.
.
Комплексная механизированная и комплексная автоматическая линии изготовления моделей. На рис. 10.1 приведен один из вариантов плана расположения типового серийного оборудования [31 ] со взаимно увязанной производительностью, скомпонованного в две линии: комплексную механизированную (мод. 652 — 654) и комплексную автоматизированную (мод. 652—653). Первая линия предназначена для изготовления моделей серийных отливок, вторая — моделей отливок массового производства [59, 70].
Из ванны выплавления моделей 1 возврат модельного состава вместе с горячей водой стекает по лотку в разделитель 2. Если модели из оболочек выплавляют не в воде, а в модельном составе, то разделитель может быть изъят из системы. В разделителе модельный состав отделяется от воды, которая после очистки сливается в канализацию, а модельный состав скапливается в баке, откуда насосом 3 по трубопроводу 4 перекачивается в плавильный агрегат 5. Сюда же подают и свежие модельные материалы. В плавильном агрегате расплавленный модельный состав отстаивается, дополнительно очищается от воды и посторонних включений. Далее насосом 6 он подается по трубопроводу 7 в емкостные баки 8, откуда направляется в пастоприготовительные агрегаты 9. В них модельный состав приобретает пастообразную консистенцию благодаря охлаждению до температуры частичной кристаллизации и замешиванию воздуха.
Пастообразный модельный состав по трубам 10 подают _ под давлением к автоматам И и карусельным установкам 12 изготовления моделей. Температуру обогревательных устройств во
Рис. 10.1. Плаи расположения оборудования для изготовления моделей.
.
всех звеньях линий поддерживают насосно-нагревательные стан-ции 13. На поворотных столах автоматов 11 установлено по десять пресс-форм. Заполнение рабочей полости пресс-форм модельным составом, выдержка для затвердевания модели, раскрытие пресс-форм, выталкивание звена моделей, очистка литникового отверстия и обдув рабочей полости выполняются автоматически по заданному циклу.
На карусельных установках 12 механизированы заполнение полости пресс-форм, раскрытие их и выталкивание моделей. Выем звена моделей, очистку литникового отверстия, обдув и смазывание рабочей полости пресс-формы выполняют вручную.
Рассмотренные линии рекомендованы для изготовления моделей из легкоплавких составов.
Комплексная автоматическая линия приготовления суспензии (рис. 10.2). Применение этой линии позволяет решить задачу автоматизации тяжелых и вредных для здоровья операций приготовления суспензии и подачи ее к местам потребления. Линия разработана на Горьковском автозаводе, в ней использованы автомат при-
Рис. 10.2. Схема комплексной автоматической линии приготовления суспензии.
.
готовления суспензии (мод. 662), машина для разрезки мешков с пылевидным огнеупорным материалом и печь для его прокаливания констр укции Гипротр акторосель хозмаша.
Мешки вспарывает машина 1. Пылевидная составляющая суспензии из бункера машины закрытым конвейером 2 передается для сушки в печь 3, затем поступает в аппарат 4 для охлаждения, а оттуда в полигональное сито 5. Из-под сита материал передается в бункер 7 автомата с помощью системы закрытых конвейеров 6 (или в кюбелях). Жидкие составляющие суспензии из цисцерн 16 подаются насосами 15 по трубам 11 в напорные баки 8, установленные над автоматом. В напорный бак для подкисленной воды кислота подается из бутылки 10, а вода из водопровода. В автомате 9 исходные составляющие суспензии непрерывно смешиваются, и готовая суспензия стекает в бак 12. К местам потребления она подается под действием сжатого воздуха (патрубок 13) по резиновым шлангам 14.
На рис. 10.3 приведена схема основного механизма линии — автомата приготовления суспензии. Из расходных баков растворителя 1, этилсиликата 4 и подкисленной воды 6, в которых поддерживают с помощью насосов 7 и переливных патрубков 3 постоянный уровень, жидкие составляющие суспензии через клапаны 2 по трубопроводам 5 поступают самотеком к дозировочной панели автомата. Расход жидкостей устанавливают с помощью игольчатых кранов 8 по ротаметрам 9. Заданное количество жидких составляющих суспензии непрерывно поступает в смеситель 12. Одновременно с жидкостными дозаторами включают дозатор пылевидной составляющей суспензии, которая из бункера 16 по лотку 15 попадает на ленту конвейера 14. Гайкой 17 регулируют положение заслонки 18, уменьшая или увеличивая количество пылевидного материала, поступающего непрерывно по лотку 13 в смеситель 12, где все составляющие суспензии интенсивно смешиваются крыльчатками 11.
.
Рис. 10.3. Схема автомата приготовления •суспензии.
.
Выдача готовой суспензии происходит непрерывно через переливной патрубок 10.
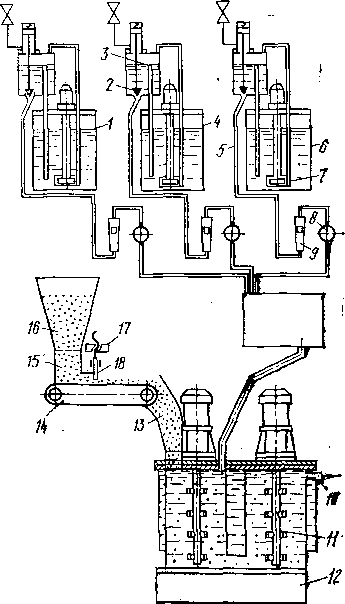
При необходимости получения отдельных порций (120—.
150 л) может быть установлен цикличный режим работы и осуществлена соответствующая настройка дозаторов, в зависимости от того, какой вязкости и состава требуется суспензия. В системе автоматической линии могут работать несколько таких автоматов.
Автоматическая линия изготовления оболочек.
(рис. 10.4).
На линии выполняются операции по формированию оболочек на блоках моделей и выплавлению последних. Автоматы изготовления оболочки 2 (мод. 6А67), камера сушки 1 (мод. 6А82) и ванна выплавления моделей 3 (мод. 672) объединены в единую линию.
(мод. 6Б60) конвейером, который помимо транспортных функций благодаря конструкции подвески выполняет и рабочие операции: подъем, опускание и вращение подвесок с блоками.
На участке сборки конвейер имеет спуск к рабочим местам навешивания модельных блоков. Модельные блоки поступают в автомат № 1, где формируется первый слой оболочки, и по конвейеру направляются в камеру сушки. Пройдя первую ветвь конвейера, высохшие блоки поступают для нанесения второго слоя в автомат № 2, затем снова в камеру сушки и так далее до получения пятислойной оболочки. После прохождения каждого из автоматов нанесения оболочки (№ 1—№ 5) автоматически очищается торец литниковой воронки.
Блоки с пятью слоями оболочки транспортируются конвейером в ванну выплавления моделей. Здесь блоки воронкой вверх погружаются в горячую воду или модельный состав. При прохождении через , ванну выплавления оболочки удерживаются на стояке благодаря спиральной канавке на металлическом колпачке, формирующем металлоприемник. Подвески конвейера с выплавленными оболочками при выходе из ванны, наезжают на копир и, обкатывая
Рнс. 10.4. Схема автоматической линии изготовления оболочек.
.
его, поднимаются, получая вращение вокруг продольной оси. При вращении из оболочки выливаются вода и модельный состав. После выплавления моделей оболочки снимают с конвейера. Освобожденные стояки проходят мойку- и возвращаются на участок изготовления модельных блоков.
Автомат изготовления оболочек (рис. 10.5). Автомат состоит из трех узлов: пескоеыпа с «кипящим слоем», ванны с суспензией м бака хранения и подачи суспензии. Блоки 1 по конвейеру 3 посту-
Рис. 10.5. Схема автомата изготовления оболочек.
.
пают к ванне 8 с суспензией. Подвеска конвейера 4, на которой укреплен блок, обкатывая копир 5, поднимается, переходит через край ванны и, двигаясь далее вдоль опускающегося копира, погружает блок в суспензию. Суспензия в ванне охлаждается проточной водой, пропускаемой через рубашку под днищем ванны. Для предотвращения оседания пылевидной составляющей суспензии последняя непрерывно перемешивается (мешалка не схеме на показана).
При дальнейшем движении конвейера блок выходит из суспензии и поступает в пескосып «кипящего слоя» 6 с перфорированной перегородкой 7. В пескосыпе происходит обсыпка нанесенного слоя суспензии зернистым огнеупором. По мере расхода суспензии ванну пополняют, для чего в бак 11, где хранится суспензия, подают сжатый воздух, который выжимает ее через трубу 9 и далее по шлангу 2 в ванну. После выдачи необходимого количества суспензии подачу сжатого воздуха прекращают, а давление в баке 11 сбрасывают. В баке суспензия непрерывно перемешивается мешалкой 10 и охлаждается водой. В ванне с суспензией предусмотрены устройства для слива и промывки, а в пескосыпе система очистки песка.
Механизированная поточная линия заформовывания оболочек, прокаливания, заливки форм, охлаждения и выбивки отливок конструкции ЗИЛ (рис. 10.6). Замкнутую поточную линию образуют установка для заформовывания оболочек в опорный наполнитель (в опоках), печь 1 для прокаливания, заливочный роликовый конвейер 3, камера охлаждения 5, устройство 6 для выбивки опок и роликовый конвейер 8 для возврата пустых опок.
В опоки, расположенные на формовочных столах 11, ставят оболочки и сверху из бункеров 12 насыпают опорный наполинитель, уплотняемый вибраторами. Наполинитель, просыпанный при заполнении опок, попадает в приемный бункер пневмотранспорта и возвращается в бункера 12. Заформованные опоки толкателями 9 продвигаются в газовую двухрядную проходную печь 1 для прокаливания. Прокаленные опоки извлекают из печи с помощью цепных вытаскивателей и подают на приемные столы 2. Продукты го-
Рис. 10.6. Механизированная поточная линия для заформовыва-ння оболочек, прокаливания заливки форм, охлаждения и выбивки отливок.
.
рения удаляются из печи дымососной установкой 10. Приемные столы 2 опускают и ставят опоки на приводной рольганг 3, на котором формы заливают расплавом. После заливки опоки по роликовому конвейеру поступают на подъемный стол 4, который поднимает их до уровня роликового конвейера камеры охлаждения 5. В последнюю опоки перемещаются гидравлическим толкателем. Охлажденные опоки из камеры поступают в поворотное устройство 6 для выбивки. Во время поворота опок включают пневматические вибраторы и наполнитель из опок высыпается через решетку на экс-.
центриковое сито. Отсев ссыпается в ящик, стоящий на роликовом конвейере, а просеянный наполнитель системой пневмотранспорта 13, 14 возвращается в бункера, расположенные над формовочными столами. После выбивки машина возвращается в исходное положение и опока поступает на приемный стол 7 роликового конвейера 8 возврата пустых опок. Здесь отливки удаляют из опок, а последние вновь подают на формовочные столы.
Если позволяют условия, то заливочную площадку лучше выполнять приподнятой над уровнем пола. В этом случае отпадает необходимость опускать опоки по выходе их из печи и поднимать для подачи в камеру охлаждения. Камера охлаждения должна иметь объем, примерно равный печи прокаливания; в противном случае формы не успеют достаточно охладиться. Следовательно, в рассматриваемой схеме камера охлаждения должна быть двухрядной.
Комплексная механизированная поточная линия прокаливания, формовки, заливки оболочек форм, выбивки и охлаждения отливок (мод. 675А). Эта линия (рис. 10.7) рассчитана на прокаливание оболочек без опорного материала. Она состоит из печи прокаливания 1, заливочной карусели 3 и камеры охлаждения 7, объединенных конвейером 9.
Оболочки формы устанавливают на подвески 10 конвейера, литниковые воронки закрывают колпачками, которые фиксируют оболочки на подвесках и предохраняют их полости от засора. Конвейер транспортирует подвески через печь прокаливания. Внутрь печи
Рис. 10.7. Схема комплексной механизированной поточной линии прокаливания, формовки» заливки оболочек форм, выбнвки н охлаждения блоков отлнвок.
через щель в своде заходит только нижняя часть подвески из жаростойкой стали, цепь же конвейера, ходовая часть подвесок и трасса работают вне горячей зоны печи. Сверху вдоль всей щели в своде предусмотрена вытяжная вентиляция для отсоса выбивающихся из печи газов. Прокаленные оболочки у выхода из печи погружаются в горячий песок, которым заполнен желоб заливочной карусели.
Привод заливочной карусели осуществляется конвейером через звездочку 4. Опускание подвесок выполняет пневматический лифт 6, который перебрасывает каретку подвесок с верхней трассы на нижнюю при движении конвейера. При опускании штанга подвески скользит во втулке тяговой цепи конвейера. Погружение подвесок с оболочками в песок становится возможным благодаря созданию на позициях погружения (формования) «кипящего слоя». «Кипение» его достигается продувкой снизу горячими газами, поступающими из печи через неподвижный коллектор 2. Трубы коллектора опущены в желоб карусели через край и не мешают вращению ее, работая в «кипящем слое» подобно плугу.
При дальнейшем движении конвейера оболочки, погруженные на подвесках в песок выходят из зоны «кипения» и оказываются за-формованными. По внешнему сектору вращающейся карусели формы заливают расплавом. Перед заливкой откидывают колпачки, прикрывающие литниковые воронки.
Блоки отливок, затвердевая и частично охлаждаясь в опорном наполнителе, движутся к камере 7. У входа в камеру подвески с залитыми блоками выдергивают из карусели пневматическим подъемником 5. При этом каретка подвески переставляется с нижней трассы обратно на верхнюю. Песок с подвесок и блоков отливок ссыпается в желоб карусели, а подвеска с блоком отливок продолжает движение по конвейеру, проходит в камеру 7, где отливки окончательно охлаждаются водяным душем. Вышедшие из камеры 7 блоки отливок снимают с подвесок, и последние возвращаются на рабочее место установки оболочек. Снизу вдоль камеры охлаждения проходит ленточный конвейер 8, передающий смытый водой песок и кусочки оболочки на общецеховой конвейер убожи отходов.
Для поддержания постоянного уровня песка в желобе карусели имеется бункер досыпки, в который сухой песок подают со склада пневмотранспортом.
Автоматическая линия очистки отливок от оболочки и отделения отливок от стояка конструкции НИИТАвтопром (рис. 10.8). Линия имеет три основных механизма: установку очистки отливок II, горизонтальный гидравлический пресс для отделения отливок от стояка / (гидравлическая станция на рисунке не показана) и конвейер III.
При работе линии на приемные призмы 9 тележки конвейера 15 укладывают блок отливок 8. В исходном положении тележки вторая пара призм 7 с блоком находится на позиции очистки отливок. Перемещаясь по направляющим 6, тележка передает блок 8 на позицию очистки, а очищенный блок на пресс. Приводом тележки кон-
вейера служит пневмоцилиндр 10, действующий через кулисный механизм 11. При подходе к крайним положениям тележка приподнимается благодаря форме направляющих 6, а при обратном ходе начинает свое движение с опускания. Этим обеспечивается беспрепятственный выход призм из зацепления с зажатыми на рабочих позициях блоками при отходе тележки конвейера.
Механизм очистки состоит из цилиндра зажима блоков 16 и вибрационного устройства 14, смонтированных на общей станине. При подходе тележки конвейера блок отливок, поданный на очистку, зажимается между упорами отбойного молотка и зажимного цилиндра за счет срабатывания пневматических цилиндров. Затем тележка отходит, включается отбойный молоток и начинается очистка отливок от оболочки. Во избежание жестких ударов отбойный молоток подпружинен. Отскочившие кусочки оболочки падают вниз и через проем станины ссыпаются на ленту конвейера уборки отходов. Длительность очистки регулируют с помощью реле времени. После окончания очистки упоры раздвигаются и блок отливок спадает на призмы 7.
При следующем ходе тележки очищенный блок подается на гидравлический пресс. На рабочей позиции пресса блок зажимается между упором 2 рабочего цилиндра 1, упирающегося в воронку, и штоком 4 подпорного цилиндра 5, упирающегося в металлоприем-ник. После отхода конвейера под действием рабочего цилиндра
Рис. 10.9. Схема отделения отливок от стояка на горизонтальном прессе:.
1 — упор рабочего цилиндра; 2 — шток подпорного цилиндра;.
3 — фильера.
стояк проталкивается через фильеру (рис. 10.9). Ход пресса может быть пульсирующим. Рабочие кромки фильеры скалывают питатели и отливки падают на наклонный стол 12 (см. рис. 10.8) пресса и далее в тару либо на ленту конвейера. Обрубленный стояк выталкивается из фильеры штоком подпорного цилиндра.
Обрубленный стояк убирается из рабочей зоны пресса манипулятором 13 с захватом 3 и сбрасывается им в тару или на конвейер. На освободившуюся позицию пресса подается для обрубки следующий блок отливок.
Работа механизма очистки и пресса идет одновременно, синхронность и блокировки обеспечиваются системой автоматики. Линию обслуживает один рабочий, который укладывает блоки отливок на приемные призмы конвейера и следит за работой механизмов.
Полуавтоматическая установка для обрубки питателей конструкции НИИТАвтопрома (рис. 10.10). Установка создана на базе пресса мод. К2130А и оснащена поворотным столом 1, на котором установлены шесть приспособлений. В каждое из них на позициях загрузки вручную укладывают отливки. Две позиции загрузки рас-
Рис. 10.10. Полуавтоматическая установка для обрубкн питателей.
положены на выступающий из-под пресса стороне поворотного стола. Стол поворачивается при каждом ходе пресса на 60° и по очереди подает приспособления с отливками на позицию обрубки — под нож, укрепленный на верхней плите 5. При рабочем ходе ползуна пресса отливки сначала прижимаются к приспособлениям механизмом прижима 7, а затем нож срубает выступающий питатель. Отрубленные питатели проваливаются через окно под стол пресса в тару для отходов. Привод поворотного стола осуществляется от вала пресса через верхний редуктор 2, карданный вал 3 и нижний редуктор 4. Обрубленные отливки выталкиваются из приспособлений механизмом 6. Отливка падает на лоток и затем соскальзывает в тару 8, установленную сбоку пресса. Производительность установки до 2100 отливок в час.
Механизация взвешивания и транспортирования шихты к плавильным печам. В цехах литья по выплавляемым моделям в качестве шихты^обычно используют отходы кузнечно-штамповочных цехов (высечку, клещевину), отходы собственного производства (литники, брак отливок), а также ферросплавы и свежий металл.
На рис. 10.11 приведен план расположения оборудования для взвешивания и транспортирования шихты, по проекту Гипротрак-торосельхозмаша. На складе шихты имеется кран 1 с магнитной шайбой для разгрузки металла и раздачи его по бункерам 2. Для каждой составляющей шихты предусмотрен свой бункер. Вдоль фронта бункеров по ресльсам паредвигается весовая тележка 3, на платформу которой ставят бадью. Рабочий подъезжает на весовой тележке к нужному бункеру, включает питатель 4 и шихта поступает в бадью. Набрав нужное количество, рабочий отключает питатель и переезжает к другому бункеру для взвешивания следующего компонента. После набора всей порции шихты бадья подвозится на позицию 5, где цепляется за электроталь, развозящую шихту по плавильным печам 6.
Автоматизация с помощью промышленных манипуляторов. На рис. 10.12 показан план расположения механизмов автоматической линии для изготовления модельных блоков конструкции НИИТАавтопрома и ХФ ВНИИЛитмаша. На линии изготовляются звенья моделей из пенополистирола и собираются в блоки. Линия состоит из 10-позиционного термопластавтомата 1 для изготовления звеньев моделей, автомата сборки блоков моделей 2 с встроенным манипулятором 3 и двух отдельно стоящих манипуляторов 4 я 6 с программным управлением. Манипулятор 3 забирает изготовленное звено моделей из открытой пресс-формы на позиции А термопластавтомата и надевают его на стояк, расположенный на позиции Б автомата сборки. Манипулятор 4 перевешивает собранные модельные блоки с автомата сборки на толкающий конвейер, а манипулятор снимает с толкающего конвейера стояки и устанавливает их на поворотной стол автомата сборки. Подвески толкающего конвейера фиксируются против манипуляторов остановами 5 [80, 81].
Рис. 10.11. План расположения оборудования для взвешивания и транспортирования шихты.
На рис. 10.13 показан манипулятор с программным управлением, спроектированный ХФ ВНИИЛитмаша для цехов литья по выплавляемым и выжигаемым моделям. Манипулятор предназначен для замены человека на тяжелых, монотонных и вредных операциях, например при изг товлении оболочковых форм.
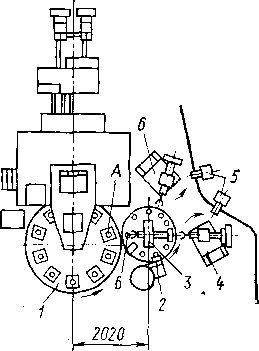
Рис. 10.12. План расположения механиз мов автоматической линии для изготов леиия модельных блоков
Техническая характеристика манипулятора мод. 5102
Имеется положительный опыт использования автоматических манипуляторов в цехе литья по выплавляемым моделям завода «Авто-цветлит» (г. Мелитополь). В этом цехе манипуляторами заменили рабочих на тяжелой операции съема залитых блоков с подвесок агрегата мод. 675А.
Механизация управленческого труда. В условиях комплексной автоматизации производственных процессов большое значение приобретает механизация и автоматизация работ, связанных с учетом и оперативным управлением производством.
Рис. 10.13. Манипулятор с программным управлением мод. 5102.
.
На рис. 10.14 приведена принципиальная схема оперативного управления крупным цехом, разработанная НИИТАавтопромом. Технические средства оперативного управления производством выполняют следующие функции:.
дистанционный автоматический учет числа собранных блоков моделей, оболочек (годных, забракованных, поступивших на прокаливание) и обрубленных блоков отливок;.
дистанционный автоматический учет запаса оболочек на складе; дистанционный полуавтоматический учет числа отливок по наименованиям, поступивших на склад и выданных со склада готовой продукции цеха;.
автоматическое фиксирование учетной информации на рапорте с помощью электроуправляемой пишущей машинки;.
дистанционную автоматическую передачу всей учетной информации в информационно-вычислительный центр завода (ИВЦ), который разрабатывает и выдает цеху подетальные производственные программы запуска и выпуска, обрабатывает аналитически сводки выполнения планов цехом;
Рис. 10.15. Расположение технических средств учета и оперативного управления производством:.
1 — зал генераторов; 11 — плавильный участок; 111 — участок обжнга, формовки, заливки оболочковых форм, выбивки и охлаждения блоков отлнвок; IV — участок изготовления оболочковых форм; V —участок изготовления модельных блоков; VI —участок приготовления модельного состава; VII — участок очистки отлнвок; VIII — участок термообработки; IX — участок обрубки и отделки отлнвок; X — склад отливок; XI — ремонтная мастерская; XII — участок приготовления суспензии; XIII — экспресс-лаборатория; XIV — контрольно-диспетчерский пункт; XV — склад шихты; 1 —- измерительный преобразователь контроля производственного состояния оборудования; 2 — измерительный преобразователь контроля технологического параметра; 3 — измерительный преобразователь счета; 4 — динамический громкоговоритель; 5 — цифровое табло
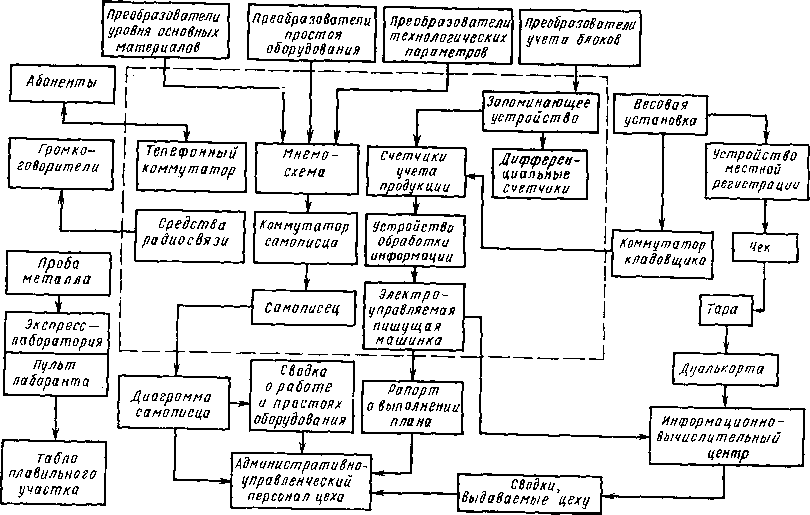
Рнс. 10.14. Принципиальная схема оперативного управления цехом литья по выплавляемым моделям (технические средства контроль-но-диспетчерского пункта выделены рамкой)
Рис. 10.16. Контрольно-диспетчерский пункт цеха.
.
сигнализацию о производственном состоянии основного оборудования цеха;.
автоматическую, выборочную регистрацию времени работы и простоев основного оборудования цеха;.
дистанционный автоматический контроль наличия основных материалов;.
диспетчерскую телефонную связь внутри цеха;.
производственную радиофикацию цеха;.
передачу результатов химического анализа металла из экспресс-лаборатории на плавильный участок.
На рис. 10.15 показано расположение технических средств применительно к плану расположения оборудования цеха мощностью 4000—5000 т в год. Вся полученная информация сосредотачивается в контрольно-диспетчерском пункте (КПД) (рис. 10.16). Сигнализирующая и управляющая аппаратура расположена на панелях пульта диспетчера 1. На панель вынесены дифференциальные счетчики, показания которых необходимы диспетчеру для оперативной деятельности, а остальные установлены в шкафах 2. Вспомогательная аппаратура смонтирована в стойках 3. Коммутатор 4 — на столе.
Функции оперативного управления производством осуществляются следующим образом.
Собранные модельные блоки считаются контактными преобразователями на конвейерах, передающих блоки с модельного участка к автоматам изготовления оболочковых форм. Счет регистрируется на КДП. После выплавления моделей подсчет оболочковых форм производится на конвейерах, подающих их на обжиг. Так как часть из них может не сниматься у агрегатов обжига и возвращаться к месту счета, число их определяют как разность между числами про.
шедших пб Подающей и возвратной ветвям конвейера. Вычитание производится автоматически дифференциальным счетчиком. Учет забракованных оболочек осуществляется аналогично, как разность между числом выплавленных и суммы поступивших на склад и на агрегаты обжига.
Оболочки, поступившие на прокаливание, учитываются на конвейерах агрегатов обжига измерительными преобразователями, сигналы с которых поступают на запоминающее устройство, а после опроса — на счетчики аппаратного шкафа КДП.
Обрубленные блоки отливок учитывают измерительные преобразователи, установленные на прессах-автоматах для отделения отливок от стояка.
Дистанционный полуавтоматический учет отливок (по наименованиям), поступивших на склад готовой продукции цеха, осуществляется с помощью установки, состоящей из платформенных весов с циферблатным указателем, позволяющим преобразовывать массу взвешенных отливок в электрические импульсы; устройств местной регистрации массы и передачи данных взвешивания на расстояние. При поступлении на склад очередного стандартного ящика с одинаковыми отливками кладовщик ставит его на платформу весов и на пульте набирает шифр взвешиваемых отливок. Убедившись в правильности набора шифра по контрольной сигнализации, кладовщик нажимает кнопку «Ввод информации». При этом данные.
о массе отливок фиксируются на ленте регистрации и передаются в КДП на соответствующий счетчик. Кроме этого, данные о массе отливок поступают на суммирующий счетчик, и диспетчер может следить за общей массой отливок, выпущенных цехом. После взвешивания кладовщик направляет ящик с отливками на стеллаж, сопровождая его чеком с данными взвешивания, который он отрывает от ленты регистрации массы отливок.
Для учета отливок, выданных со склада, служит дуаль-карта. По чеку, находящемуся в ящике с отливками, кладовщик отмечает массу отправляемой партии в дуаль-карте и отправляет ее на ИВЦ.
По команде диспетчера автоматически печатается рапорт со всей информацией, накопленной на КДП. Этот рапорт используется руководством цеха для оценки деятельности подразделений цеха. Дистанционная передача информации в ИВЦ осуществляется по его запросу раз в сутки в том же объеме, что и на внутрицеховом рапорте. В ИВЦ эта информация используется при составлении аналитических сводок о выполнении плана цехом, для внесения коррективов в программу цеха и др.
Сигнализация о производственном состоянии оборудования осуществляется с помощью мнемонической схемы. На изображении агрегатов (на схеме) установлены лампы, сигнализирующие об остановке агрегатов. Кроме того, на мнемонической схеме имеются сигнальные лампы, предупреждающие о нарушениях технологических параметров, влияющих на качество выпускаемой продукции.
Продолжительность работы и простоев оборудования регистрируется с помощью автоматического самопишущего прибора. Автоматическая регистрация позволяет анализировать работу оборудования по объективным данным и принимать необходимые меры.
Контроль наличия на складе жидких составляющих суспензии (этилсиликата, ацетона и др.) осуществляется измерительными преобразователями — уровнемерами, устанавливаемыми в емкостях их хранения.
Диспетчер имеет в своем распоряжении телефонный коммутатор (с устройствами светового вызова абонента в шумных местах цеха) и 20 каналов громкоговорящей связи, подключать которые можно по одному и все сразу. Средства радиосвязи используют для поиска и вызова работников цеха, для распоряжений, объявлений и т. п. Сигнализация химического анализа металла обеспечивает быструю передачу сведений из экспресс-лаборатории на плавильный участок. По команде из лаборатории на табло плавильного участка загораются цифры, обозначающие содержание химических элементов в сотых долях процента.
10.2. ЦЕХИ ЛИТЬЯ ПО ВЫПЛАВЛЯЕМЫМ МОДЕЛЯМ.
Цехи литья по выплавляемым моделям в структуре машиностроительного предприятия относят к основным (производственным) заготовительным литейным цехам.
Цехи различают (табл. 10.1) по роду сплава, массе отливок, объему производства, серийности, степени механизации и сложности отливок.
В состав цехов входят производственные отделения (участки), вспомогательные отделения (участки) и склады.
К производственным отделениям, где выполняется собственно технологический процесс изготовления отливок, относят следующие: модельное, в котором приготовляют модельный состав, изготовляют модели, собирают блоки моделей; изготовления оболочек форм, в котором приготовляют суспензию, изготовляют оболочки, выплавляют из них модели; прокалочно-заливочное, в котором оболочки форм заформовывают в опорный наполнитель и прокаливают, плавят и заливают в формы металл, охлаждают и выбивают блоки отливок; термообрубное, где очищают отливки от остатков оболочек, отделяют отливки от ЛПС, зачищают питатели, проводят термообработку и исправляют дефекты отливок.
К вспомогательным относят следующие отделения: подготовки формовочных материалов и шихты, ремонта пресс-форм и другой технологической оснастки, мастерские механика и энергетика, цеховую лабораторию, вентиляционные и пылеочистные установки и КДП.
К складам относят закрытые склады шихтовых, формовочных, горючих материалов, готовых отливок.
В цехе предусматривают также помещения для культурно-бытового обслуживания работающих: санитарно-бытового назначения, общественного питания, здравоохранения, культурного обслуживания, учебных занятий и общественных организаций, управлений.
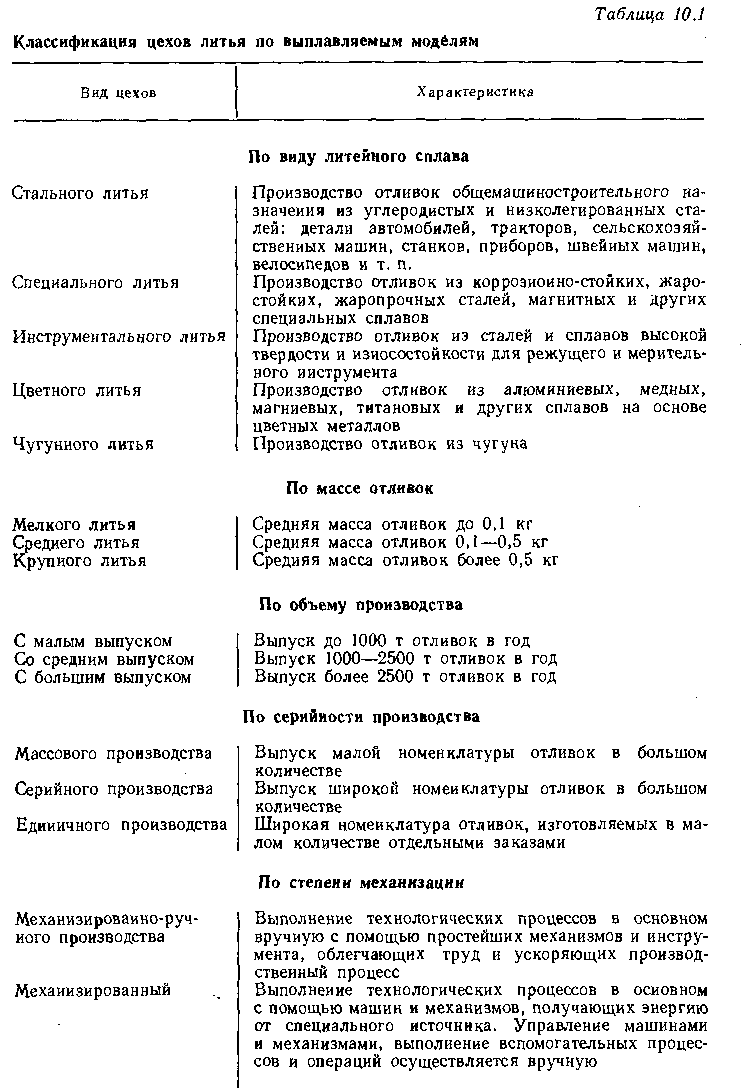
* Группы сложности отливок приняты в соответствии с прейскурантом оптовых цен на отливки.
РАЗРАБОТКА ТЕХНОЛОГИЧЕСКОЙ ЧАСТИ ПРОЕКТА ЦЕХА.
Исходными данными для разработки проекта цеха служат следующие основные документы: задание на проектирование (включает технико-экономическое обоснование проекта); производственная программа; чертежи и технические условия на отливки.
Производственная программа. Программа монсет быть точной (подетальной), приведенной или условной. Подетальную программу производства массовых и крупносерийных отливок составляют по форме 10.1 Программу приводят по видам металла, изделиям и узлам (группам) в порядке возрастания номеров узлов и деталей. На основании подетальной программы составляют производственную программу по форме 10.2, которую заполняют по видам и маркам металла.
Технологический процесс и оборудование. Выбор варианта технологического процесса является определяющим, главным в проек-
тировании цеха. Выбранные варианты технологического процесса и оборудование должны обеспечивать получение отливок нужного качества с наименьшими трудовыми и материальными затратами. Для выполнения этой задачи проектировщик должен не только располагать сведениями о передовом отечественном опыте, но и учитывать данные научно-технического прогноза, чтобы к моменту ввода в эксплуатацию новое производство было на уровне мировых технических достижений.
Для оценки варианта нового технологического процесса его сравнивают с наилучшим из известных, который принимают за базовый. Оптимальной технологией изготовления отливок считают ту, которая обеспечивает минимум приведенных народнохозяйственных затрат на производство готовых деталей.
Для практических расчетов по выбору оптимального технологического процесса Б. В. Кнорре рекомендует использовать упрощенную формулу
где Сц и С
— себестоимости изготовления отливок в литейном цехе и механической обработки, руб/т, руб/шт; В
—выпуск отливок, т/год, шт/год; Е
— коэффициент эффективности капитальных вложений, £
»0,12; К
к Ки — капитальные вложения по варианту.
технологии производства отливок в литейном цехе и в механическом цехе, руб.
_ .
.
В соответствующих главах книги даны основы для выбора технологии и оборудования, отвечающие особенностям производства отливок различного назначения.
.. В табл. 10.2 приведены рекомендуемые процессы и оборудование (без плавильного) для цехов, выпускающих мелкие и средние стальные отливки.
Исходные технологические данные отдельно по каждой группе по массе рассчитывают и заносят в ведомости по форме 10.3.
Форма 10.3.
Исходные технологические данные (группа отливок по массе)
№ п.п | Я. Ч. 03. Н | Масса отливкн, кг (А) | Про. грамма | Число моделей в звене (В) | Число звеньеа в блоке | Число моделей в блоке (Г) . | Число модельных звеньев (моделей) на программу | Число блоков на программу (Д) | Масса модельного состава, кг | |||
шт. (Б) | кг | на одну модель (Е) | на один блок (Ж) | на. про. грамму | ||||||||
Б/В | Б/Г | Api/p а | ЕХГ+ + VnPi | ЖХД | ||||||||
Итого |
Примечание. Pi, Рг — плотности соответственно модельного состава и материала отливкн, кг/м*; — объем ЛПС и модельного стояка (нлн суммы модельных втулок), м
Рекомендуется деление номенклатуры отливок на восемь групп по массе, кг: 1,5. Такое деление оправдано тем, что для каждой группы отливок характерны свои технологические нормативы и показатели.
Форма 10.3 содержит только исходные технологические данные и использовать их для расчета числа оборудования нельзя. В этих данных не учтены неизбежные на производстве потери и брак из-за некачественных материалов, ошибок рабочего, неисправности оборудования и других причин. Брак и потери на производстве возмещают путем увеличенного против программы изготовления моделей, форм или отливок по переходам процесса. Для определения числа Подлежащих изготовленоию моделей, форм и отливок на которое рассчитывают оборудование, вводят коэффициенты технологических потесь:

где В
п
— число отливок, форм или моделей, которое необходимо изготовить в данном отделении для выполнения программы и для восполнения брака и потерь; В —число отливок, форм или моделей по программе (без учета брака и потерь).
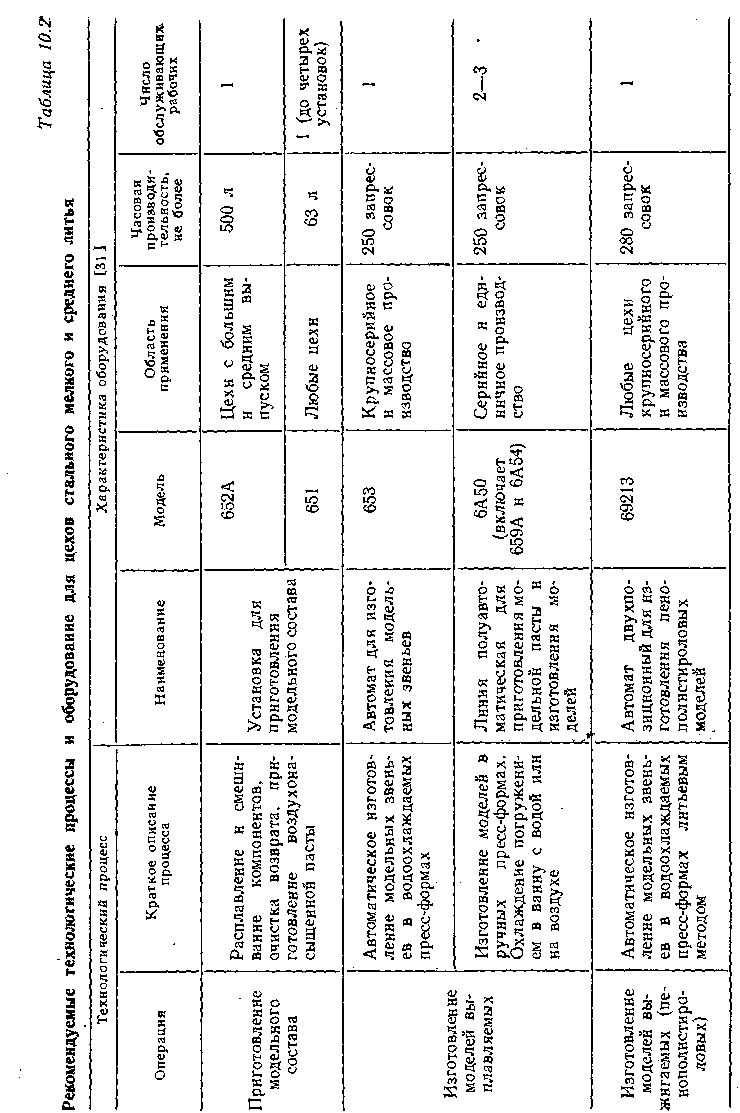
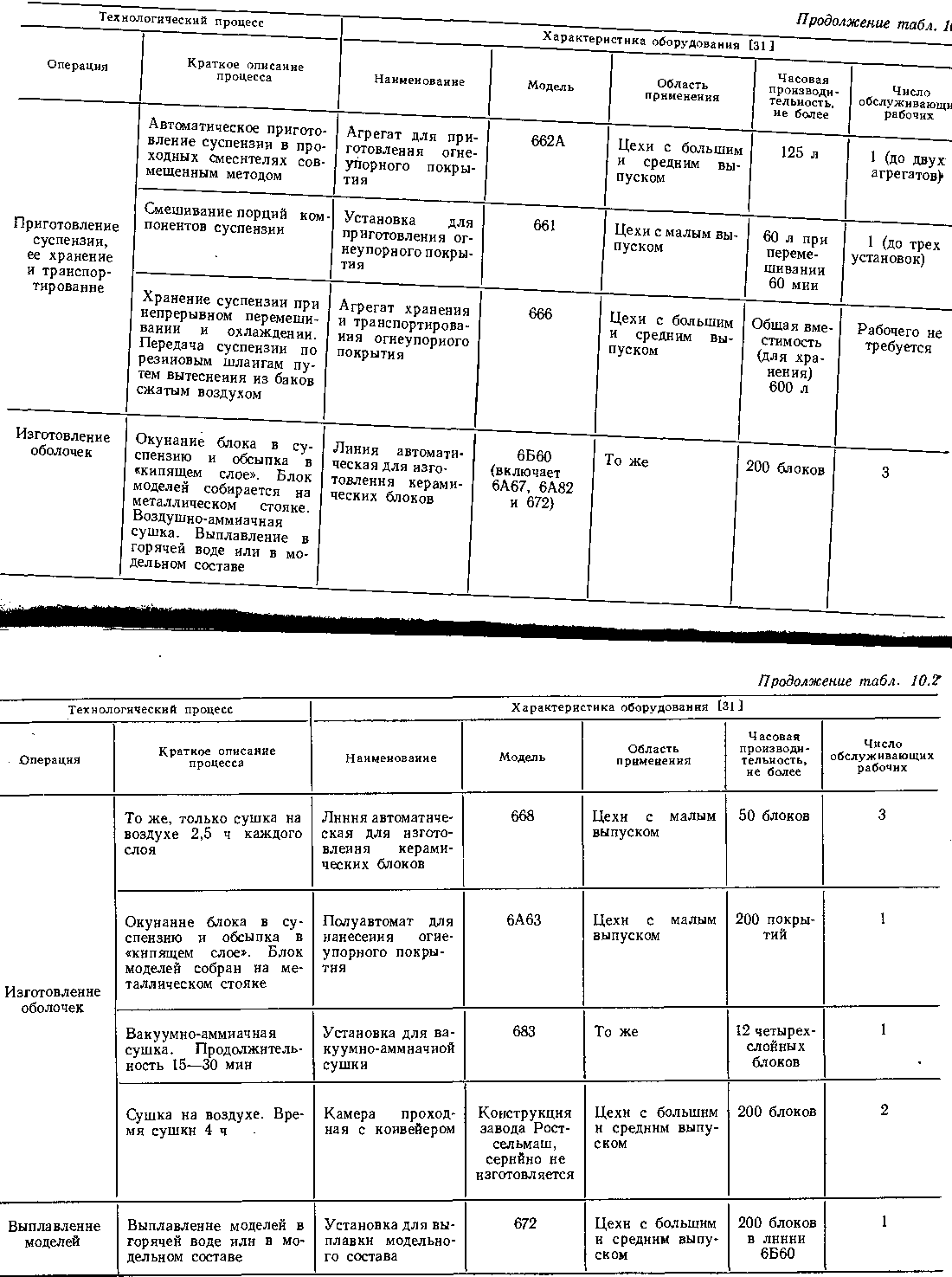
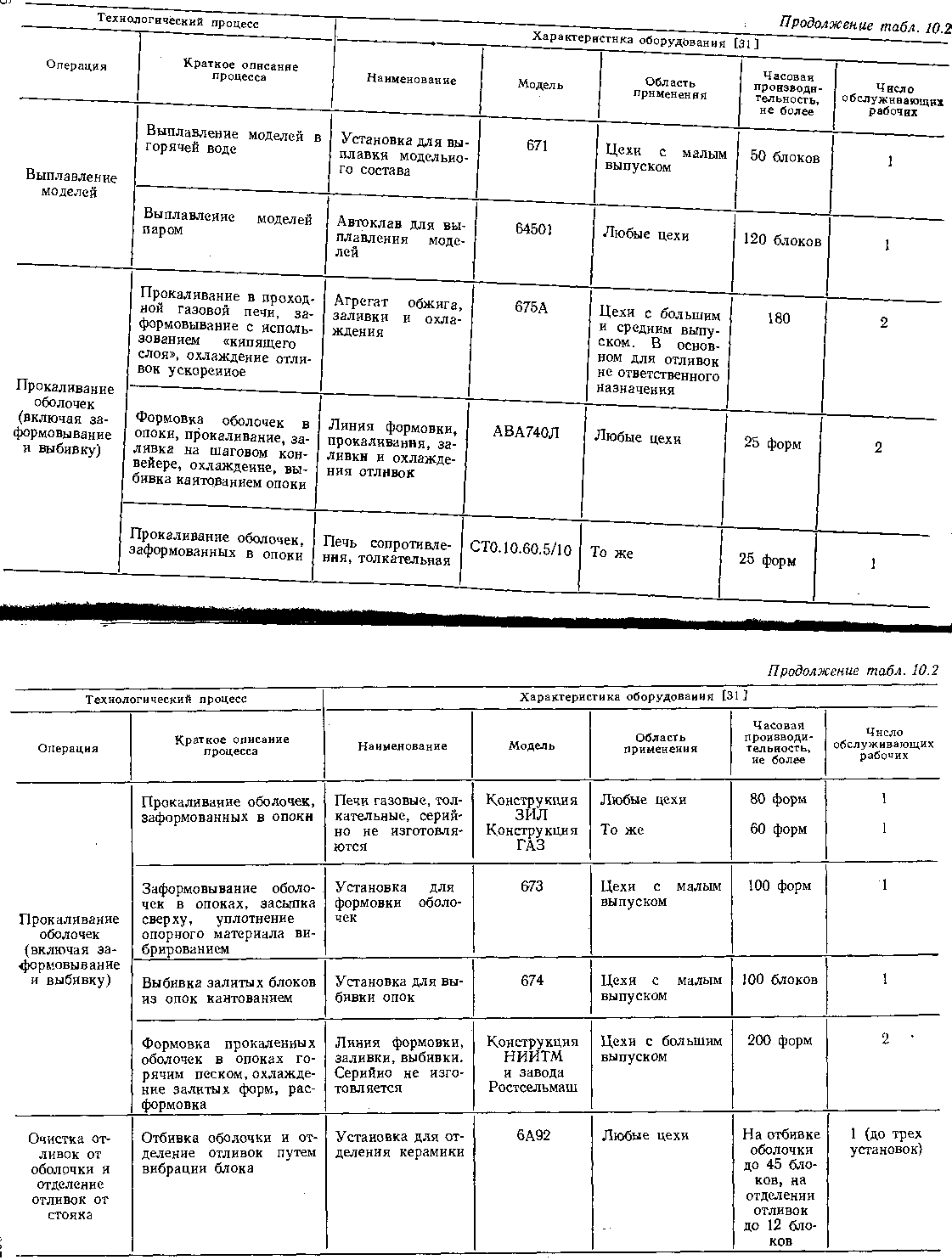
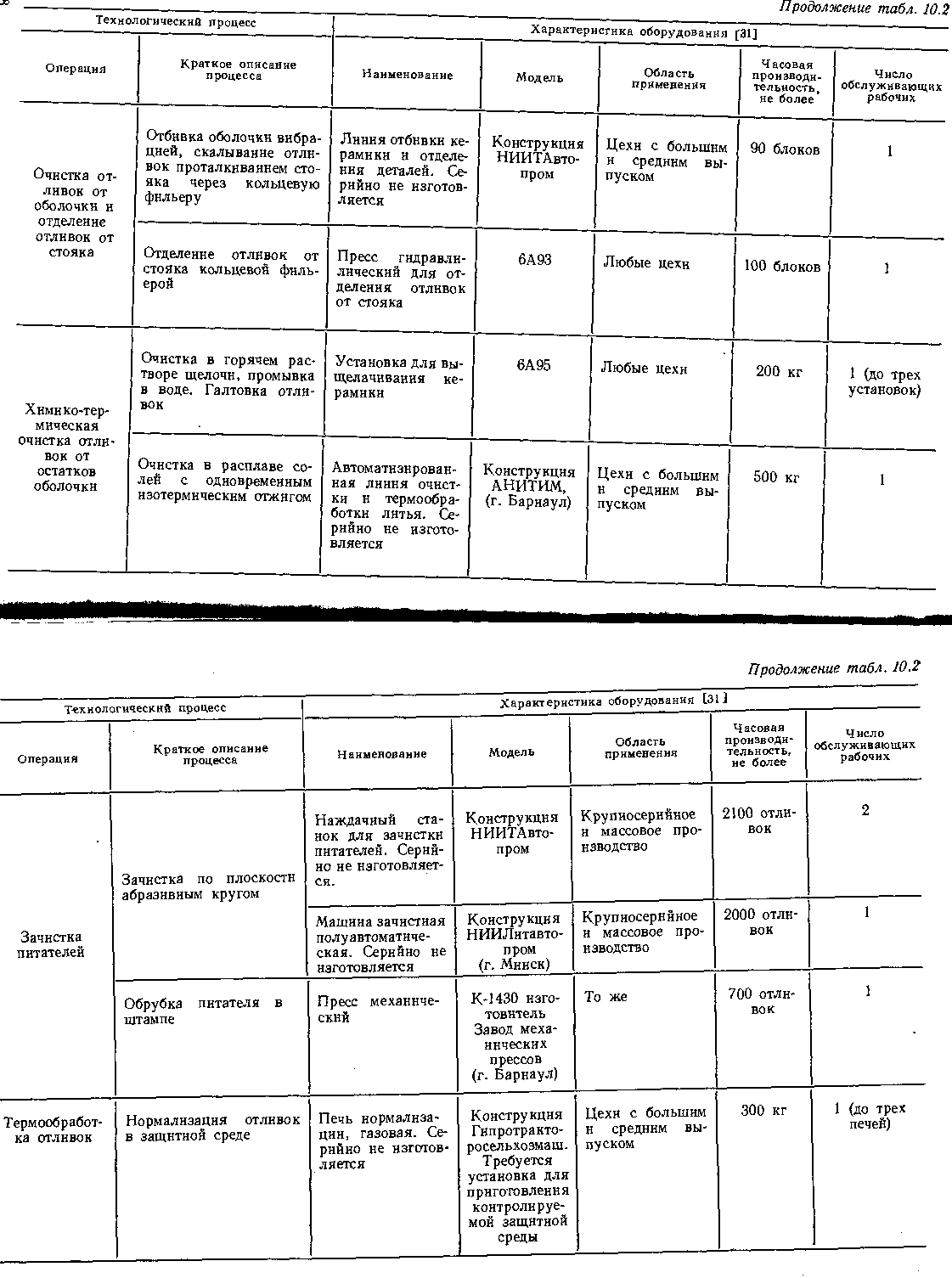
Для каждого производственного участка (группы операций) рассчитывают свой К, учитывающий потери и брак не только этой группы операций, но и всех последующих (табл. 10.3).
Таблица 10.3.
Примерные коэффициенты технологических потерь
Группа операций или производственный участок цеха | Те> нологиче-ские потери и брак, % | Коэффициенты технологических потерь |
Изготовление модельных блоков | 15 | 1,42 |
Изготовление форм | 3 | k 3 = 1,2 |
Обжнг форм, плавка н заливка металла | 5 | k 2 = 1,16 |
Обрубка, термообработка н отделка отлнвок | 9 | *1“ 1,1 |
Определив k
—k
,можно составлять ведомость объемов производства для расчета основного оборудования по форме 10.4.
Примечания. I. k — коэффициенты технологических потерь; n
— число моделей элементов литниковой системы на одни блок (чаша, металлопрнемннк н т. п.); — масса литников иа один блок; k
м — коэффициент, учитывающий потерн металла на угар, скрап, сливы и т. п., для стали &
1.06, для цветных сплавов k
м 1,08.
2. Массу суспензии рассчитывают в завиышости от числа £лоев по укрупненным показателям (см. табл. 10.4) или, если номенклатура отливок невелика, по поверхности отлнвок,.
Относительно точно расход суспензии на программу можно определить по суммарной поверхности модельных блоков. Средний расход суспензии на 1 дм
поверхности модели при нанесении одного слоя составляет 0,001 дм
или 16—17 г (при содержании в.
суспензии 72 % по массе пылевидного кварца). Пример расчета расхода компонентов суспензии приведен вгл. 11.
В табл. 10.4 приведены ориентировочные показатели для рас. четов исходных данных.
Таблица 10.4.
Ориентировочные показатели для стальных отливок средней сложности
Показатель | Группы | отливок по массе, кг | ||||||
До. 0,02 | 0,02 — 0,04 | 0,04 — 0,06 | 0,06 — 0,! | 0,1-. 0,2 | 0,2-. 0,6 | 0,6-. 1,5 | 1,5 н бьлее | |
Выход годного от зали | 21 | 34 | 40 | 44 | 48 | 53 | 57 | >57 |
того металла, % | ||||||||
Расход на 1 т годных | ||||||||
отливок, кг: | , ~ ч | |||||||
суспензии на один слой | 290 | 200 | 170 | 155 | 126 | 95 | ||
покрытия | ||||||||
модельного состава | 90 | 80 | 70 | 60 | 50 | : 45 / | 40 | |
(при 10 % потерь) | • ^ | |||||||
песка | 1300 | 1000 | ||||||
Количество перерабаты | 900 | 800 | 700 | 600 | 500 | 450 | 400 | |
ваемого модельного со | ||||||||
става на 1 т годных отли | ||||||||
вок, кг | ||||||||
Число отлнвок (моделей) | 100 | 80 | 60 | 40 | 20 | 10 | 6 | 4 |
в блоке длиной 500 мм |
Расчет числа оборудования. При проектировании цеха число каждого вида основного технологического оборудования определяют по формуле /
где В
—годовое количество перерабатываемого материала (суспензии, модельного состава, песка и т. д.) или число модельных звеньев, блоков, отливок; Н ■— часовая производительность единицы оборудования (размерность та же, что и для В
); ф
—действительный (расчетный) годовой фонд времени работы оборудования при выбранной сменности, ч (табл. 10.5).
В связи с тем, что в расчетном годовом фонде времени работы оборудования учитывают только потери времени на планово-предупредительный ремонт оборудования и не учитывают непредвиденные простой оборудования, при проектировании принимают к установке несколько большее число оборудования (с округлением в большую сторону, до целых единиц), чем получается по расчету.
Размер резерва, который должен компенсировать непредвиденные простои оборудования, характеризуется коэффициентом.загрузки оборудования :•*.» ,v».
где Рр —расчетное число оборудования; Р — принятое число, единиц оборудования.
Действительный (расчетный) годовой фонд времени работы оборудовании (рабочаи неделя 41 ч, в году восемь праздничных дней)
Оборудование | Число. смен | Номинальный годовой фонд времени, ч | Потерн, % номинального фонда времени | Действительный годовой фонд времени, ч |
Оборудование для приготовления | 1 | 2070 | 2 | 2030 |
модельного состава и суспензии, | 2 | 4140 | 4 | 3975 |
изготовления моделей и форм, вы | 3 | 6210 | 5 | 5900 |
плавления моделей, формовки и выбивки отливок, обрубки н очистки. То же, особо сложное | 2 | 4140 | 9 | 3770 |
3 | 6210 | 11 | 5525 | |
Автоматическое оборудование н ав | 2 | 4140 | 12 | 3645 |
томатические лннни | 3 | 6210 | 14 | 5340 |
Индукционные печи повышенной | 1 | 2070 | 4 | 1985 |
частоты для плавки стали, вмести | 2 | 4140 | 6 | 3890 |
мостью 0,06—2,5 т | 3 | 6490 | 12 | 5710 |
Печи плавильные: для медных сплавов | 1 | 1830 | 3 | 1775 |
2 | 3660 | 4 | 3510 | |
3 | 5490 | 6 | 5160 | |
для алюминиевых и других лег | 1 | 2070 | 3 | 2010 |
ких сплавов | 2 | 4140 | 4 | 3975 |
3 | 6210 | 6 | 5840 | |
Печи для прокаливания форм и термообработки отливок:. с непрерывным режимом работы, | 3 | 8760 | 11 | 7800 |
механизированные с коротким циклом работы, не- | 2 | 4140 | 4 | 3975 |
механизнрованные | 3 | 6210 | 6 | 5840 |
Примечание. Потери времени для оборудования определены, исходя нз его простоев, при планово-предупредительиом ремонте.
.
Коэффициент k
,
должен быть таким, чтобы обеспечивалось выполнение программы в реальных производственных условиях при отсутствии неиспользуемых производственных мощностей. Чем сложнее оборудование, тем оно менее надежно в работе, поэтому меньше должен быть &з.
. И наоборот, чем надежнее оборудование, тем ближе &з. о к единице.
Примерные значения k
в зависимости от сложности используемого оборудования:.
Несложное (например, установка для приготовления суспензии мод. 661,.
ванна выплавления моделей мод. 671) ................. 0,9.
Сложное (например, установка для приготовления модельного состава.
мод. 651, автомат для изготовления модельных звеньев мод. 653)..... 0,8.
Особо сложное (например, агрегат для приготовления суспензии мод. 662А, агрегат прокаливания, заливки и охлаждения мод. 675А)........ 0,7.
Состав работающих. Промышленно-производственный персонал цеха подразделяют на следующие категории: рабочие, инженерно-.
технические работники (ИТР), счетно-конторский персонал (СК.П) младший обслуживающий персонал (МОП). -Рабочих подразделяют на производственных и вспомогательных. Производственными называют рабочих, непосредственно связанных с изготовлением отливок.
При укрупненных расчетах число рабочих может быть принято по данным цеха-аналога.
Ориентировочные показатели для определения числа рабочих приведены в табл. 10.6.
.
Таблица 10.6.
Ориентировочные показатели для определения числа рабочих
Характеристика цеха | Средне | ||||
Отрасль. производства | Тил производства н годовой выпуск отливок, т | Степень. механизации | списочное число производственного персонала, чел. | Чи. сло. рабо. чих | Выпуск на одного рабочего, т/год |
Автомобилестрое. ние | Массовое. 7100 | Комплексная механизация и автоматизация | 796 | 708 | 10,03 |
4613 | То же | 821 | 738 | 6,25 | |
Мотовелостроение | Массовое. 1000 | Комплексная. механизация | 174 | 164 | 6,1 |
680 | Механизация | 140 | 126 | 5,39 | |
Тракторные двигатели | Массовое. 4300 | Комплексная механизация и автоматизация | 581 | 525 | 8,19 |
Сельскохозяй. ственные | Массовое. 3350 | То же | 391 | 352 | 9,52 |
Станкостроение | Разной серийности 2000 | » | 232 | 198 | 10,1 |
Производство текстильных и швейных машин | Массовое. 1580 | Комплексная. механизация | 180 | 161 | 9,81 |
Производство инструмента | Разной серийности 200 | Механизация | 45 | 40 | 5,0 |
Для более,, точного расчета нужно число производственных рабочих у оборудования (в том числе автоматического) определять на основании норм обслуживания этого оборудования, путем проектной расртановки рабочих по рабочим местам.
На ручных работах, там, где отсутствует принудительный темп работы оборудования и производительность зависит от рабочего, или там, где возможно выполнение рабочим нескольких операций либо обслуживание нескольких машин, число производственных рабочих определяют по трудоемкости этих работ (метод расчета приведен ниже).
Число вспомогательных рабочих либо определяют по рабочим местам и участкам цеха, по нормам обслуживания, либо, как при-вёдено ниже, принимают в процентном отношении к числу производственных рабочих:
Число ИТР, СКГ1 и МОП принимают в следующем процентном отношении к общему числу рабочих: 7 — 9 % ИТР; 0,6 — 1 % СК.П; 1,5 —2 % МОП.
Расчет числа производственных рабочих по трудоемкости работ. Требуемое число производственных рабочих для выполнения программы в целом по цеху или на зданную группу операций определяют по формуле
где 7’
— норма времени на изготовление отливок или на данную группу операций на годовую программу, ч; Т
— действительный (расчетный) годовой фонд времени рабочих, ч (табл. 10.7),
где Т
— норма времени на изготовление одной отливки или на выполнение данных операций на одну отливку, мин; п —число отливок на годовую программу;
t
— норма времени на выполнение отдельной операции на одну отливку, мин.
Таблица 10.7.
Действительный (расчетный) годовой фонд времени рабочих
Продолжительность рабочей недели, ч | Номинальный годовой фонд времени, ч | Продолжительность основного отпуска, дин | Потерн от номинального фонда времени, % | Действительный (расчетный) годовой фонд времени рабочего, ч |
41 | 2070 | 15 | 10 | 1860 |
41 | 2070 | 18 | 11 | 1840 |
41 | 2070 | 24 | 12 | 1820 |
36 | 1830 | 24 | 11 . | 1640 |
В условиях массового и крупносерийного производства нормы времени на отливку (штучное время) по отдельным операциям рассчитывают по формуле
где t
—оперативное время на операцию, принимаемое по общемашиностроительным нормативам времени на работы при литье по выплавляемым моделям, мин; а
бол — время на обслуживание рабо-.
чего места, а
= 4-~-6 % оперативного; а
— время на отдых н личные надобности, а
= 7-н9 % оперативного.
Площади. При укрупненных расчетах площадь цеха определяют по показателям выпуска (съема) годных отливок с 1 м
площади в тоннах. Этот показатель тем выше, чем выше серийность и масса отливок, уровень механизации, сменность работы цеха.
Для комплексно-механизированных цехов стального литья средней и большой мощности, спроектированных с учетом требований промышленной санитарии и техники безопасности, характерны следующие показатели: съем с 1 м
общей площади цеха (без бытовых) 0,3 — 0,5 т/год; съем с 1 м
производственной площади 0,4 — 0,7 т/год.
Для некоторых существующих участков и цехов, не имеющих собственных складов, отличающихся большой скученностью и недостаточно хорошими условиями труда, показатели съема в 1,4 — 1,5 раза выше указанных.
Точно площадь всех отделений цеха определяют разработкой плана расположения оборудования (см. с. 376 — 384.
Рассчитывают площади для складов, исходя из норм запасов материалов, насыпной массы (в укладке) материала и принятой высоты хранения.
Примерные нормы запасов для среднего климатического пояса на цеховом складе (при отсутствии базисного склада завода) следующие:

Ниже приведена насыпная (или в укладке) объемная масса материалов для расчета складов, т/м
8
:
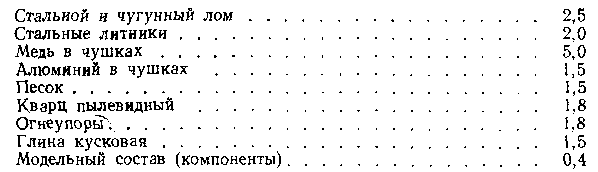
Площади (полезные) вспомогательных помещений культурно-бытового назначения принимают из расчета 5м
на одного работающего по списочному составу. В том числе по видам обслуживания: санитарно-гигиеническое — 3,5 м
; общественное питание — 0,78 м
; медицинское — 0,09 м
; культурно-массовое и цеховые общественные организации — 0,3 м
; местное бытовое обслуживание — 0,33 м
Энергетика. При разработке технологической части проекта определяют установленную мощность оборудования и среднюю активную нагрузку (кВт), расход основных видов энергоносителей:.
сжатого воздуха (м
), природного или сжиженного газа (м
), пара (т), а также воды (м
) на производственные нужды.
Данные о расходах энергоносителей и воды на технологические нужды сводятся в ведомости по форме 10.5.
Форма 10.5.
Расход - (вид и параметры энергоносителя, вода)
№ оборудования | Потребители по отделениям цеха | Коэффициент использования оборудования | Часовой. энергии. влениая | расход. (устаио-. мощиость) | Годовой. фоид. времени,. ч | Годовой. расход. энергии. (средняя. активная. нагрузка) |
по плану | иаи-. больший | средний | ||||
Капитальные затраты на оборудование. На стадии разработки технологической части проекта цеха в капитальных затратах на оборудование учитывают стоимость всего производственного, вспомогательного и подъемно-транспортного оборудования, а также дополнительные затраты, связанные с транспортированием и складированием этого оборудования, стоимостью его монтажа, стоимостью металлоконструкций и их монтажа, стоимостью инструмента, приспособлений, технологического и хозяйственного инвентаря.
Ниже приведены ориентировочные размеры капитальных затрат различных видов