Для расплавления модельного состава и поддержания его температуры в заданных пределах применяют водяные, глицериновые или масляные бани с устройством для автоматического регулирования температуры. Для заливки используют ковши из коррозионно-стойкой стали или фарфоровые. Заливают спокойно, по стенке литникового канала либо через воронку, вставленную в литниковое отверстие и подогретую до температуры заливки модельного состава. Это позволяет снизить потери теплоты модельного состава, устранить быстрое затвердевание его в литниковой системе и улучшить питание затвердевающей модели расплавом, находящимся в воронке. Во избежание разбрызгивания и вспенивания модельного состава, пос* ледний иногда заливают по стеклянному, фарфоровому или_сталь* ноУу стержню диаметром 4—6 мм.
При охлаждении и затвердевании в пресс-форме уровень расплава в воронке быстро снижается и для компенсации усадки необходимо доливать модельный состав. Литниковый ход в пресс-форме следует выполнять достаточно массивным, коротким и простым по форме.
Метод свободной заливки применяют в зарубежной практике при изготовлении ртутных моделей. Перед заливкой ртути форму заполняют ацетоном, вытесняющим воздух и выполняющим роль смазочного материала. Затем в форму заливают ртуть, которая вытесняет ацетон. Для затвердевания ртути пресс-форму погружают в ванну с ацетоном либо с другим веществом, имеющим более низкую температуру плавления, чем ртуть (температура плавления ртути —38,87 °С). Ацетон охлаждают с помощью сухого льда до температуры —60 °С и ниже, вследствие чего ртуть затвердевает, при этом
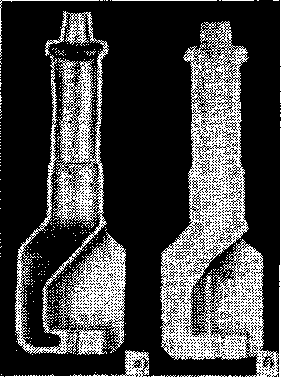
Рис. 5.25. Пустотелая (а) и сплошная (б) модели детали «тяга» в разрезе.
.
она практически не дает усадки, что обеспечивает высокую размерную точность моделей.
По ртутным моделям изготовляют сложные отливки высокой точности, например детали радиолокационных установок, турбинные лопатки, крыльчатки, уникальный режущий инструмент. Были отлиты стальные детали диаметром до 1050 мм и массой до 135 кг. На отечественных предприятиях ртутные модели не применяют ввиду вредного воздействия паров ртути на организм человека.
Свободной заливкой расплава получают как сплошные, так и полые модели.
Применение пустотелых моделей имеет следующие преимущества: повышается точность отливок по форме и размерам, сокращается время изготовления моделей, так как выдержка в пресс-форме уменьшается примерно в 3 раза, уменьшается масса модельного блока, устраняется растрескивание оболочки вследствие расширения моделей при выплавлении, сокращается время выплавления моделей.
В, серийном производстве наиболее доступным является следующий метод изготовления пустотелых моделей- Модельный расплав заливают в полостьпресс-формы, выдерживают в ней до образования по контуру полости затвердевшего слоя толщиной 1,5—3 мм, после чего незастывшую часть модельного состава выливают либо через отверстие в нижней части пресс-формы, либо через литниковый канал. Пустотелые модели целесообразно применять при изготовлении отливок с толщиной стенок более 10 мм, а также отливок, имеющих массивные части.
Преимущества пустотелых моделей видны на примере изготовления тяги, представляющей собой сравнительно массивную деталь с местными утолщениями (рис. 5.25).
В производственных условиях модели (рис. 5.25, б) изготовляли из модельного состава КПсЦ. Большинство моделей имело утяжину на скосе а. Применение пастообразной парафиново-стеариновой смеси уменьшило этот дефект, но не устранило его полностью. При отливке пустотелых моделей из парафиново-стеариновой смеси утя-жина на скосе (рис. 5.25, а) была полностью устранена. Толщину стенки полой модели выдерживали в пределах 2—2,5 мм. При меньшей толщине стенки прочность модели была недостаточной, а при большей — появлялись усадочные дефекты.
Рис. 5.26. Схемы процесса изготовления моделей:.
а — с подпрессовкой модельного состава сжатым воздухом после заполнения пресс-формы расплавом; б — с выдуванием незатвердевшей части модельного состава сжатым воздухом дЯ^люлучения полой (оболочковой) модели.
.
Таким образом, при изготовлении пустотелых моделей необходимо учитывать два важнейших фактора: точность и прочность» Применение модельных составов повышенной прочности позволяет уменьшить толщину стенки моделей до 2 мм.
В условиях крупносерийного и массового производства наиболее целесообразно применять способ изготовления пустотелых моделей, по которому незатвердевшую часть модельного состава удаляют продувкой сжатого воздуха. Воздух вдувают под избыточным давлением 0,2—0,3 МПа через литник и он выходит вместе с незатвердевшим модельным составом через отверстие в нижней части пресс» формы.
В зарубежной практике пустотелые модели изготовляют на пресс-машинах (рис. 5.26, а и б).