если контейнер не имеет дна, остановитесь, когда уретан начнет выдавливаться наружу снизу, потому что это означает, что вы достигли максимального давления внутри контейнера.
Матричная пресс-форма.
Матричная пресс-форма (матрица) также может быть названа контурным штампом, так как она представляет собой просто пластину из материала, в которой вырезано отверстие, соответствующее контуру изделия. Матричная пресс-форма - нижняя половина штампа; деталь, внутри которой изделию придается форма. Когда уретан используется с матричной пресс-формой, он выполняет роль пуансона. Концептуально матричная пресс-форма похожа на мазонитовые штампы, которыми пользуются мастера многие годы. В этом случае, однако, нет необходимости прикреплять металлическую заготовку к пресс-форме или использовать молоток или пунзель для формовки металла. Пресс «прижимает» заготовку к штампу, а уретан равномерно вдавливает и вытягивает металл в имеющееся отверстие без придания ему какой-либо фактуры. Результатом является гладкая форма, напоминающая подушечку, с плоским фланцем и четким контуром
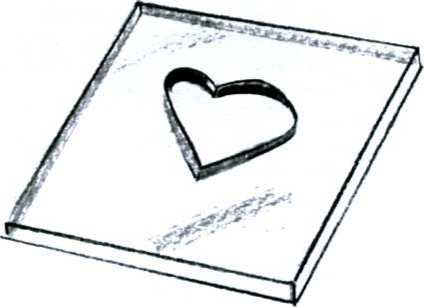
Матрица.
Эти детали могут быть изготовлены из пластика, стали или алюминия.
В матричной пресс-форме уретан берет на себя функцию пуансона, вдавливая металл внутрь формы. Обратите внимание на использование многослойной матрицы для увеличения глубины продавливания.
Мазонит, дерево и алюминий всегда использовались для изготовления этих пресс-форм, но я предпочитаю листовой акрил, потому что его легче резать, он недорог и более долговечен. Стальная или латунная пластина, установленная с лицевой стороны формы, позволяет использовать эту пресс-форму сотни раз. Можно купить листы акрила различной толщины, но я считаю, что наиболее практичной является толщина в 6 мм (1/4 дюйма), так как такие пластины дешевле, легко режутся, и из них можно составить несколько слоев, чтобы получить необходимую глубину штампа. Большие пластины можно разрезать на маленькие, более удобные в работе при помощи ножовки, это может сделать и поставщик пластика. Можно также купить обрезки на вес. Если вы можете позволить себе первоначальные вложения, создайте запас из квадратиков необходимых размеров. Очень удобно просто взять с полки заготовку и приступить к работе.
Чтобы определить оптимальную толщину для штампа, измерьте самую широкую часть вырезаемого вами контура изделия, Чем шире изделие, тем глубже вы можете продавить рельеф и тем толще должна быть пресс-форма. В следующей таблице отражены основные соотношения размеров.
Ширина контура | Толщина | |
матричной | ||
пресс-формы | ||
2 5 мм (1 дюйм) | 6 мм | (Н дюйма) |
38 мм (1 % дюйма) | 9 мм | (3/8 дюйма) |
50 мм (2 дюйма) | 12 мм | (% дюйма) |
63 мм (2 % дюйма) | 19 мм | (% дюйма) |
Отцентрируйте рисунок на пластине и оставьте поля шириной, по меньшей мере, 19 мм (3/4 дюйма) вокруг контура изделия. Без такой кромки матричная пресс-форма, скорее всего, сломается, особенно, если в дизайне присутствуют углы, как на рисунке. Если припуск будет шириной в 25 мм (1 дюйм) и более, это даже лучше. Я режу листовой акрил ювелирным лобзиком со спиральной пилкой. Поскольку эти полотна оставляют неровный край и в процессе распила их трудно контролировать, производите распил рядом с линией, а не по ней, а затем опилите на нужную глубину. Важно, чтобы верхний край был выпилен чисто, и чтобы внутренние стенки контура не имели поднутрений с лицевой стороны и были вертикальными. Степень окончательной обработки не имеет значения.
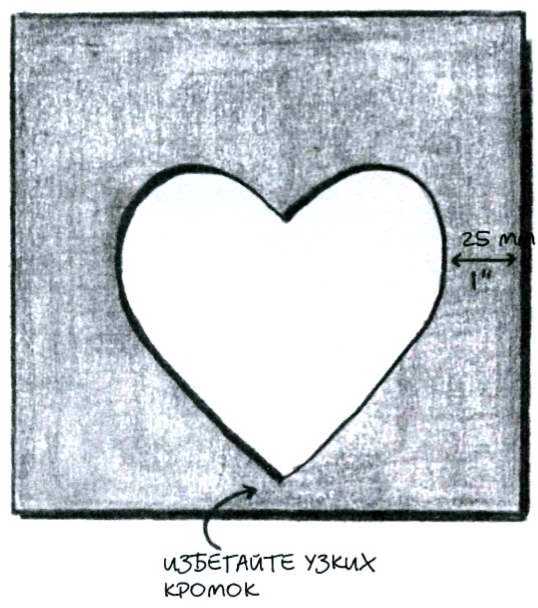
Обычно я оставляю около 25 мм (1 дюйма) материала вокруг вырезанного контура изделия. Не располагайте углов рядом с краем пластины, как нижний край сердца на рисунке.
«Плоское дно».
Решение проблемы-более толстая матричная пресс-форма.
Если вы хотите составить матричную пресс-форму из нескольких слоев акрила каждый толщиной 6 мм (1/4 дюйма), просто вырежьте первый силуэт, а затем перенесите его чертилкой на следующую пластину. Полного совпадения не требуется, но не допускайте поднутрений, так как они вызовут разлом пресс-формы.
Акрил обладает высоким пределом прочности при сжатии, но он хрупок, и треснет и разрушится, если снизу он не будет надежно опираться на что-либо. Слои могут быть склеены друг с другом акриловым клеем, но двухсторонний скотч держит ничуть не хуже. Конечно, количество слоев можно увеличить в любое время, поэтому вспомните об этом приеме, если при формовке у изделия появится «дно» от соприкосновения с плитой пресса.
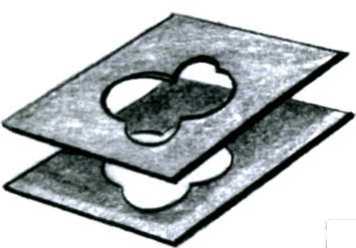

Латунные наружные пластины, которые были пропилены и обточены в соединенном виде, обеспечивают точное совпадение поверхностей двусторонней матричной пресс-формы.
Одно из направлений применения штамповки - изготовление в точности повторяющих друг друга «половинок», которые могут быть соединены вместе, образуя полое внутри изделие, такое, как бусина или небольшой контейнер. Если контур идеально симметричен, края двух полученных деталей, приложенные один к другому, совместятся, но если дизайн асимметричен, то получится зеркальное отражение.
Если вы вырежете форму электролобзиком или на фасоннофрезерном станке, вы можете добиться того, что стенки матрицы будут строго вертикальными. Поэтому контуры с обеих сторон формы будут представлять собой совпадающие зеркальные отражения. Тогда вы сможете продавить металл сначала с одной стороны заготовки, перевернуть матрицу и продавить деталь с другой стороны, и тогда «половинки» образуют вместе как бы раковину моллюска.
Еще один способ сделать двустороннюю матричную пресс-форму.
- это изготовить две матрицы с полностью повторяющимся на лицевых поверхностях рисунком. Склейте две латунных пластины толщиной 1,2 9 мм (16 B&S) или стали толщиной 0,8 мм (1/32 дюйма) между собой и аккуратно выпилите рисунок. Опилите так, чтобы края образовывали между собой угол в 90°, а потом разделите пластины. Затем вы можете изготовить одну двустороннюю пресс-форму или пару пресс-форм, используя поверхности, которые были склеены как лицевые поверхности одной матричной пресс-формы. Металлические пластины можно приклеить или прикрепить двусторонним скотчем. И, конечно, вновь проверьте, чтобы на акриле не было поднутрений.
Для работы с матричными пресс-формами используется металл толщиной от 1,02 мм (18 B&S) до.
0,33 мм (28 B&S). Толщина выбираемой заготовки определяется тем, до какой степени надо продавить металл. Как и прежде, не забывайте помечать каждый образец, записывая, как он был получен. Глубокие пресс-формы (с широким контуром) требуют более толстого металла. То, для чего будут использоваться изготовленные на пресс-форме детали, также должно учитываться при определении необходимой толщины заготовки. Поскольку фланец добавляет жесткости конструкции, то можно использовать более тонкий металл, если известно, что в готовом изделии он (фланец) будет сохранен. Если парные части должны быть соединены вместе без сохранения фланца, используйте металл достаточно толстый, чтобы образовалась пригодная для пайки кромка.
Заготовки для работы с матричной пресс-формой должны быть на 12-19 мм (1/2 - 3/4 дюйма) шире контура изделия. Это создаст фланец в 6-9 мм (1/4 дюйма) шириной вокруг детали. Матричные пресс-формы обычно используются с уретановыми подкладками жесткостью 95 дюрометров. Толщина уретановых подкладок пропорционально зависит от ширины и объема изделия. Подкладка в 25 мм (1 -дюйм) должна использоваться для выдавливания глубокой и большой формы, а в 6 мм (1/4 дюйма) - для неглубоких и маленьких изделий.
Подкладки жесткостью 8 0 дюрометров также используются с матричными пресс-формами, но вы должны быть осторожны потому, что более мягкий уретан легче растекается, и процесс формовки будет проходить быстрее. Металл может быть вдавлен в форму до того, как фланец будет надежно зажат на месте. Это может вызвать повреждение краев пресс-формы, так как металлическая заготовка будет скрести по краям. Чтобы избежать этого, я советую использовать подкладки жесткостью 95 дюрометров.
в начале формовки, а затем переключаться на подкладки.
жесткостью 8 0 дюрометров.
Результатом использования более мягкого уретана является более выпуклая форма изделия. Работая с матричными пресс-формами вы должны быть готовы к тому, что ходе работы заготовку придется отжигать и прессовать несколько раз, медленно вдавливая металл в пресс-форму. Также как и при других видах формовочных работ с металлом обработка должна носить ступенчатый характер. Сочетание: пресс 20 тонн и уретан жесткостью 95 - страшная сила, которую вы должны уметь контролировать. Начинайте с низкого давления, чаще отжигайте и постоянно записывайте, какое давление применяли. Металл быстро формуется, но он еще и быстро нагартовывается.
Не имеет никакого значения, в каком порядке расположены слои «сэндвича» (уретан, металл и форма внутри пресса, лишь бы металл находился между уретаном и пресс-формой. Чтобы достичь нужного результата, придется провести несколько пробных операций. Обычно я начинаю экспериментировать с новой пресс-формой, используя медь Проведите пробы с металлом разной толщины, при разном давлении, с уретановыми подкладками разной толщины, с уретаном разной жесткости, варьируйте количество отжигов и формовок. Подробно записывайте на каждом образце, как вы его получили, чтобы под рукой имелась памятка.
Два вида рельефно-формовочных штампов. В первом случае (выше) латунная проволока припаяна к латунной пластине. Во втором случае (справа) линия вырезана в листе пластика.
Рельефно-формовочные штампы.
Два вида описанных ранее пресс-форм используются для объемной формовки. Рельефно-формовочные штампы, напротив, создают неглубокий рельеф на тонком металле. Рельефная формовка отличается от штамповки и прокатки в вальцах тем, что металл формуется с двух сторон.
Первый рисунок демонстрирует, как прокатка в вальцах утончает металл. Рельефная формовка, напротив, выдавливает металл, создавая рельеф без существенного истончения заготовки.
Рельефно-формовочные штампы могут быть собраны из подручных предметов. Прокладки, шайбы, контргайки, металлические решетки, сетки, трафареты, маленькие шестерни и другие мелкие детали могут быть использованы как штампы. Могут быть использованы и различные текстурированные пластики, например, пластик, применяемый в световых рассеивателях и для стекления окон в ванных комнатах. «Органические» материалы, такие как листья просто сжимаются, а природные объекты, такие как ракушки, ломаются и не годятся. Не пытайтесь использовать камни в прессе, так как они дробятся.
Рельефно-формовочные штампы могут быть изготовлены несколькими способами. Проволоку можно напаять на лист металла, чтобы получить простой вариант пресс-формы для рельефной формовки. Так же можно изготовить матричную пресс-форму для рельефной формовки, вырезав рисунок в листе латуни толщиной 1,29 мм (16 B&S). Неглубокий рельеф может быть вырезан борами в акриле. Чтобы формообразование проходило в центре пресс-формы, необходимо оставлять широкий припуск вокруг формуемой части (19 мм (3/4 дюйма) и более).
Лучший результат при рельефной формовке даст отожженный металл толщиной от 0,33 мм (28 B&S) до 0,2 мм (36 B&S). Металл толщиной более.
0,33 мм (28 B&S) формуется плохо, так как его толщина не позволяет ему быть вдавленным в неглубокий рельеф.
К каждой форме нужен индивидуальный подход. Экспериментируйте для достижения наилучшего результата. Следует использовать тонкие (1,5 - 3 мм (1/16 - 1/8 дюйма)) уретановые подкладки жесткостью 8 0 или 95 дюрометров. Их можно расположить одну на другую (например, чтобы получить подкладку толщиной 4,8 мм (3/16 дюйма)) или подрезать ножницами, подогнав по размерам к пресс-форме. Как и в случае с матричной пресс-формой, «сэндвич» можно расположить в прессе в любом положении, лишь бы металл находился между формой и уретаном. Когда я работаю с рельефно-формовочными штампами, я часто использую акриловые блоки в качестве спейсеров, чтобы увеличить расстояние между плитами пресса. Использование спейсеров необходимо в связи с тем, что работа гидравлического пресса менее эффективна при полностью выдвинутом поршне, а рельефная формовка, чаще всего, требует максимального давления, которое может развить 20тонный пресс.
Заключение.
.
Эта информация должна дать вам общее представление об одночастных пресс-формах. Существует множество интересных способов сочетания и последовательного использования различных видов штамповки. Вот некоторые из возможностей:.
• В работе с матричными пресс-формами можно использовать гофрированный металл.
Например: сложите, отожгите, разверните, отожгите и затем отпрессуйте. Складки могут быть оставлены «мягкими» или сделаны «жесткими» путем проковки. Или отдельные части изделия до формовки в матричной пресс-форме могут быть уплотнены молотком.
• Металл, декорированный травлением или прокаткой в вальцах, мокуме, биметалл, металл, инкрустированный припоем и другой, предварительно обработанный металл, может быть отштампован в матричных пресс-формах.
• Чеканенный металл также может быть отформован в матричных пресс-формах. Неотожженный чеканенный металл нужно поместить в пресс так, чтобы уретан вдавливал тыльную сторону отчеканенного листа в пресс-форму.
• Матричные пресс-формы могут иметь гравированный бортик и служить, таким образом, одновременно и рельефноформовочным штампом. Рельефная формовка производится в этом случае одновременно с формовкой контура изделия. (Можно посоветовать производить первое продавливание с тонкой подкладкой).
• Рельефную формовку можно использовать в сочетании со штамповкой пуансонами.
Например, заготовку, полученную путем использования рельефноформовочного штампа, изготовленного из листа с напаянной проволокой, можно дополнительно продавливать пунзелями и пуансонами.
Я надеюсь, что, познакомившись с основными приемами, вы разработаете свои индивидуальные способы использования пресс-форм. Формовка может стать составной частью процесса обработки металла, а не остаться «вещью в себе».
Если металл рвется. . . Убедитесь, что металл отожжен. Используйте более толстый металл. Уменьшите силу давления, чаще проводите процедуру промежуточного отжига. Проверьте, нет ли на пресс-форме острых деталей рельефа или заусенцев. Может потребоваться доработка вогнутых фрагментов.
Возможные осложнения
Если форму перекашивает. . .
Убедитесь, что плиты пресса горизонтальны и параллельны, что штамп помещен в центр пресс-формы, а пресс-форма - в центр плиты пресса.
Если не хватает мощности домкрата после прохождения поршнем определенной точки. . . Не работайте при почти полностью выдвинутом поршне пресса, когда до верхнего положения поршня осталось 25-50 мм (1-2 дюйма). Пользуйтесь акриловыми блоками, чтобы производить работу при среднем положении поршня, где прессовка максимально эффективна. Проверьте сальниковое уплотнение вокруг поршня и убедитесь, что оно заполнено достаточным количеством масла.
Если форма с трудом поддается равномерной штамповке. . . Иногда на пресс-форме есть широкие и узкие участки. В звезде, например, центр формуется хорошо, а лучи остаются плоскими. Сначала используйте тонкую подкладку из 95 уретана, прежде чем перейдете к толстым подкладкам. Тем не менее, то, что на широких участках уретан всегда продавит форму глубже, а на узких мельче, является закономерным при работе как с матричными, так и с рельефно-формовочными пресс-формами.
После интенсивного использования матричная пресс-форма начинает изнашиваться...
Это нормально. Накройте лицевую поверхность матрицы латунной или стальной пластиной или изготовьте новую пресс-форму.
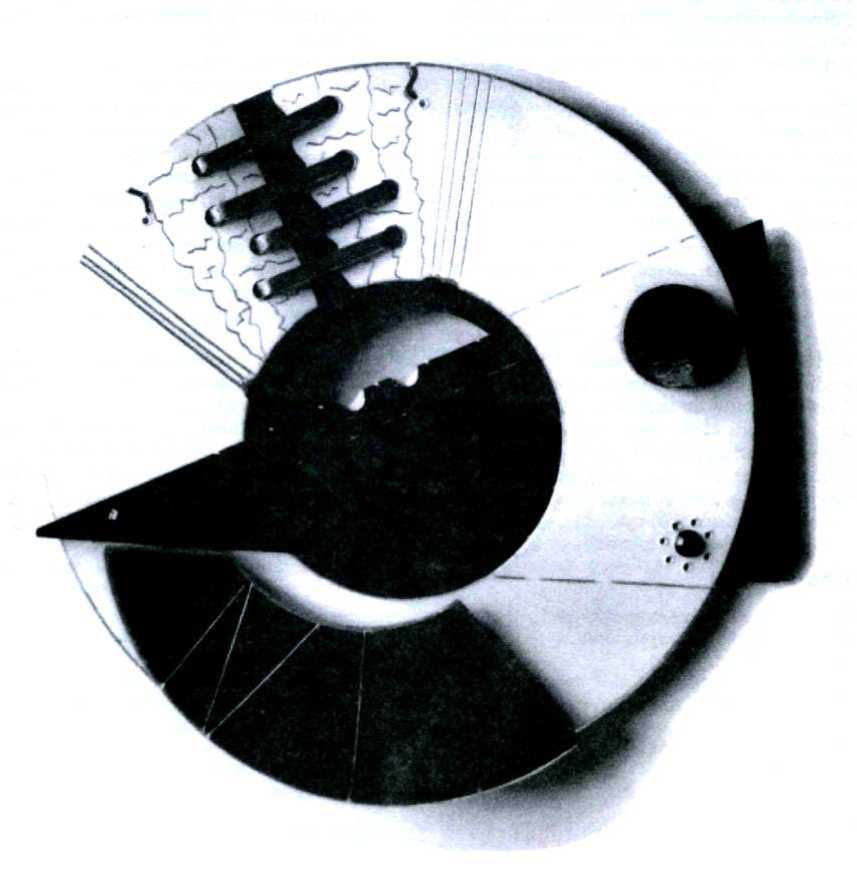
Соединение деталей холодным способом.
.
Приглашаю вас ступить на новый, интересный и дающий неограниченные возможности ускорить создание конструкций в вашем творчестве путь. Соединение деталей холодным способом означает использование механических или химических средств, которые позволяют вам соединять элементы конструкции, обходясь без пайки. Кроме возможности соединять материалы, которые не могут быть спаяны, такие как пластик или бумага, способы холодного соединения деталей позволяют компоновать изделие из уже готовых отполированных деталей. По сути, холодное соединение рассматривается не просто как более легкий способ сборки изделий, но и как важный элемент дизайна и творческой фантазии. Для меня они -широкий проспект в творчестве, по которому я продвигаюсь, совершенствуя свое мастерство.
Возможно, лучше всего начать с того, чтобы открыть для себя окружающий нас мир соединения деталей холодным способом. Будьте готовы дать свободу мыслям и непредвзято смотреть на материалы в ходе исследования нами фантастичного мира способов холодного соединения деталей! Ручаюсь, что после того, как вы начнете использовать эти приемы, вы заметите множество соединений в повседневной жизни, которые нашли применение в ювелирном деле. Старайтесь быть внимательными. Смешно и грустно то, как мы не замечаем важных вещей в нашей жизни, не видя их взаимоотношений, и как это можно связать с нашей работой. Когда я набираю текст на своем ноутбуке, я вспоминаю, как щелкнул диск, скользнув в щель дисковода - холодное соединение.
Они - абсолютно везде!.
Чтобы помочь себе в изучении способов холодного соединения, встречающихся в повседневной жизни, прочитайте невероятную книгу, которая называется The Handbook of Fastening and Joining Metal Parts авторы Vallory H. Laughner,.
Augustus D. Hargan (McGraw-Hill. 1956, LCCN: 54-8 8 01).Если эта книга в 62 0 страниц с изумительными иллюстрациями не вызовет у вас появления хотя бы нескольких идей, тогда вам в этом ни что не поможет.
Прежде, чем мы приступим к подробному изучению того, как пользоваться этими приемами, неплохо было бы осветить некоторые общие моменты. Процесс мышления (или то, как нас научили мыслить) очень часто представляет собой движение по прямой. Лично я предпочитаю двигаться по касательной. Когда мы мыслим прямолинейно, жизнь, ее проблемы и их решения обычно скучны и носят не такой творческий характер, как могли бы. Мысля по касательной, вы свободны и можете в любой момент придать своим мыслям совершенно иное, чем прежде, направление. И, без сомнения, вы вольны и будете возвращаться к прямолинейному мышлению так часто, как это потребуется.
При использовании любого способа холодного соединения деталей принимайте в расчет взаиморасположение, количество и размер соединяемых деталей, их цвет, форму и высоту. Спросите себя, есть ли необходимость использовать подкладные шайбы в функциональных или эстетических целях, и не потребуются ли специальные инструменты или особая последовательность операций.
Типы соединения деталей холодным способом.
Позже я расскажу о клеях, но сейчас мы сосредоточим наше внимание на механических средствах соединения. Они подразделяются на две категории: те, что вы сами изготавливаете в мастерской и уже готовые, которые можно купить и которые вы можете доработать так, как вам хочется.
У стандартной заклепки головка выступает над поверхностью детали (слева). У потайной заклепки зенкованное отверстие вмещает головку. Если заклепка изготовлена из того же материала, что и лист, то она называется «невидимой».
.
Заклепки
Мышление «по касательной»
Методика установки заклепок проста: стержень, полоска или трубка плотно проходит сквозь соединяемые материалы и слегка выступает с каждой стороны. Молоток используют для того, чтобы расплющить металл в процессе, называемом расклепывание. Полученная именно таким образом головка удерживает блок вместе.
Хотя заклепки обычно круглые, вы можете изготовить заклепку такой формы, какой вам хочется, если только вам не жалко времени, требующегося на выпиливание отверстий нужного сечения. Это справедливо как для трубчатых заклепок, так и для распространенных заклепок из проволоки, хотя вам понадобятся скошенные чеканы особой формы, чтобы облегчить расклепывание головки.
Заклепки могут быть установлены так, что головка будет находиться либо над поверхностью металла, либо вровень с ней. Стандартные заклепки вносят разнообразие во внешний вид детали, которая иначе могла бы быть плоской и скучной, тогда как потайные заклепки приятны на вид, так как сливаются с поверхностью. Если использовать металлы разного цвета, это оживит внешний вид изделия. С другой стороны, если заклепка того же цвета, что и металл, то ее совершенно не будет видно.
Здесь описаны буквально десятки вариантов заклепок, не считая тех, которые вы еще придумаете сами. Например, заклепки из проволоки могут быть распилены ювелирным лобзиком и расклепаны в виде шплинта. Двойной распил в форме буквы X открывает новые возможности. В обоих случаях кончик проволоки просто раздвигается лезвием ножа или маленькой отверткой.
Для расклепывания я обычно пользуюсь молотком с маленьким круглым бойком. Каждый удар молотка выдавливает металл на 360°. Если начать с середины проволоки и двигаться наружу по концентрической спирали, то металл будет.
расклепываться быстро и ровно. Простой и эффективный способ продемонстрировать воздействие ударов молотка - это скатать столбик из пластичной глины, размером примерно с ваш мизинец, следя за тем, чтобы оба торца получились плоскими. Крепко зажмите столбик в кулак, как показано на рисунке, и воспользуйтесь молотком с круглым бойком, действуя, как описано выше.
.
Обратите внимание на соотношение диаметра стержня заклепки, сверла, требующегося для того, чтобы сделать подходящее отверстие, и размера фильеры в волочильной доске, используя которую, можно вытянуть проволоку такого сечения. В данном случае имеется 3 взаимосвязанных параметра и, когда определен один из них, он диктует, какими должны быть два других. К примеру, если у вас имеется сверло только одного размера, это продиктует использование проволоки определенной толщины для стержня заклепки. Что, в свою очередь, если вам необходимо вытянуть проволоку, отсылает вас к определенной фильере на волочильной доске. Например, сверло №53 примерно соответствует проволоке сечением 1,63 мм (14 B&S), которая, в свою очередь, соответствует фильере №25 на моей волочильной доске Joubert «Е». Приятно видеть, как легко все взаимосвязи расставлены по своим местам.
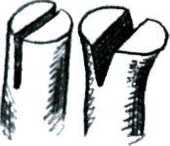
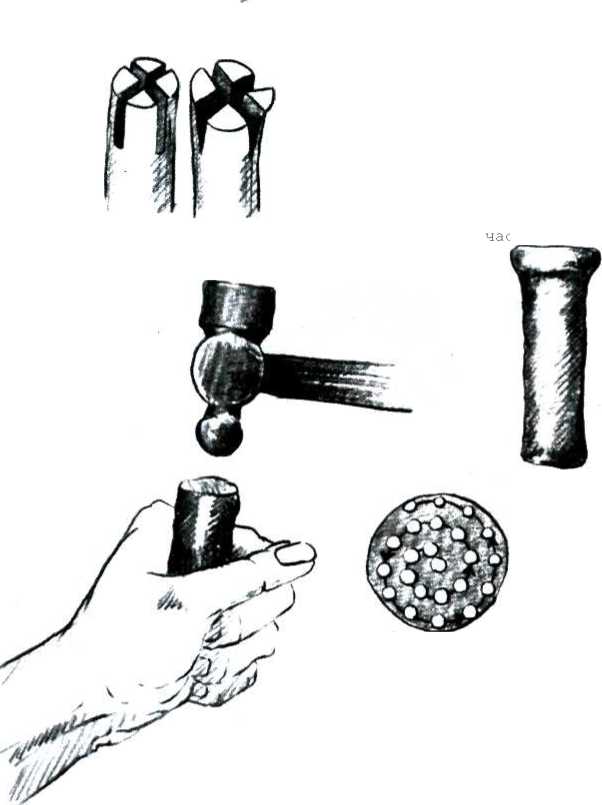
У заклепок, изготовленных из проволоки малых диаметров, головка распиливается самым тонким полотном одним или двумя надрезами. Чтобы образовать захват, при помощи ножа нужно раздвинуть полученные части в стороны.
Кусок глины используется, чтобы продемонстрировать принцип образования головки заклепки. Как показано, удары молотка перемещаются по спирали от центра к краю.